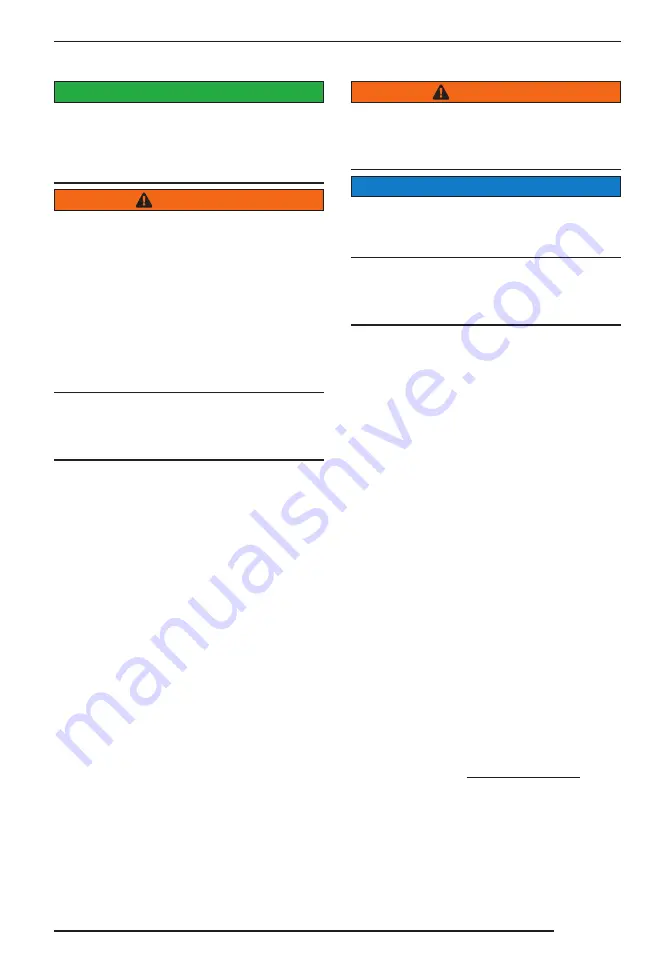
Bandit
43
MODEL 12X
HYDRAULICS
HYDRAULICS
Do not go near hydraulic leaks. High pressure
oil easily punctures skin causing serious injury,
gangrene, or death. Avoid burns from fluid. Hot
fluid under pressure can cause severe burns. Do
not use fingers or skin to check for leaks. Lower
load or relieve hydraulic pressure before loosening
fittings. Relieve all pressure in the system before
disconnecting the lines, hoses, or performing other
work. Use a piece of cardboard to find leaks. Never
use your bare hands. Allow system to cool down to
ambient temperature before opening any coolant or
hydraulic oil system.
Some equipment and components including
fluid engagement clutches (PTO’s) have their
own lubrication requirements. Consult their
manufacturer’s manual for that information.
When returning hydraulic components for
warranty make sure to box up all warranted
parts to avoid additional damage while shipping.
Do not disassemble any hydraulic components
which are to be warrantied. Anything which has
been disassembled or tampered with will not be
warrantied. Items being returned must be clean. All
hydraulic components must have all hosing ports
plugged. Failure to plug ports will allow debris to
enter components which will void warranty.
Before attempting any type of maintenance,
disengage clutch, wait for the drum to come to a complete
stop, turn off engine, remove the ignition key, make
sure the ignition key is in your possession, install the
drum lock pin, and disconnect the battery.
After the initial start-up of the machine and after
any replacement of hydraulic components, fittings
and hoses must be re-checked for leaks and
clearances.
It is very important after you have operated a new
machine for approximately an hour to shut down the
machine and recheck all hydraulic fittings. Relieve all
pressure and retighten as needed.
Do not operate this machine unless all hydraulic
control devices operate properly. They must function,
shift and position smoothly and accurately at all
times. Faulty controls can cause personal injury.
In cold weather situations let your hydraulic system
idle for approximately 15 minutes to allow the system
to warm up to operating temperature.
WARNING
WARNING
SAFETY INSTRUCTIONS
NOTICE
This machine is equipped with a very efficient, simple hydraulic system. Each component is capable of
withstanding a specified pressure and still operate for a very long time.
• If a problem is encountered, it will more than likely
be located in the relief valve or something as simple
as belts or clutch slipping, check these first.
•
Only use the optional adjustable flow control when
chipping large diameter trees. Do not leave the speed
adjustment partially open for long periods of time. This
will cause excessive heat to the hydraulic system!
Excessive heat will cause low feedwheel power and
premature failure of all hydraulic components. Always
operate system at full oil flow unless chipping large
diameter trees.
•
Do not close the optional hydraulic shut‑off valve
for more than 3 to 4 seconds. Hydraulic shut‑off
valve handle must be completely turned on (in line
with hose) at all times unless checking hydraulic
pressure. Pressure gauge should be safely stored and
installed only when checking pressure. Follow above
instructions or this will cause unwarranted damage to
the hydraulic components.
• Never close the ball valves on the hydraulic
tank suction ports (if equipped) while the machine
is running, this will ruin the hydraulic pump and
components.
• Avoid hydraulic pump cavitation. Low oil levels
or cold start-ups will cause the hydraulic pump to
cavitate. Cavitation will ruin the pump and possibly
the entire hydraulic system. Cavitation only has to
happen once. This will start the pump on its way to
ruin. Allow hydraulic system to turn slowly for several
minutes in cold weather in order for hydraulic system
to warm up. Cavitation is not covered under warranty.
• Keep hydraulic oil clean. Dirty oil will cause
excessive wear and loss of hydraulic power.
•
Replace the hydraulic oil filter(s) after first 10
hours and with each 400 hours of operation or 3
months.
• Replace hydraulic oil & suction screen(s) at least
once yearly. This is also a very good time to flush and
clean the tank. Replace hydraulic oil immediately if
it is contaminated or looks “milky”. See page 43
for hydraulic oil requirements.
• If the machine’s hydraulic system is kept clean
and the hydraulic pressures are not increased
beyond the specified pressure, the maximum use
and life should be received from the hydraulic
system.
If the simple rules mentioned below are followed, the hydraulic components will last for years: