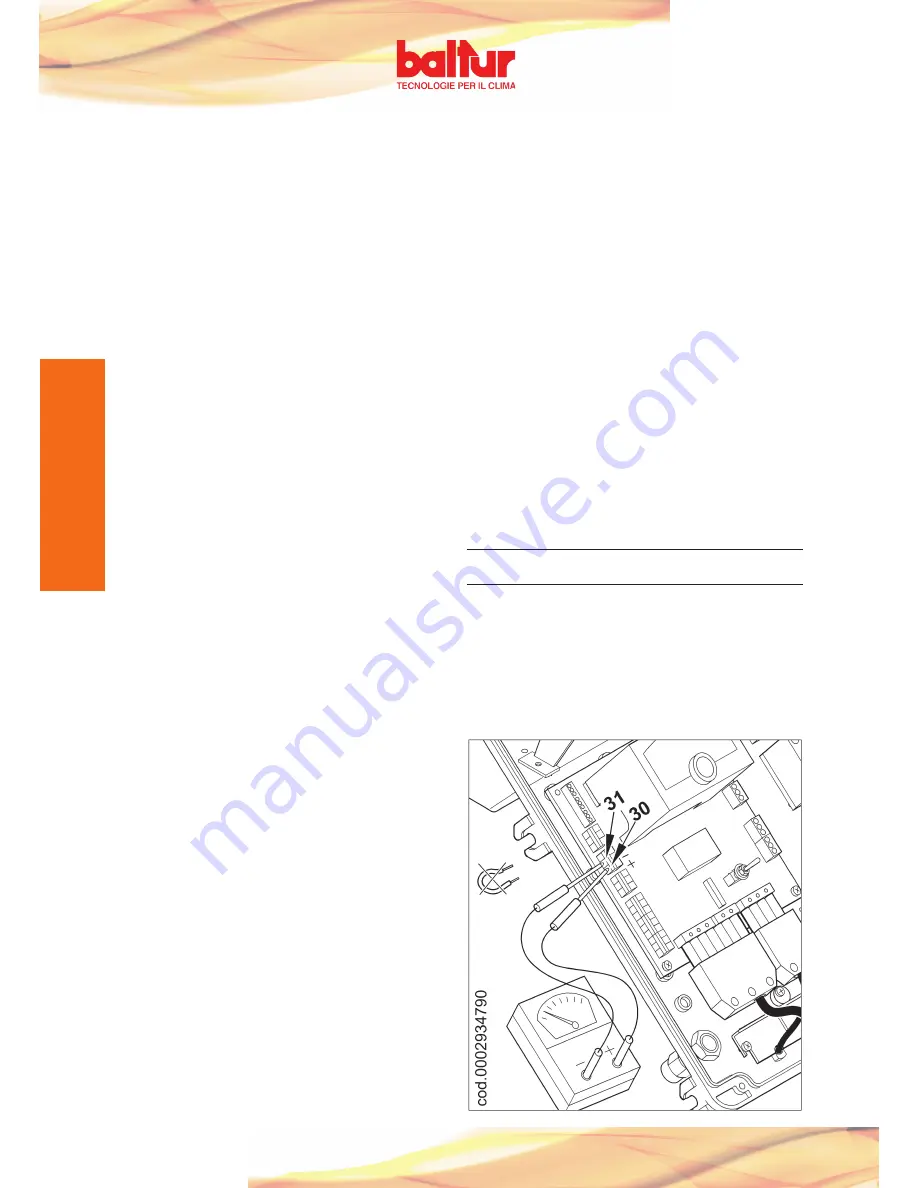
30 / 75
0006081327_200807
E
N
G
L
I
S
H
IONISATION CURRENT MEASUREMENT
To measure the ionisation current, remove the jumper between
terminals 30-31 on the printed circuit with the burner off (see
diagram). Connect a microampmeter to the terminals (with a suitable
scale to have the burner restart). Once the flame has appeared it
will be possible to measure the ionisation current, the minimum
value of which to ensure the working of the equipment is shown in
the specific wiring diagram. After making the measurement, reset
the jumper that has been disconnected.
13) To change the maximum gas flow, use the air flow regulator
so that the gas is suitably and automatically adjusts itself to
the supply of air. The cam regulating the maximum opening
of the damper must be reset (see instructions on adjustment
0002933650). The air damper opening angle must be reduced
to reduce the gas flow and vice versa; to change the gas-air mix
see the instructions for the pneumatic gas valves installed.
14) Subsequently check the combustion with the special
instruments. For a correct air-gas mix you must measure the
carbon dioxide (CO2) to methane value and check that it is at
least 8% or O2=6% with minimum burner supply, up to an ideal
value of 10% or O2= 3% at maximum supply. It is essential to
check, with a suitable instrument, that the percentage of carbon
monoxide (CO) present in the fumes does not exceed the limit
set by regulations at the time of installation.”
15) after adjusting running at maximum thermal capacity you
have to set the air adjustment servo motor at the minimum
supply position, turning the modulation switch to MIN. If, with
burner running at minimum power, it is necessary to change
the combustion conditions, follow the pneumatic gas valves
adjustment devices’ instructions. We advise you carry out
a check on combustion with the special instruments and, if
necessary, change the setting previously carried out, even on
some intermediate points on the course set for the air damper.
16) now check the proper working of the automatic modulation
mode.
17) the air pressure switch
is a safety (lock-out) system for if
the air pressure is not that expected. The pressure switch
must therefore be set to be triggered to close the contact (it
should be closed when working) when the air pressure in the
burner reaches a sufficient level. Please note that if the contact
which should be closed when working does not in fact close
(air pressure insufficient) the system goes through its work
cycle but does not switch on the ignition transformer and the
gas valves will not open, with the result that the burner stops in
lock-out. To check the right working of the air pressure switch
you must, with burner at minimum supply, increase regulation
to check the triggering that leads to immediate “lock-out” of the
burner. To release the locked burner, press the release button
and reset the pressure switch to a value sufficient to detect
the existing air pressure during the preventilation stage. The
pressure switch’s connection circuit has automatic control so
the contact must be closed at rest (fan stopped and so no air
pressure in burner). This condition is produced if the control
box is not switched on and the burner stays stopped.
18) The gas pressure control switches (minimum and maximum),
if installed, prevent the working of the burner when the gas
pressure is not within the preset values. From the specific
function of the pressure switches it is clear that the minimum
pressure control switch must use the contact that is closed
when the pressure switch detects a pressure greater than that
set, while the maximum pressure switch must use the contact
which is closed when the pressure switch detects a pressure
that is lower than that set. The adjustment of the minimum
and maximum gas pressure gas switches must therefore take
place on inspection and testing of the burner according to the
pressure from time to time found. The pressure switches are
electrically connected in series, thus the triggering (i.e. with
circuit opening) any one of the gas pressure switches, which
prevents the switching on the control box and hence of the
burner. When the burner is running (flame on), the triggering
of thegas pressure
switches (circuit opening) causes the
immediate stoppage of the burner. When the burner is being
tested it is essential to check the proper working of the
pressure switches. Using the respective adjustment devices,
the triggering of the pressure switch (circuit opening) can be
checked, ensuring it causes the arrest of the burner.
19) Check the flame sensor (ionisation sensor) is triggered,
disconnecting the bridge between terminals 30 and 31 on the
printed circuit and switching on the burner. The control box
must completely carry out its working cycle and, three seconds
after the ignition flame is formed, stop itself in “lock-out”. This
check only needs to be carried out with the burner already
on. Disconnecting the 30 and 31 jumper, the control box must
immediately go into its “lock-out” action.
20) Check the proper working of the thermostats or pressure
switches for the boiler (when triggered they must stop the
burner.
N.B. Check that the switch on occurs normally since if the adjuster
is shifted forward, it may happen that the speed of the delivery air
is so high that ignition is difficult. If this happens, the adjust must
be shifted back by degrees until it is in a position in which ignition
occurs normally, and this new position can be regarded as the final
position. We remind you that is preferable, in the case of the small
flame, to limit the quantity of air to the least possible needed for
safe ignition, even in the most difficult circumstances.
Summary of Contents for TBG 110LX PN
Page 2: ......
Page 20: ......
Page 38: ......
Page 56: ...54 75 0006081327_200807 F R A Ç A I S ...
Page 74: ...72 75 0006081327_200807 ...
Page 75: ...73 75 0006081327_200807 ...
Page 76: ...74 75 0006081327_200807 ...