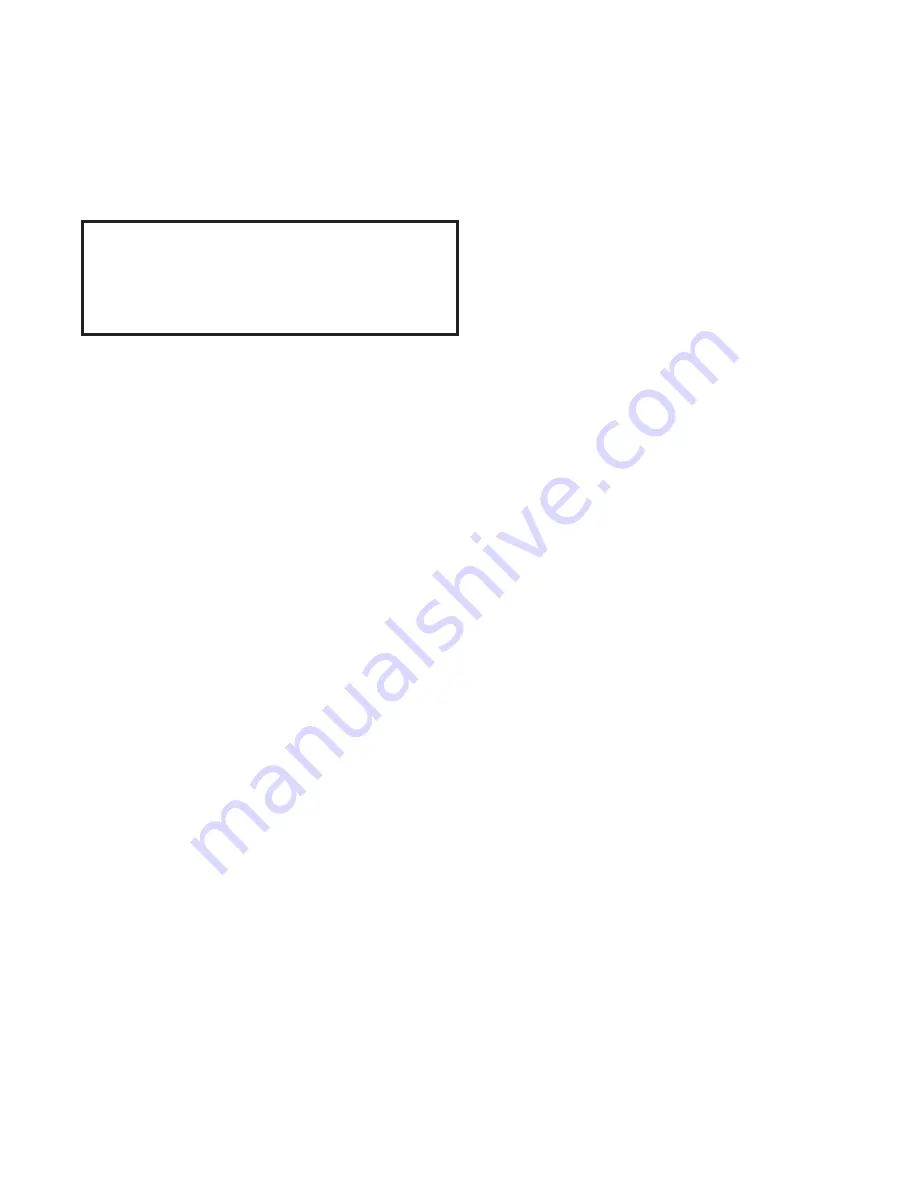
Page 5
INSTALLATION
Check the tightness of the pump's hardware prior to
installation and operation of a new pump.
Pump hard-
ware is prone to loosening due to vibration in transportation,
expansion and contraction, or the relaxing of materials after
they are torqued.
It is important that the pump is not
under pressure when hardware is being tightened.
This pump comes with a footed base for easy mounting
in permanent installations. The pump should be mount-
ed in a vertical position. In permanent installations, the
pump should be attached to plant piping using a flexible
coupling on both the intake and discharge connections
to reduce vibration to the pump and piping. To further
reduce vibration, a surge suppressor next to the pump
may be used.
Suction pipe size should be at least 1/2 inch in diameter
or even larger if highly viscous fluid is to be pumped.
If suction hose is used, it must be of a non-collapsible
reinforced type. Discharge piping should be at least
1/2 inch in diameter. It is critical, especially on the suction
side of the pump, that all fittings and connections are air-
tight or pumping efficiency will be reduced and priming
will be difficult.
The air supply line should be at least 3/8 inch in diame-
ter. Make certain the supply line and compressor are
capable of supplying the required pressure and volume
of air needed to operate the pump at the desired flow
rate. The quality of the compressed air source should be
considered. Air that is contaminated with moisture and
dirt may result in erratic pump performance and
increased maintenance cost as well as frequent process
“down time” when the pump fails to operate properly.
PUMP OPERATION
The pump is powered by compressed air. Compressed
air is directed to the pump air chamber by the main air
valve. The compressed air is separated from the fluid by
a membrane called a diaphragm. The diaphragm in turn
applies pressure on the fluid and forces it out of the
pump discharge. While this is occurring, the opposite air
chamber is depressurized and exhausted to atmosphere
and fluid is drawn into the pump suction. The cycle again
repeats, thus creating a constant reciprocating action,
which maintains flow through the pump. The flow is
always in through the bottom suction connection and out
through the top discharge connection. Since the air pres-
sure acts directly on the diaphragms, the pressure
applied to the fluid roughly approximates the air supply
pressure supplied to the main valve.
TROUBLESHOOTING
The pump will not run, or runs slowly:
1. Examine the air inlet for debris.
2. Check for a sticking air valve. Remove the air valve from
the pump and check to see if air valve spool can move
freely. If dirt or debris is present wipe it away with a
cloth. Check to see if the valve spool u-cups or the air
valve housing is worn. If worn, replace with new com-
ponents. Clean all ports and airways and replace worn
out gaskets and o-rings.
3. Check pilot shaft and main shaft for scoring and
scratches; replace if needed. Replace the pilot shaft
and main shaft o-rings if they are worn, flat or torn.
The pump runs, but little or no material flows:
1. Check for pump cavitation, slow the pump speed
down to match the thickness of the material being
pumped.
2. Look for sticking ball checks. If the material being
pumped is not compatible with the ball material, the
elastomer may swell. Replace the balls and seats
with a compatible elastomer type.
3. Make sure all the suction line fittings and connec-
tions are tight.
Air bubbles in pump discharge:
1. Look for a ruptured diaphragm.
2. Check for suction leaks in pump manifolds and piping.
Material comes out of the pump air exhaust:
1. Inspect the diaphragm for rupture.
2. Check the tightness of the diaphragm plates to the
pump shaft.
1120-012 1/2" Aluminum Pump Torque Settings
Water Chamber Bolts ............... 100 in-lbs (11.3 N-m)
Diaphragm Plates ......................... 50 in-lbs (5.6 N-m)
Air Valve Screws ........................... 25 in-lbs (2.8 N-m)
Manifold Bolts........................... 230 in-lbs (26.0 N-m)