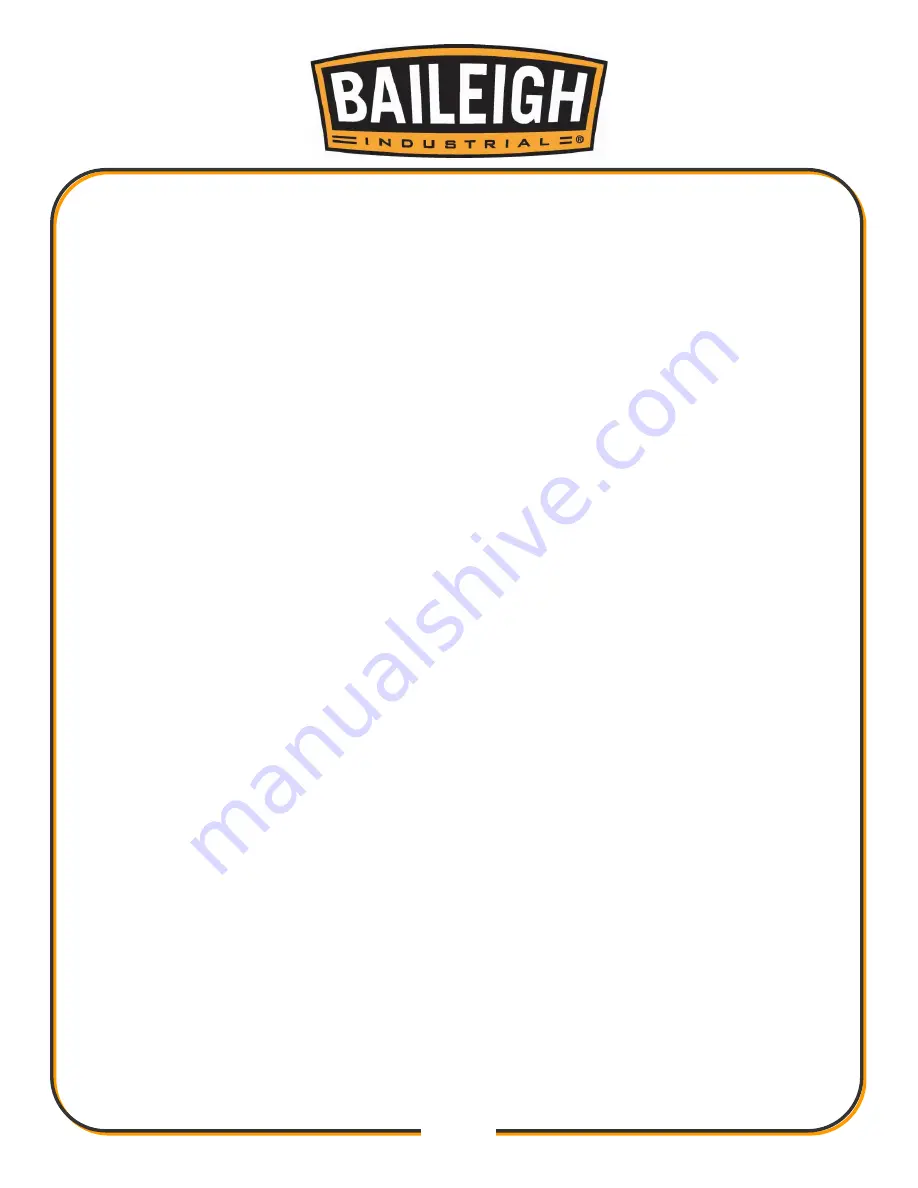
11
11
•
Remove scrap and waste materials regularly, and make sure the work area is free from
obstructing objects.
•
If long lengths of material are to be fed into the machine, make sure that they will not extend
into any aisles.
•
LEVELING:
The machine should be sited on a level, concrete floor. Provisions for securing it
should be in position prior to placing the machine. The accuracy of any machine depends on
the precise placement of it to the mounting surface.
•
FLOOR:
This machine distributes a large amount of weight over a small area. Make certain
that the floor is capable of supporting the weight of the machine, work stock, and the
operator. The floor should also be a level surface. If the unit wobbles or rocks once in place,
be sure to eliminate by using shims.
•
WORKING CLEARANCES:
Take into consideration the size of the material to be
processed. Make sure that you allow enough space for you to operate the machine freely.
•
POWER SUPPLY PLACEMENT:
The power supply should be located close enough to the
machine so that the power cord is not in an area where it would cause a tripping hazard. Be
sure to observe all electrical codes if installing new circuits and/or outlets.
Summary of Contents for BS-128M
Page 3: ...SAW VISE AND BASE PARTS DIAGRAM 37 Parts List 38 ELECTRICAL SCHEMATIC 43 TROUBLESHOOTING 44...
Page 15: ...12 12 GETTING TO KNOW YOUR MACHINE S R Q P O N M L K J I H G F E D C B A...
Page 29: ...26 26...
Page 39: ...36 36 SAW BOW PARTS DIAGRAM...
Page 40: ...37 37 SAW VISE AND BASE PARTS DIAGRAM...
Page 46: ...43 43 ELECTRICAL SCHEMATIC...
Page 50: ...47 47 NOTES...
Page 51: ...48 48 NOTES...