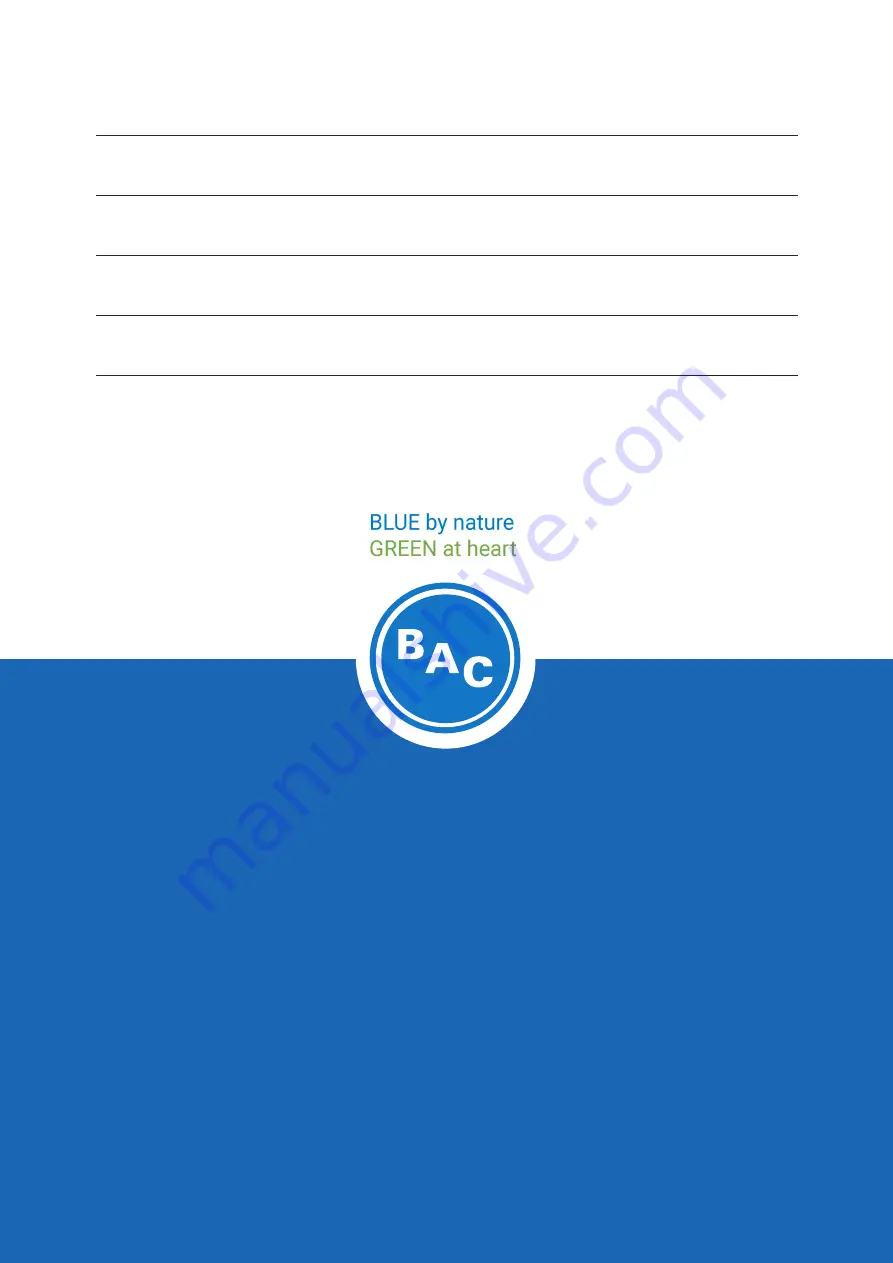
COOLING TOWERS
CLOSED CIRCUIT COOLING TOWERS
ICE THERMAL STORAGE
EVAPORATIVE CONDENSERS
HYBRID PRODUCTS
PARTS, EQUIPMENTS & SERVICES
www.BaltimoreAircoil.eu
Please refer to our website for local contact details.
Industriepark - Zone A, B-2220 Heist-op-den-Berg, Belgium
©
Baltimore Aircoil International nv