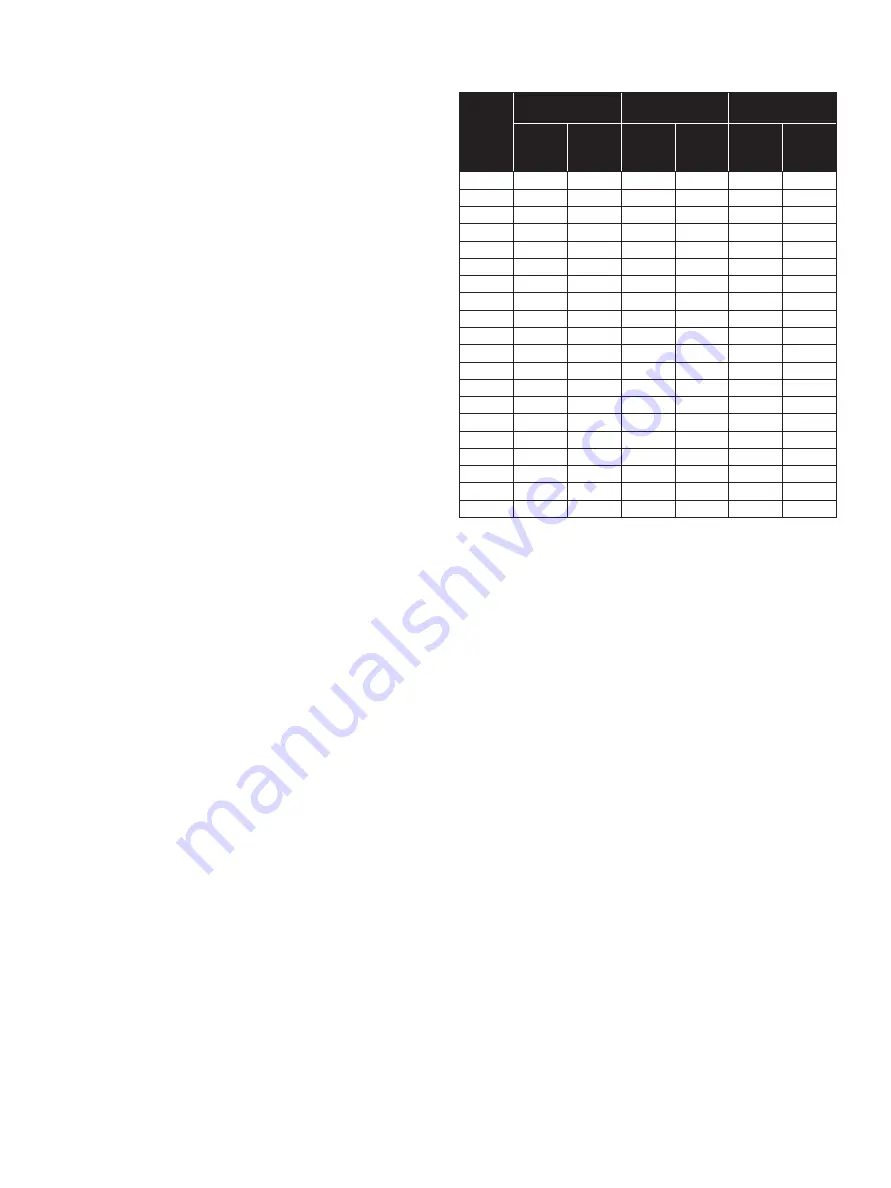
3 | Baker Hughes
Copyright 2020 Baker Hughes Company. All rights reserved.
2. Maintenance
1. Reasonable precautions should be taken before beginning
work on the valve. Protective clothing, as required by the
specific line fluid, should be worn.
2. Before removing handle or the actuator from the valve, or
before removing seat retainer from a valve in dead end
service, close the valve and depressurize the line. The
eccentric design of the 39004 Series may allow line pressure
to open the valve if the handle / actuator is not in place while
the valve is under pressure.
DO NOT PRESSURIZE THE LINE WITHOUT A HANDLE
OR ACTUATOR ON THE VALVE.
3. The 39004 Series valve must be in the closed position to be
removed from the line.
4. Begin all work on a valve that has been removed from the
line by cleaning the valve, removing any grit or scale. When
handling the valve, care should be taken not to scratch the
disc edge or seats.
5. Replacement seats, seals and other parts are available from
authorized distributors. Contact your distributor or sales
representative for details of price and delivery.
3. Stem Seal Replacement
Refer to drawing on page 5 for parts identification.
1. If required, remove handle assembly. Remove socket head
cap screws (21) and lock washers (22). Remove mounting
bracket (20). For actuated valves, unbolt mounting bracket
from body and lift actuator assembly off stem. Note assembly
positions before removal.
2. Remove gland retainer nuts (14) and lock washers (13).
Remove gland retainer (11) anti-blowout retaining ring or
split ring (10) (depending on size), and gland ring (7).
3. Hook out stem seals (8), taking care not to scratch stem or
stuffing box bore. Do not remove thrust washer (9), unless
further valve disassembly is required.
4. Examine stuffing box bore and stem, clean as necessary
to remove any corrosion or foreign matter before installing
new seals.
5. Install new seals in stuffing box one at a time, TFE (white)
seals first, with the carbon fiber ring at the top. Stagger seal
ring joints 180° apart when installing. Tamp each ring to
bottom before installing next ring.
Note: On the larger valves it will be necessary to
compress each seal before adding the next.
6. Slide gland ring (7) over stem on top of seals (8). Install anti-
blowout retaining ring or split ring (10) (depending on valve
size). Slide gland retainer (11) over stem and onto gland
studs (12). Place lockwashers (13) and hex nuts (14) on
studs (12) and tighten finger tight. Tighten gland nuts (14)
evenly and alternately to the proper torque value given in
Table 2.
7. Remount actuator, or mounting bracket (20) with lock
washers (22) and cap screws (21) and handle (27). Tighten
handle set screw (28) to secure the handle to the valve
stem.
8. Operate valve open and closed several times, to check for
binding and to set the stem seals. Loosen gland nuts (14)
and retighten to torque value given in Table 2.
Table 1 - Total Number of Stem Seals
CF = Carbon Fiber
Valve
Size
Class 150
Class 300
Class 600
Number
of Stem
Seals
Material
CF / TFE
Number
of Stem
Seals
Material
CF / TFE
Number
of Stem
Seals
Material
CF / TFE
3
4
1 / 3
4
1 / 3
12
2 / 10
4
4
1 / 3
4
1 / 3
12
2 / 10
6
4
1 / 3
4
1 / 3
16
2 / 14
8
5
1 / 4
5
1 / 4
16
2 / 14
10
5
1 / 4
5
1 / 4
18
0 / 18
12
5
1 / 4
5
1 / 4
18
0 / 18
14
6
0 / 6
6
0 / 6
18
0 / 18
16
6
0 / 6
9
0 / 9
16
0 / 16
18
16
0 / 16
20
16
0 / 16
24
10
0 / 10
8
0 / 8
30
8
0 / 8
9
0 / 9
32
8
0 / 8
36
8
0 / 8
9
0 / 9
40
9
0 / 9
9
0 / 9
42
9
0 / 9
9
0 / 9
44
9
0 / 9
48
9
0 / 9
9
0 / 9
54
9
0 / 9
60
9
0 / 9
4. Seat Replacement
1. With the disc in the closed position, remove the valve from
the line.
2. Lay the valve down with the disc in the closed position and
the seat retainer side facing up.
3. Remove the socket head cap screws (17), the seat retainer
(16), and seat (15).
4. Carefully clean the seat area in the body and seat retainer.
Remove foreign matter, dirt, etc. Check disc seating area for
nicks or scratches.
5. Place the new seat (15) on disc (2), carefully centering it in
the recess in the body.
6. Align the holes in the seat retainer (16) with matching holes
in body and carefully place in position on top of seat (15).
Be careful not to shift retainer to align holes so that seat is
not shifted from correct position. Lightly grease cap screw
(17) threads and tighten down evenly, alternating from top
to bottom and side-to-side. Tighten to the torque value in
Table 2.
7. Operate valve several times and examine seat for any
damage before reinstalling the valve in the line.