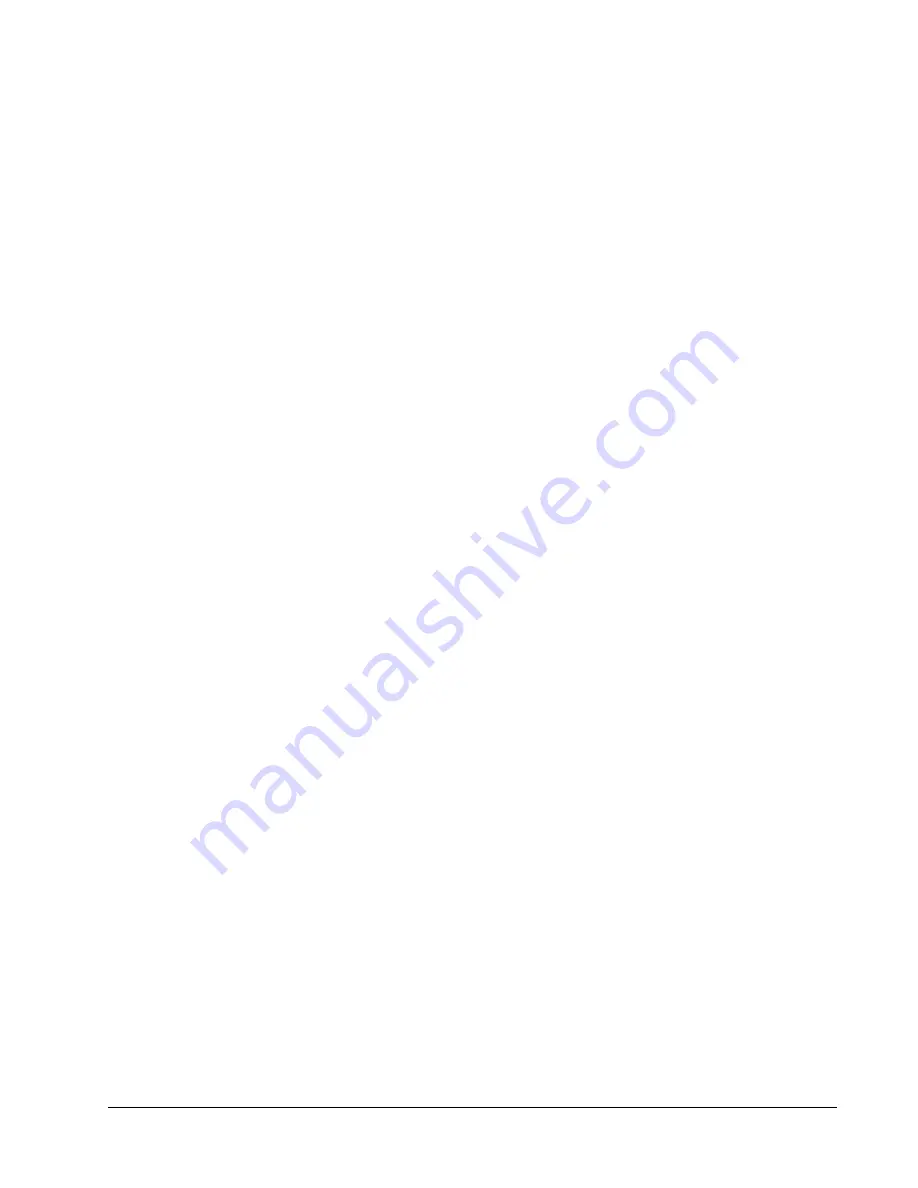
Manual 2100-408C
Page
17
HEATING SEQUENCE
– On a call for heating, the
compressor and reversing valve of the unit are energized
to provide heat pump heating. If the room temperature
falls below the 2nd stage heating set point backup
electric heat is energized. Heat pump heating is only
available when the timer is energized. If heating is
energized any call for dehumidification is ignored. If
dehumidification is already energized a call for 2nd
stage heating is needed to cancel dehumidification
mode.
A 24V solenoid coil on reversing valve controls heating
cycle operation. A thermostat demand for heat
completes R-W1 circuit, pulling in compressor contactor
starting compressor and outdoor motor. R-G also make
starting indoor blower motor.
DEHUMIDIFICATION SEQUENCE
– On a call for
dehumidification the compressor and three way valve of
the unit are energized to provide dehumidification.
Dehumidification mode will continue until the
humidistat is satisfied. If the room temperature falls
below 1st stage heating setpoint, electric heat will be
energized by the room thermostat and cycle to maintain
room temperature. If 2nd stage heating setpoint is
reached, dehumidification is de-energized and heat pump
heating is energized. A call for cooling cancels
dehumidification mode. Refer to Figure 14.
UNOCCUPIED MODE
Cooling, heating, emergency heat and ventilation are
inhibited.
DEHUMIDIFICATION SEQUENCE
– On a call for
dehumidification the compressor and three way valve of
the unit are energized to provide dehumidification.
Dehumidification mode will continue until the
humidistat is satisfied. If the room temperature falls
below 65 degrees and dehumidification is energized,
electric heat will be energized by the return air
thermostat and cycle to maintain room temperature.
PRESSURE SERVICE PORTS
High and low pressure service ports are installed on all
units so that the system operating pressures can be
observed. Pressure tables can be found later in the
manual covering all models on both cooling and heating
cycles. It is imperative to match the correct pressure
curve to the unit by model number.
DEFROST CYCLE
The defrost cycle is controlled by temperature and time
on the solid state heat pump control. See Figure 11.
When the outdoor temperature is in the lower 40° F
temperature range or colder, the outdoor coil
temperature is 32° F or below. This coil temperature is
sensed by the coil temperature sensor mounted near the
bottom of the outdoor coil. Once coil temperature
reaches 30° F or below, the coil temperature sensor
sends a signal to the control logic of the heat pump
control and the defrost timer will start.
After 60 minutes at 30° F or below, the heat pump
control will place the system in the defrost mode.
During the defrost mode, the refrigerant cycle switches
back to the cooling cycle, the outdoor motor stops,
electric heaters are energized, and hot gas passing
through the outdoor coil melts any accumulated frost.
When the temperature rises to approximately 57° F, the
coil temperature sensor will send a signal to the heat
pump control which will return the system to heating
operations automatically.
If some abnormal or temporary condition such as a high
wind causes the heat pump to have a prolonged defrost
cycle, the heat pump control will restore the system to
heating operation automatically after 10 minutes.
The heat pump defrost control board has an option of
30, 60 or 90 minutes setting. All models are shipped
from the factory on the 60-minute pin. If special
circumstances require a change to another time, remove
the wire from the 60-minute terminal and reconnect to
the desired terminal. The manufacturer's
recommendation is for 60-minute defrost cycles. Refer
to Figure 11.
There is a cycle speed up jumper on the control. This
can be used to reduce the time between defrost cycle
operation without waiting for time to elapse.
Use a small screwdriver or other metallic object, or
another 1/4 inch QC, to short between the
SPEEDUP
terminals to accelerate the HPC timer and initiate
defrost.
Be careful not to touch any other terminals with the
instrument used to short the
SPEEDUP
terminals. It
may take up to 10 seconds with the
SPEEDUP
terminals shorted for the speedup to be completed and
the defrost cycle to start.
As soon as the defrost cycle kicks in remove the
shorting instrument from the SPEEDUP terminals.
Otherwise the timing will remain accelerated and run
through the 1-minute minimum defrost length sequence
in a matter of seconds and will automatically terminate
the defrost sequence.