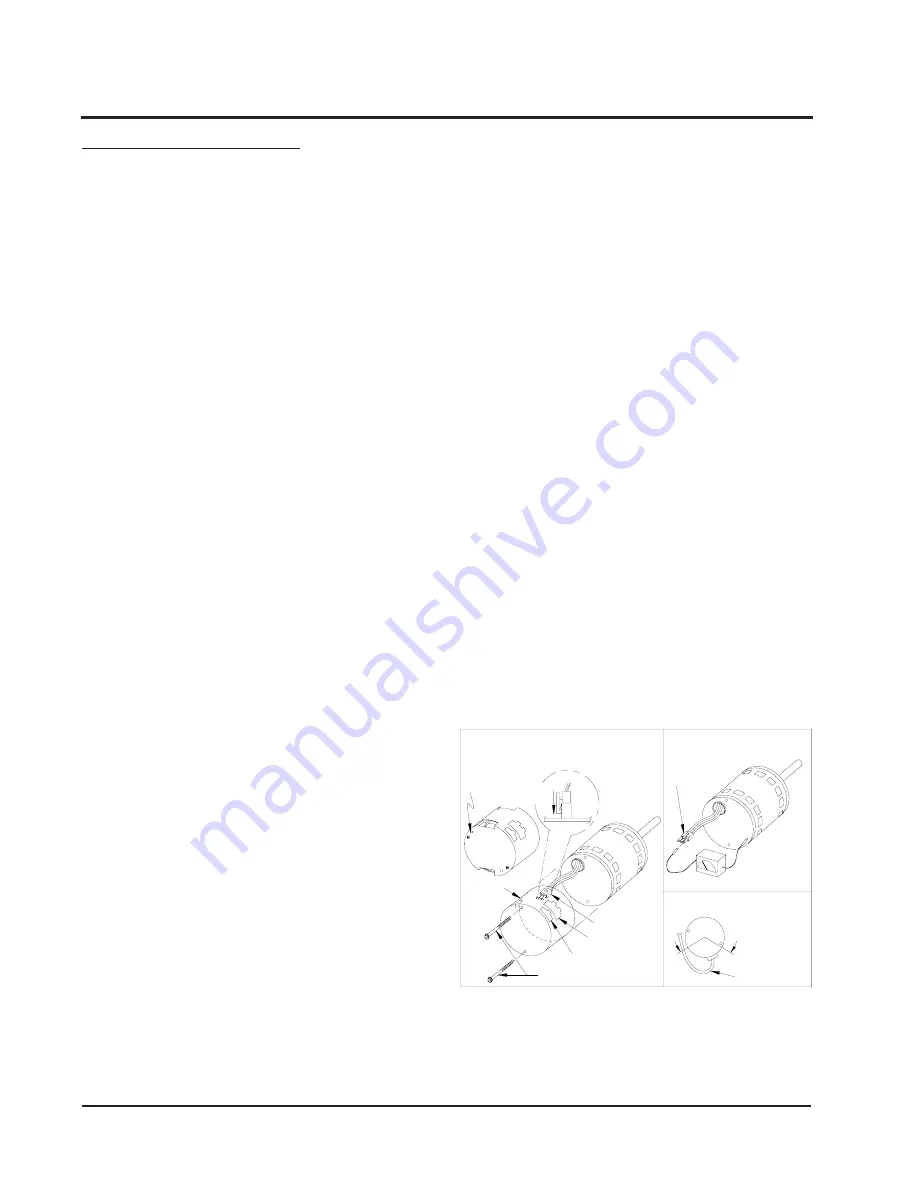
Manual
2100-532B
Page
43 of 46
TROUBLESHOOTING GE ECM
™
MOTORS CONT’D.
Motor
Motor OK when
R > 100k ohm
ECM 2.0
Only remove
Hex Head Bolts
Connector Orientation
Between 4 and 8 o'clock
Drip Loop
Back of
Control
Figure 5
Winding Test
Figure 4
Note:
Use the shorter
bolts and
alignment pin
supplied when
replacing an
ECM 2.0
control.
Figure 3
ECM
2.3/2.5
Power Connector
(5-pin)
Control Connector
(16-pin)
Hex-head Screws
Motor Connector
(3-pin)
Motor Connector
(3-pin)
Control Disassembly
Drip Loop
Push until
Latch Seats
Over Ramp
From Motor
Circuit
Board
Replacing ECM Control Module
To replace the control module for the GE variable-speed indoor blower
motor you need to take the following steps:
1. You MUST have the correct replacement module. The controls are
factory programmed for specific operating modes. Even though they look
alike, different modules may have completely different functionality.
USING THE WRONG CONTROL MODULE VOIDS ALL PRODUCT
WARRANTIES AND MAY PRODUCE UNEXPECTED RESULTS.
2. Begin by removing AC power from the furnace or air handler being
serviced.
DO NOT WORK ON THE MOTOR WITH AC POWER
APPLIED.
To avoid electric shock from the motor’s capacitors, disconnect
power and wait at least 5 minutes before opening motor.
3. It is usually not necessary to remove the motor from the blower
assembly. However, it is recommended that the whole blower assembly,
with the motor, be removed from the furnace/air handler. (Follow the
manufacturer’s procedures). Unplug the two cable connectors to the motor.
There are latches on each connector.
DO NOT PULL ON THE WIRES.
The plugs remove easily when properly released.
4. Locate the two standard ¼" hex head bolts at the rear of the control
housing (at the back end of the control opposite the shaft end).
Refer
to Figure 28.
Remove these two bolts from the motor and control
assembly while holding the motor in a way that will prevent the motor
or control from falling when the bolts are removed. If an ECM2.0
control is being replaced (recognized by an aluminum casting rather
that a deep-drawn black steel can housing the electronics), remove
only the hex-head bolts.
DO NOT REMOVE THE TORX-HEAD
SCREWS.
5. The control module is now free of mechanical attachment to the
motor endshield but is still connected by a plug and three wires inside
the control. Carefully rotate the control to gain access to the plug at
the control end of the wires. With thumb and forefinger, reach the
latch holding the plug to the control and release it by squeezing the
latch tab and the opposite side of the connector plug and gently pulling
the plug out of the connector socket in the control.
DO NOT PULL
ON THE WIRES. GRIP THE PLUG ONLY.
6. The control module is now completely detached from the motor.
Verify with a standard ohmmeter that the resistance from each motor
lead (in the motor plug just removed) to the motor shell is >100K ohms.
Refer to Figure 29.
(Measure to unpainted motor end plate.) If any
motor lead fails this test, do not proceed to install the control module.
THE MOTOR IS DEFECTIVE AND MUST BE REPLACED.
Installing the new control module will cause it to fail also.
7. Verify that the replacement control is correct for your
application. Refer to the manufacturer's authorized replacement list.
USING THE WRONG CONTROL WILL RESULT IN
IMPROPER OR NO BLOWER OPERATION.
Orient the control
module so that the 3-wire motor plug can be inserted into the socket in
the control. Carefully insert the plug and press it into the socket until
it latches.
A SLIGHT CLICK WILL BE HEARD WHEN
PROPERLY INSERTED.
Finish installing the replacement control per
one of the three following paragraphs, 8a, 8b or 8c.
8a.
IF REPLACING AN ECM 2.0 CONTROL
(control in cast
aluminum can with air vents on the back of the can)
WITH AN ECM
2.3 CONTROL
(control containing black potting for water protection in
black deep-drawn steel case with no vents in the bottom of the can),
locate the two through-bolts and plastic tab that are packed with the
replacement control. Insert the plastic tab into the slot at the perimeter
of the open end of the can so that the pin is located on the inside of the
perimeter of the can. Rotate the can so that the tab inserts into the tab
locater hole in the endshield of the motor. Using the two through-bolts
provided with the replacement control, reattach the can to the motor.
THE TWO THROUGH-BOLTS PROVIDED WITH THE
REPLACEMENT ECM 2.3 CONTROL ARE SHORTER THAN
THE BOLTS ORIGINALLY REMOVED FROM THE ECM 2.0
CONTROL AND MUST BE USED IF SECURE ATTACHMENT
OF THE CONTROL TO THE MOTOR IS TO BE ACHIEVED.
DO NOT OVERTIGHTEN THE BOLTS.
8b.
IF REPLACING AN ECM 2.3 CONTROL
WITH AN ECM
2.3 CONTROL
, the plastic tab and shorter through-bolts are not
needed. The control can be oriented in two positions 180° apart.
MAKE SURE THE ORIENTATION YOU SELECT FOR
REPLACING THE CONTROL ASSURES THE CONTROL'S
CABLE CONNECTORS WILL BE LOCATED DOWNWARD IN
THE APPLICATION SO THAT WATER CANNOT RUN DOWN
THE CABLES AND INTO THE CONTROL.
Simply orient the
new control to the motor's endshield, insert bolts, and tighten.
DO
NOT OVERTIGHTEN THE BOLTS.
8c.
IF REPLACING AN ECM 2.0 CONTROL WITH AN ECM
2.0 CONTROL
(It is recommended that ECM 2.3 controls be used for
all replacements),
the new control must be attached to the motor using
through bolts identical to those removed with the original control.
DO
NOT OVERTIGHTEN THE BOLTS.
9. Reinstall the blower/motor assembly into the HVAC equipment.
Follow the manufacturer's suggested procedures.
10. Plug the 16-pin control plug into the motor. The plug is keyed.
Make sure the connector is properly seated and latched.
11. Plug the 5-pin power connector into the motor. Even though the
plug is keyed,
OBSERVE THE PROPER ORIENTATION. DO
NOT FORCE THE CONNECTOR.
It plugs in very easily when
properly oriented.
REVERSING THIS PLUG WILL CAUSE
IMMEDIATE FAILURE OF THE CONTROL MODULE.
12. Final installation check. Make sure the motor is installed as
follows:
a. Unit is as far INTO the blower housing as possible.
b.Belly bands are not on the control module or covering vent
holes.
c. Motor connectors should be oriented between the 4 o’clock
and 8 o’clock positions when the blower is positioned in its
final location and orientation.
d.Add a drip loop to the cables so that water cannot enter the
motor by draining down the cables.
Refer to Figure 30.
The installation is now complete. Reapply the AC power to the
HVAC equipment and verify that the new motor control module is
working properly. Follow the manufacturer's procedures for
disposition of the old control module.
Figure 29
Figure 28
Figure 30