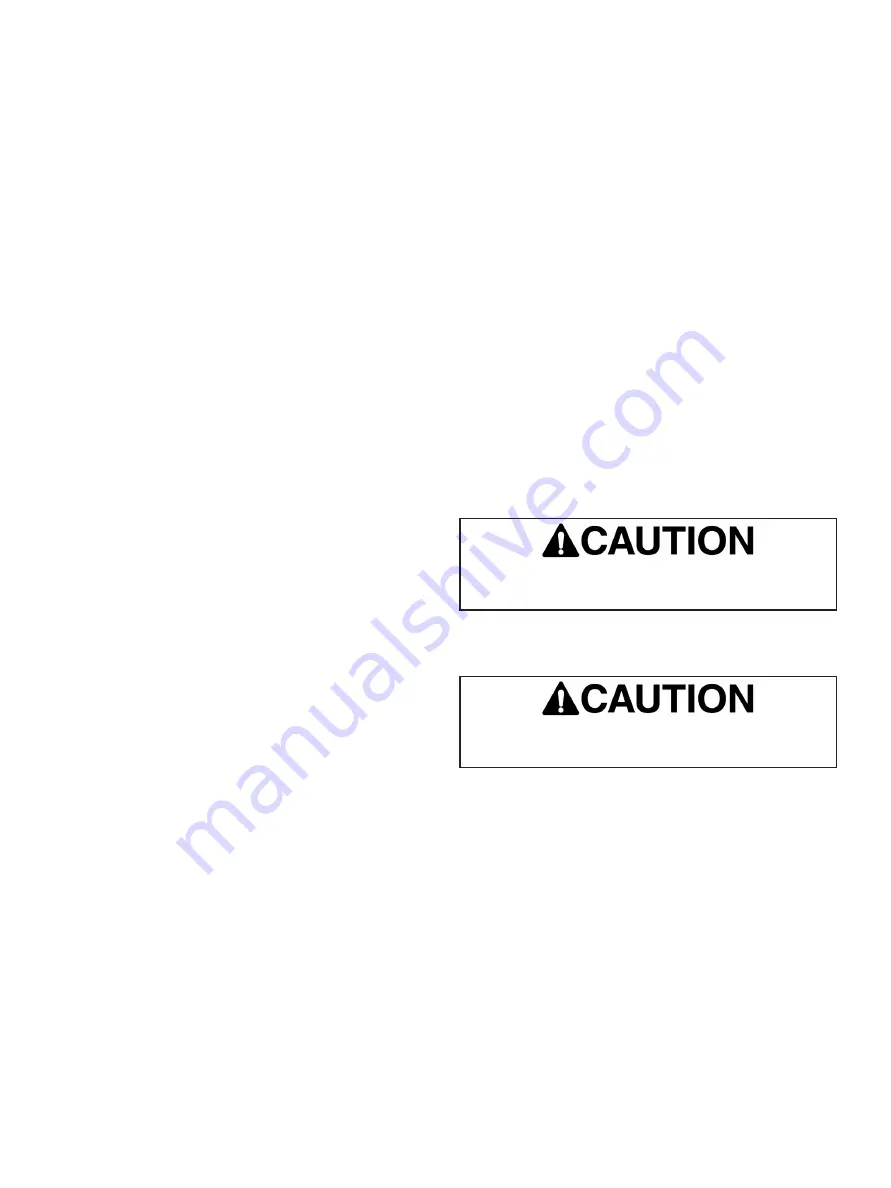
6 | Baker Hughes
Copyright 2020 Baker Hughes Company. All rights reserved.
Maintenance
Lapping Seats
If, after long service, valve leakage becomes excessive, a hand
operation called lapping is necessary. In order to facilitate this
operation, the plug and seat ring seating surfaces should be free
of large scratches or dents and the contact surfaces of the seats
should be as narrow as possible. This may require dressing both
parts in a lathe. The seating surfaces make an angle of 60° with
the axis of the plug.
For the lapping operation, a good grade of fine grinding
compound is required. The compound is applied at several spots
equally spaced around the periphery of the ring. Assemble the
entire valve body including the packing for the lapping operation
(excluding the bottom flange of the diverting valve). The bonnet
(and bottom flange of the combining valve) fastened temporarily
to the body, less gasket, serves as a guide during the lapping
operation. To facilitate lapping, screw a drilled and tapped rod
with a T-handle onto the top of the valve stem and secure with a
locknut. As an alternative, drill a hole through a small flat piece
of steel and fasten to the plug stem with two locknuts. Before
lapping, plug and stem must be “true” (see pinning operation).
Lapping is accomplished by rotating the plug in short oscillating
strokes. After 8 or 10 strokes, the plug should be lifted and
turned 90% before repeating the operation. This intermittent
lifting is important to keep the plug and seat ring concentric
during lapping.
It is advisable to mix a small quantity of lubricant such as
graphite with the grinding compound. This will slow the cutting
rate and avoid tearing the seating surface.
The amount of lapping required depends on the materials of
construction, condition of the seating surfaces and accuracy of
machining. If a short period of lapping does not visibly improve
seating, there is usually no advantage in continuing as too much
lapping may result in rough seats or small ridges on the plug
or seat ring. The only remedy is replacement of one of both
parts. When lapping a new plug and rings, begin with coarse
compound and finish with fine. Old (used) parts should only be
lapped with a fine grade of compound.
Packing Box
Packing box maintenance is one of the principal chores of
routine servicing. For smooth valve operation, the packing
should be compressed just enough to affect a seal and no
more. Tightness of the packing box is maintained by the packing
compression alone or in combination with a lubricant. Little by
little it is necessary to take up on the packing until all available
compression is used up.
To add packing, it is necessary only to back off the packing
follower and flange and insert one or two rings of split ring
packing.
Note: In an emergency, string packing may be inserted
without removing old packing, after first taking the valve out
of service. If the packing is solid ring, it will be necessary
to disassemble the valve and remove the old packing. To
repack the packing box, refer to Reassembly – 80385 (Step
3).
Lubrication
For some applications, packing boxes are designed for use with
a lubricator. The lubricator (66) is provided with a ball check
valve to prevent back flow of the process fluid. On steel valves,
an isolating valve (67) is added for positive protection against
back flow. The lubricator should be kept filled with the specified
lubricant and turned in firmly but not tightly. One or two turns of
the lubricator once every two weeks should suffice to provide
the desired seal. Lubricants are stocked in our Norwood plant
and may be ordered through your local Masoneilan International
Representative or District Office.
Plug Stem Pinning
Valve plug and stem assemblies are normally furnished as a
complete assembly in which case the installation involves no
problems. It is necessary only to lap the seats and assemble
the valve.
If necessary to assemble plug and plug stem, it is better to use
a new stem as the original pin hole in an old stem prevents
satisfactory results an might seriously impair the strength of
the assembly. If an old stem must be used, the plug end of
the stem should be cut off just above the old pin hold and the
stem rethreaded the original amount. This will shorten the stem
but there is usually enough adjustment in the actuator stem to
compensate. If, however, the thread engagement in the actuator
stem is less than the diameter of the plug stem, the plug stem
should be disgarded.
While pinning is being performed, the seating surface
and plug guide of the plug must not be damaged!
The old pin may usually be removed by driving it out with a punch.
If necessary to drill it out, a drill somewhat smaller than the pin
should be used and then the remainder of the pin driven out.
Do not mar the guide section of the plug by gripping
in the jaws of a vise.
For drilling, the plug should be placed with the guide section
resting on a vee block. The stem must be screwed into the plug
solidly before starting to drill. This can be checked by measuring
the depth of the pilot recess in the plug (X in figure on page 8)
and making a reference mark on the stem the same distance
from the thread. When properly assembled, the reference mark
should be flush with the end of the guide section. The stem can
then be redrilled through the old hole in the guide section, using
first a pilot drill of suitable size and then a reamer drill to bring the
hole to required size for the pin. After all burrs and sharp corners
are removed from the edge of the hole, a small amount of grease
should be applied before inserting the pin. The hole should be of
such diameter that the pilot end of the pin can be pushed in by
hand about 1/8” to 3/16”. The easiest method of driving the pin is
to press it in the jaws of a vise. Be sure the pin is recessed about
1/16” below the plug guide surface. After plug has been pinned, it
should be placed in a lathe to see if it is running “true”. If it is not,
tap the plug with a mallet to straighten. Stem should be placed in
“chuck” and plug should be tapped.