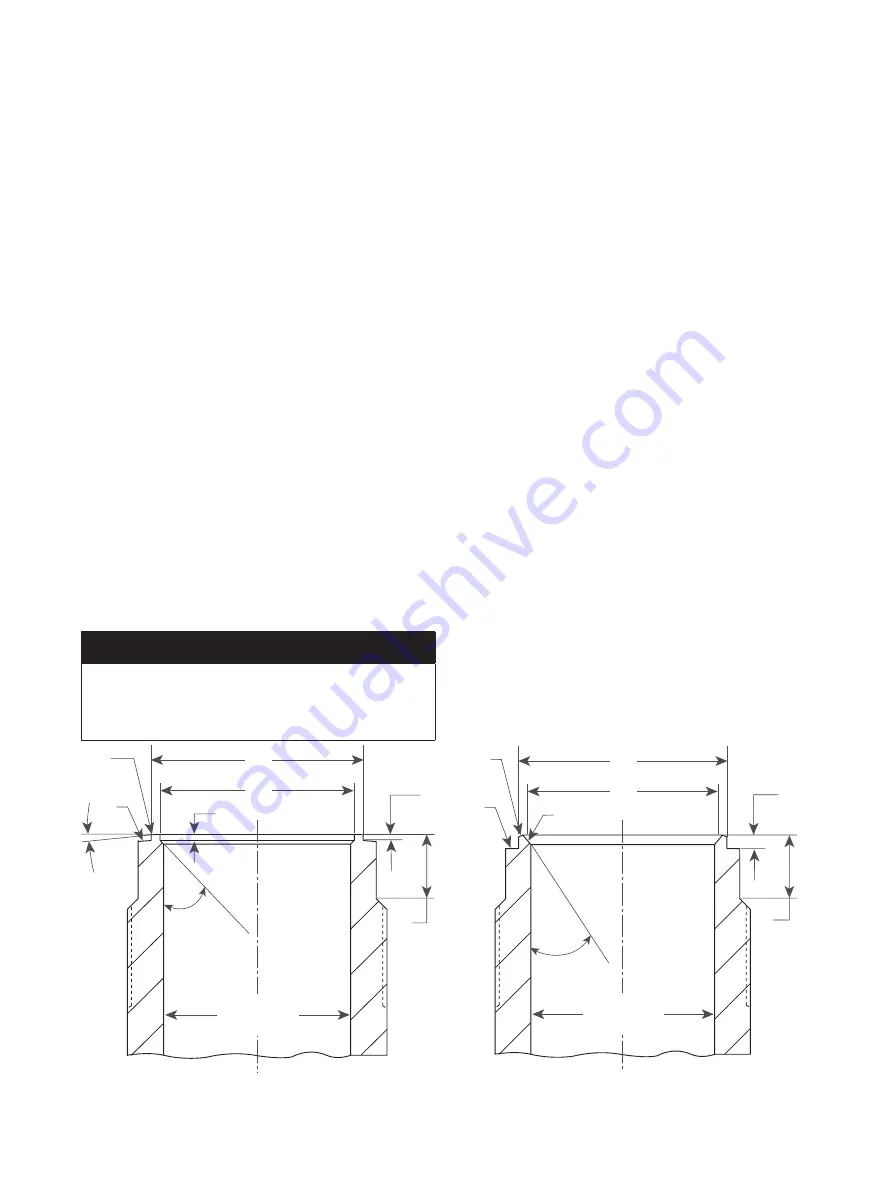
XIV. Maintenance Instructions
A. General Maintenance Information
After the valve has been disassembled, a close
inspection should be made of the seating surfaces.
In a majority of cases, a simple lapping of seats is
all that is necessary to put the valve in first class
working order. If an inspection of the parts shows
the valve seating surfaces to be badly damaged,
machining will be required before lapping. O-Ring
seat seal valve nozzles can only be reconditioned
by machining, not lapping. (For specific information
concerning the machining of nozzle and disc seating
surfaces, see The Re-Machining Nozzle Seats and
Bores and Re-Machining the Disc Seat sections.)
The seating surfaces of the metal seated
Consolidated Safety Relief Valve are flat. The nozzle
seat is relieved by a 5° angle on the outside of the
flat seat. The disc seat is wider than the nozzle seat;
thus, the control of seat width is the nozzle seat (see
Figure 34).
Reconditioning of the seating surfaces of the nozzle
and disc is accomplished by lapping with a cast iron
lap, and lapping compound.
Anytime the V or W orifice valve is disassembled,
be sure to inspect the Guide Rings for wear. If worn,
replace before reassembly.
ATTENTION!
In order to establish leak free valve seats,
the nozzle seating surface and the disc
seating surface must be lapped flat..
B. O-Ring Seat
The nozzle must not have any defects to prohibit the
O-Ring from sealing properly, especially the OD of
the seat where the surface must maintain a minimum
of 32 RMS finish. See Figure 34 and Table 2 for
reworking O-Ring Nozzle.
The O-Ring Retainer must also maintain a flat
surface for it to sit on the Nozzle. Only polishing of
surface can be done since material removal from this
surface will cause the Nozzle to over engage O-Ring.
Polishing paper or some other light abrasive can
only be used since the part cannot function properly
if its overall dimensions are changed significantly.
If significant corrosion or damage has occurred on
O-Ring retainer, discard and replace.
K
L
D
J
45°
Nozzle
Bore
B
A
M
F
H
D
N
E
P
5°
Nozzle
Bore
L
G
Figure 34a: Metal Seat Nozzle
Figure 34b: Soft Seat Nozzle
Figure 34: Main Valve Nozzle Critical Dimensions
40 |
Baker Hughes
© 2021 Baker Hughes Company. All rights reserved.