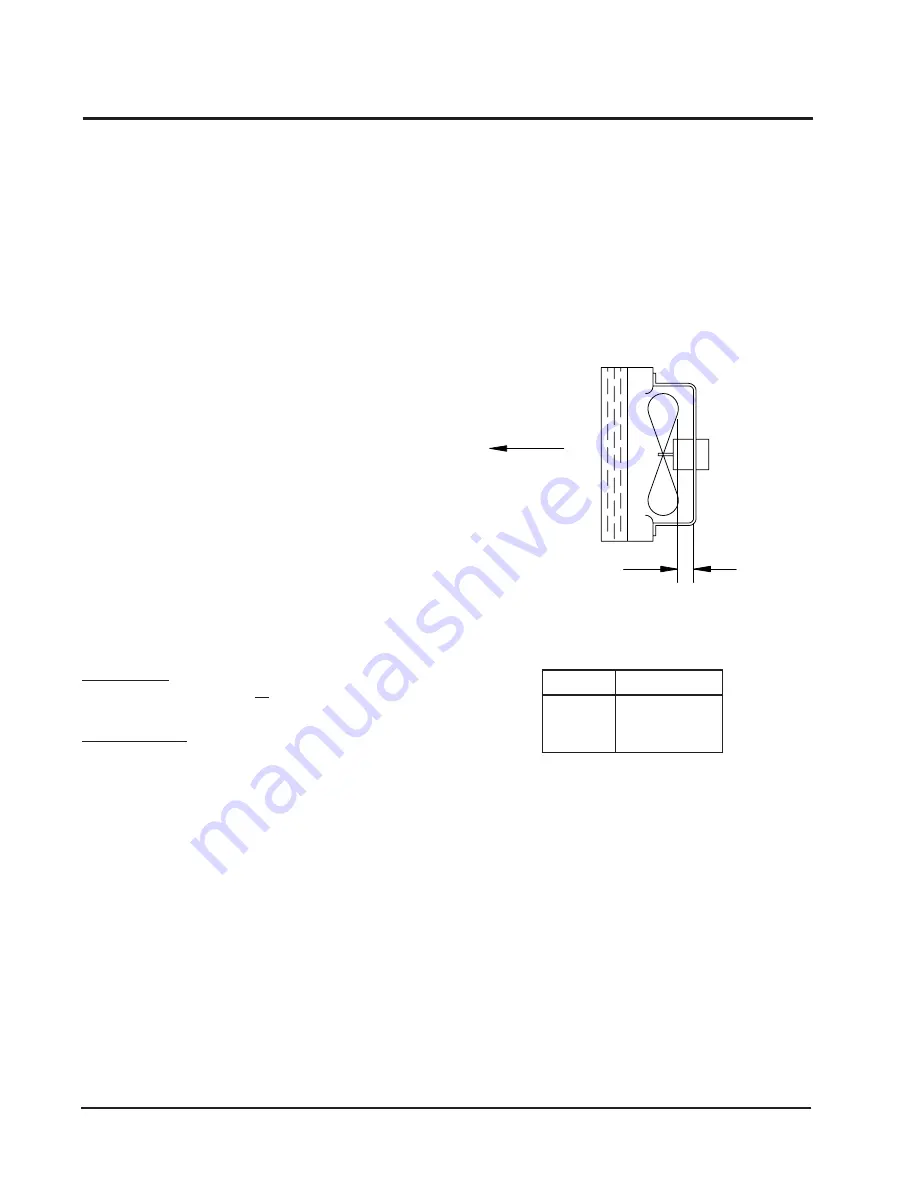
Manual 2100-451E
Page
18 of 24
FAN BLADE SETTING DIMENSIONS
Shown in the drawing below are the correct fan blade
setting dimensions for proper air delivery across the
outdoor coil. See Figure 9
Any service work requiring removal or adjustment in the
fan and/or motor area will require that the dimensions
below be checked and blade adjusted in or out on the
motor shaft accordingly. See Table 7.
TROUBLESHOOTING
COMPRESSOR SOLENOID
(See Sequence of Operation on Page 16 for function.)
A
nominal 24-volt direct current coil activates the internal
compressor solenoid. The input control circuit voltage
must be 18 to 28 volt ac. The coil power requirement is
20 VA. The external electrical connection is made with
a molded plug assembly. This plug contains a full wave
rectifier to supply direct current to the unloader coil.
Compressor Solenoid Test Procedure
If it is
suspected that the unloader is not working, the following
methods may be used to verify operation.
1. Operate the system and measure compressor
amperage. Cycle the compressor solenoid on and off
at ten-second intervals. The compressor amperage
should go up or down at least 25 percent.
2. If step one does not give the expected results, shut
unit off. Apply 18 to 28 volt ac to the solenoid
molded plug leads and listen for a click as the
solenoid pulls in. Remove power and listen for
another click as the solenoid returns to its original
position.
3. If clicks can’t be heard, shut off power and remove
the control circuit molded plug from the compressor
and measure the solenoid coil resistance. The
resistance should be 32 to 60 ohms depending on
compressor temperature.
4. Next, check the molded plug.
Voltage check
: Apply control voltage to the plug wires (18
to 28 volt ac). The measured
dc
voltage at the female
connectors in the plug should be around 15 to 27 vdc.
Resistance check
: Measure the resistance from the end of
one molded plug lead to either of the two female connectors
in the plug. One of the connectors should read close to zero
ohms, while the other should read infinity. Repeat with
other wire. The same female connector as before should
read zero, while the other connector again reads infinity.
Reverse polarity on the ohmmeter leads and repeat. The
female connector that read infinity previously should now
read close to zero ohms.
Replace plug if either of these test methods does not
show the desired results.
FIGURE 9
FAN BLADE SETTING
REMOVAL OF FAN SHROUD
1. Disconnect all power to unit.
2. Remove the screws holding both grills – one on
each side of unit – and remove grills.
3. Remove screws holding fan shroud to condenser and
bottom – (9) screws.
4. Unwire condenser fan motor.
5. Slide complete motor, fan blade, and shroud
assembly out the left side of the unit.
6. Service motor/fan as needed.
7. Reverse steps to reinstall.
TABLE 7
FAN BLADE DIMENSIONS
l
e
d
o
M
A
n
o
i
s
n
e
m
i
D
1
S
3
A
W
1
S
4
A
W
1
S
5
A
W
"
5
7
.
1
"A"
AIRFLOW
MIS-1724