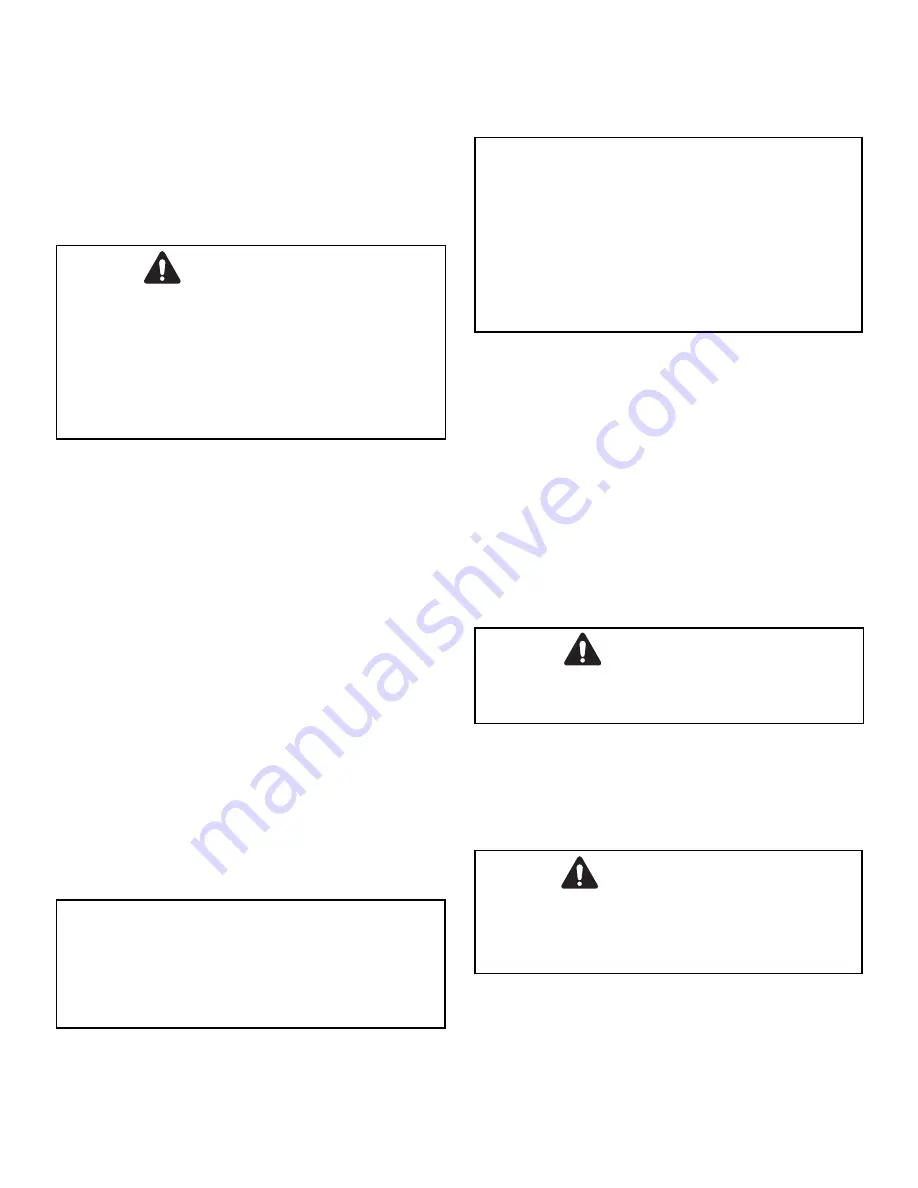
Masoneilan 49000 Series Energy Management Control Valves | 3
Copyright 2020 Baker Hughes Company. All rights reserved.
Installation
Piping Cleanliness
Before installing the valve in the line, clean piping and valve of all
foreign material such as welding chips, scale, oil, grease or dirt.
Gasket mating surfaces must be thoroughly cleaned to ensure
leak-free joints. Sacrificial start-up fixtures can be purchased from
Baker Hughes to protect the operational trim during the installa-
tion and line flushing phases.
CAUTION
CAUTION
WARNING
DANGER
If major system or piping modifications (or repairs) are
performed, thorough flushing and blowdown of the
system will be required prior to reinstalling the trim.
Sacrificial flushing trim should be installed in the valve
to protect the integrity of the flow passages. Failure to
follow this warning will violate the valve warranty agree-
ment and could result in control instability, excessive
noise levels, and valve leakage.
Isolation Bypass Valve
To allow for in-line inspection, maintenance and removal of the
valve without service interruption, provide a manually operated
shutoff valve on each side of the control valve and a manually
operated throttling valve in the bypass line.
Heat Insulation
In case of a heat-insulated installation, do not insulate the valve
bonnet and take protective measures relative to personal safety.
Hydrostatic Testing and Line Cleaning
During this operation, the control valve must not be used as an
isolating valve. This means that the valve must always be opened
before carrying out pressure tests in the process line, cleaning
of pipes, etc. otherwise equipment damage or failure of the seal
rings could result. If the valve is to remain installed during line
cleaning, flushing trim MUST be installed to prevent damage to
trim components.
Flow Direction
The valve must be installed so that the process fluid will flow
through the valve in the direction indicated by the flow arrow
located on the body.
Welded Connections
CAUTION
CAUTION
WARNING
DANGER
Carefully review the information in this section prior to
welding any valves inline. Refer any additional ques-
tions to the local Baker Hughes Sales Office or Service
Center.
Pre-Weld Preparation
Carefully follow the installation steps defined in the sections noted
above prior to performing weld procedures.
Welding Process
Perform welding process in accordance with the standard
requirements for the materials and weld construction of the specific
valve. Apply post weld heat treatment if required.
CAUTION
CAUTION
WARNING
DANGER
Internal valve components should be removed prior
to performing welding or pre/post weld heat treatment
weld heat treatment in order to prevent damaging any
soft goods (such as PTFE seals). If unable to remove
the elastomeric components, then other methods must
be employed to prevent the local temperature around
the seals from exceeding the maximum material limits
(typically 450°F / 232°C for PTFE based materials).
Post Weld Cleaning & Assembly
Inspect the body, bonnet, and trim components for cleanliness and
surface condition. Remove any foreign materials, such as weld
chips, slag or scale. Make sure there are no nicks, scratches, burrs
or sharp corners on sealing and sliding surfaces. Clean all gasket
interface surfaces and reassemble using new gaskets to ensure
sealing integrity.
Actuator Assembly
Assemble the pneumatic actuator onto the control valve using the
appropriate instructions for the specific actuator model and type.
Connect air pressure lines to the actuator ports to meet intended
operating mode (i.e., air-to-extend, air-to-retract, or double-acting).
Disassembly
CAUTION
CAUTION
WARNING
DANGER
Prior to performing any maintenance on the valve, iso-
late the valve and vent the process pressure.
Valve Actuation
Access to the internal components of the valve should be
accomplished with the actuator removed. Follow the detailed
instructions below and refer to the appropriate actuator
instruction manuals.
CAUTION
CAUTION
WARNING
DANGER
Actuator may be pre-loaded with tension from air pres-
sure or springs. Prior to disconnecting instrumentation
read all instructions for the specific actuator.
Disconnect Instrumentation
Disconnect all mechanical connections between the positioner and
the other instruments. Disassemble the valve stem and actuator
stem coupling as described in the following sections.