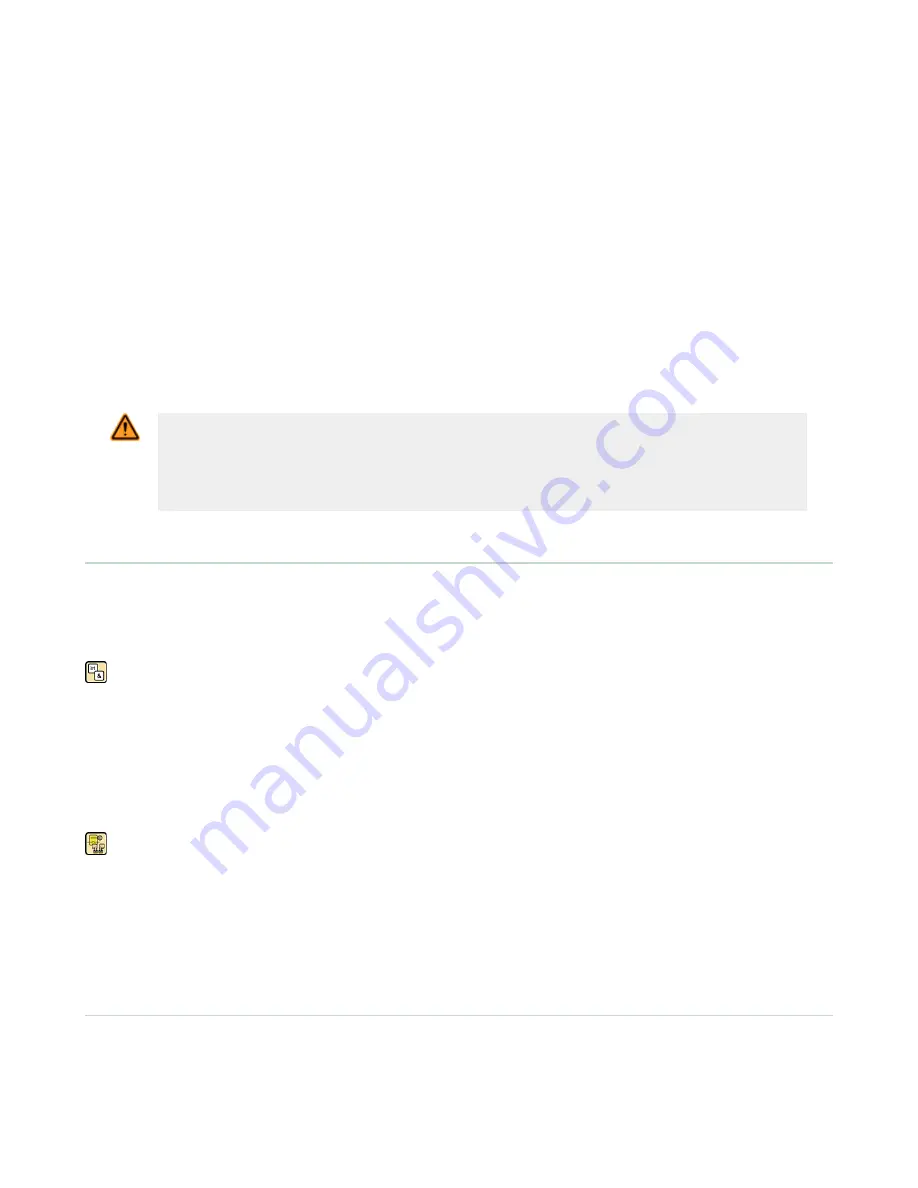
Functional Stops according to IEC 60204-1 and ANSI NFPA79
The Controller is capable of performing two functional stop types:
•
Category 0: an uncontrolled stop with the immediate removal of power from the guarded machine
•
Category 1: a controlled stop with a delay before power is removed from the guarded machine
Delayed stops can be used in applications where machines need power for a braking mechanism to stop the hazardous
motion.
2.7.3 Status Outputs and Virtual Status Outputs
The Base Controller has eight convertible I/Os (labeled IOx) that can be used as Status Outputs which have the capability
to send non-safety status signals to devices such as programmable logic controllers (PLCs) or indicator lights. In addition,
any unused Safety Output terminals may be configured to perform a Status Output function with the benefit of higher
current capacity (see
on page 11 for more information). The Status Output signal convention can be
configured to be 24 V dc or 0 V dc. See
Status Output Signal Conventions
on page 95 for information on the specific
functions of a Status Output.
Ethernet models, using the PC Interface, can be configured for up to 64 Virtual Status Outputs. These outputs can
communicate the same information as the status outputs over the network. See
on page 96 for
more information.
WARNING: Status Outputs and Virtual Status Outputs
Status Outputs and Virtual Status Outputs are not safety outputs and can fail in either the On or the Off
state. They must never be used to control any safety-critical applications. If a Status Output
or a Virtual Status Output is used to control a safety-critical application, a failure to danger is
possible and may lead to serious injury or death.
2.8 Internal Logic
The Safety Controller’s internal logic is designed so that a Safety Output can turn On only if all the controlling safety input
device signals and the Controller’s self-check signals are in the Run state and report that there is no fault condition.
The XS26-2 Expandable Safety Controller configuration software uses both Logic and Safety Function blocks for simple and
more advanced applications.
Logic Blocks are based on Boolean (True or False) logic laws. The following Logic Blocks are available:
•
NOT
•
AND
•
OR
•
NAND
•
NOR
•
XOR
•
Flip Flop (Set priority and Reset priority)
See
on page 24 for more information.
Function Blocks are pre-programmed blocks with built-in logic which provide various attribute selections to serve both
common and complex application needs. The following Function Blocks are available:
•
Bypass Block
•
Enabling Device Block
•
Latch Reset Block
•
Muting Block
•
THC (Two-Hand Control) Block
See
on page 26 for more information.
2.9 Password Overview
A password is required to confirm and save the configuration to the device and to access the Password Manager via the PC
Interface. See
on page 53 for more information.
XS/SC26-2 Safety Controller
9