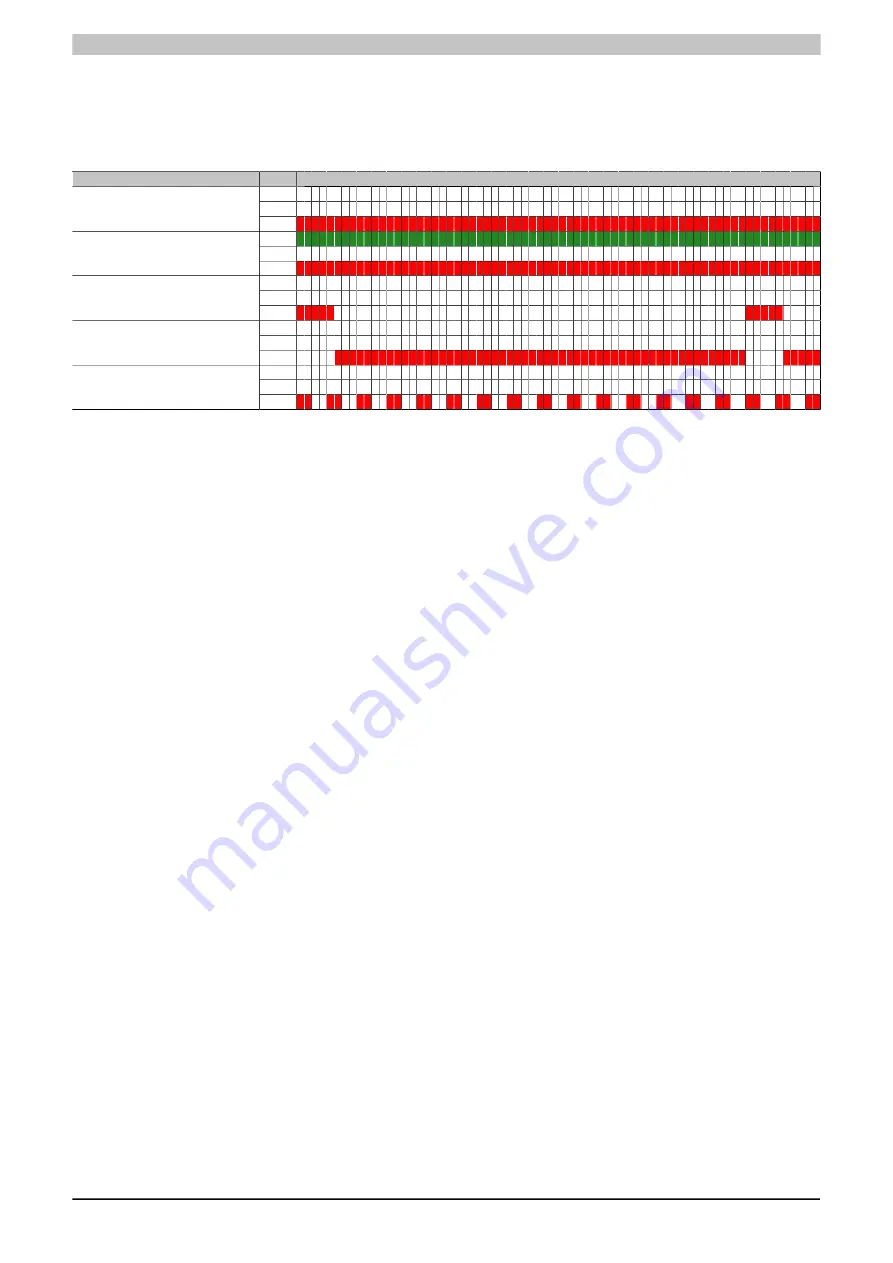
8BVI0014HWD0.000-1
Data sheet V 1.4
7
4.4 Status changes when booting the operating system loader
The following timing is used for the LED status indicators:
Block size: 50 ms
Repeats after: 3,000 ms
Status
LED
Indicator
RDY
RUN
1. Boot procedure for base hardware
active
ERR
RDY
RUN
2. Network configuration active
ERR
RDY
RUN
3. Waiting for network telegram
ERR
RDY
RUN
4. Network communication active
ERR
RDY
RUN
5. ACOPOS operating system being
transferred/burned
1)
ERR
Table 7: Status changes when booting the operating system loader
1)
Firmware V2.140 and higher.