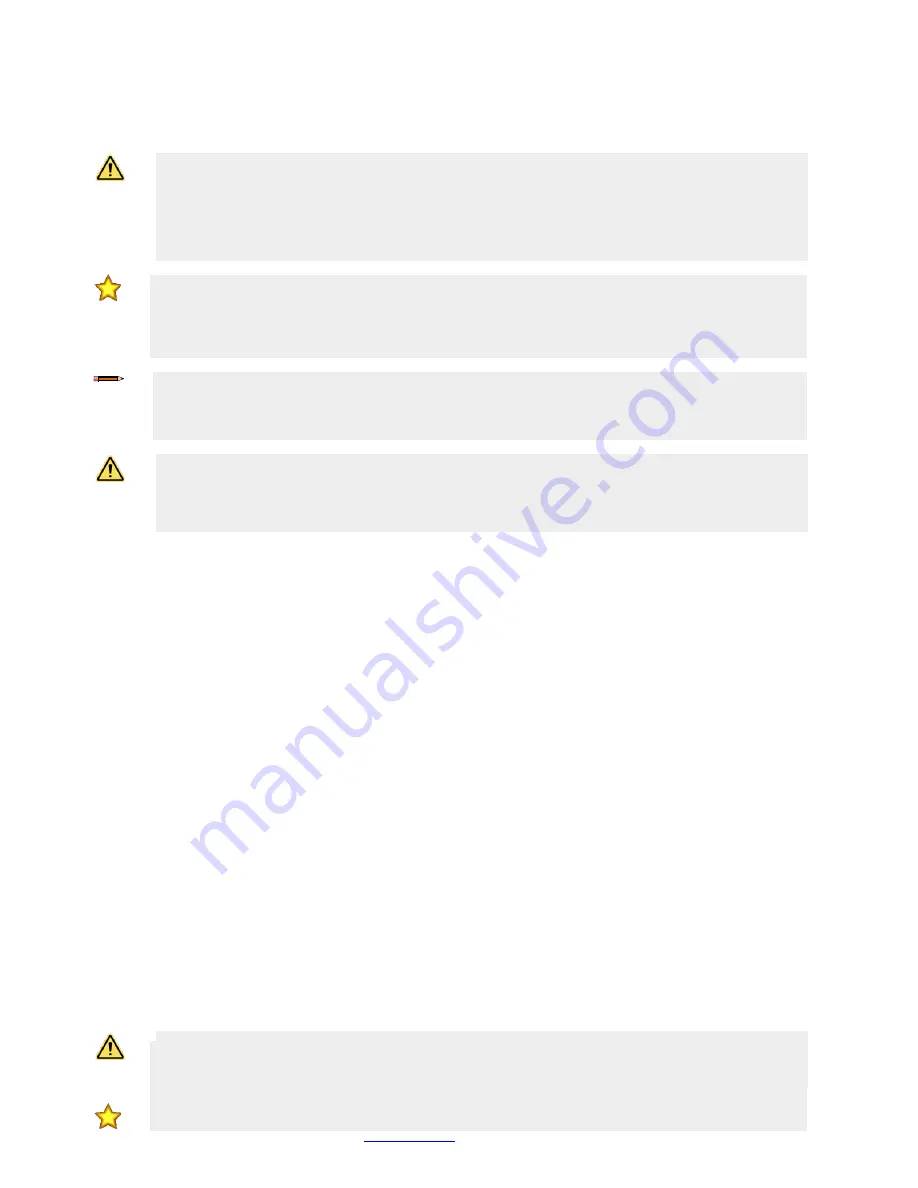
Programmable Safety Controller SCR P
www.bernstein.eu
- Tel: + 49 571 793 0
37
The reset switch must be mounted at a location that complies with the warning below.
A key-actuated reset switch
provides some operator or supervisory control, as the key can be removed from the switch and taken into the guarded area.
However, this does not prevent from any unauthorized or inadvertent resets due to spare keys being in the possession of
others, or additional personnel entering the guarded area unnoticed (a pass-through hazard).
Automatic and Manual Reset Inputs Mapped to the Same Safety Output
By default, Safety Outputs are configured for automatic reset (trip mode). They can be configured as a Latch Reset using
the Solid State Output Properties attribute of the Safety Output (see
Safety Input Devices operate as automatic reset unless a Latch Reset Block is added. If a Latch Reset Block is added in line
with an output configured for Latch Reset mode, the same or different Manual Reset Input Device(s) may be used to reset
the Latch Reset Block and the Safety Output latch. If the same Manual Reset Input Device is used for both, and all inputs
are in their Run state, a single reset action will unlatch the function block and the output block. If different Manual Reset
Input Devices are used, the reset associated with the Safety Output must be the last one activated. This can be used to
force a sequenced reset routine, which can be used to reduce or eliminate pass-through hazards in perimeter guarding
applications (see
Safety Input Device Properties
If the controlling inputs to a Latch Reset Block or a Safety Output Block are not in the Run state, the reset for that block will
be ignored.
Reset Signal Requirements
Reset Input devices can be configured for monitored or non-monitored operation, as follows:
Monitored reset:
Requires the reset signal to transition from low (0 V dc) to high (24 V dc) and then back to low. The high
state duration must be 0.5 seconds to 2 seconds. This is called a trailing edge event.
Non-monitored reset:
Requires only that the reset signal transitions from low (0 V dc) to high (24 V dc) and stays high for at
least 0.5 seconds. After the reset, the reset signal can be either high or low. This is called a leading-edge event.
6.6 Virtual Non-Safety Input Devices
The virtual non-safety input devices include manual reset, On/Off, mute enable, and cancel off delay.
WARNING: Reset Switch Location
All reset switches must be accessible only from outside, and in full view of, the hazardous area. Reset
switches must also be out of reach from within the safeguarded space, and must be protected against
unauthorized or inadvertent operation
(for example, through the use of rings or guards). If any areas are
not visible from the reset switch(es), additional means of safeguarding must be provided.
Failure to follow
these instructions could result in serious injury or death.
Important:
Resetting a safeguard must not initiate hazardous motion. Safe work procedures require a
start-up procedure to be followed and the individual performing the reset to verify that the entire
hazardous area is clear of all personnel
before each reset of the safeguard is performed
. If any area
cannot be observed from the reset switch location, additional supplemental safeguarding must be used:
at a minimum, visual and audible warnings of the machine start-up.
Note: Automatic Reset
sets an output to return to an On state without action by an individual once the
input device(s) changes to the Run state and all other logic blocks are in their Run state. Also known as
"Trip mode," automatic reset is typically used in applications in which the individual is continually being
sensed by the safety input device.
WARNING: Automatic Power Up
On power up, the Safety Outputs and Latch Reset Blocks configured for automatic power up will turn
their outputs On if all associated inputs are in the Run state. If manual reset is required, configure outputs
for a manual power mode.
WARNING:
Virtual Non-Safety Inputs must never be used to control any safety-critical applications. If a
Virtual Non-Safety Input is used to control a safety-critical application, a failure to danger is possible and
may lead to serious injury or death.
Important:
Resetting a safeguard must not initiate hazardous motion. Safe work procedures require a
start-up procedure to be followed and the individual performing the reset to verify that the entire
hazardous area is clear of all personnel before each reset of the safeguard is performed. If any area
cannot be observed from the reset switch location, additional supplemental safeguarding must be used:
at a minimum, visual and audible warnings of the machine start-up.