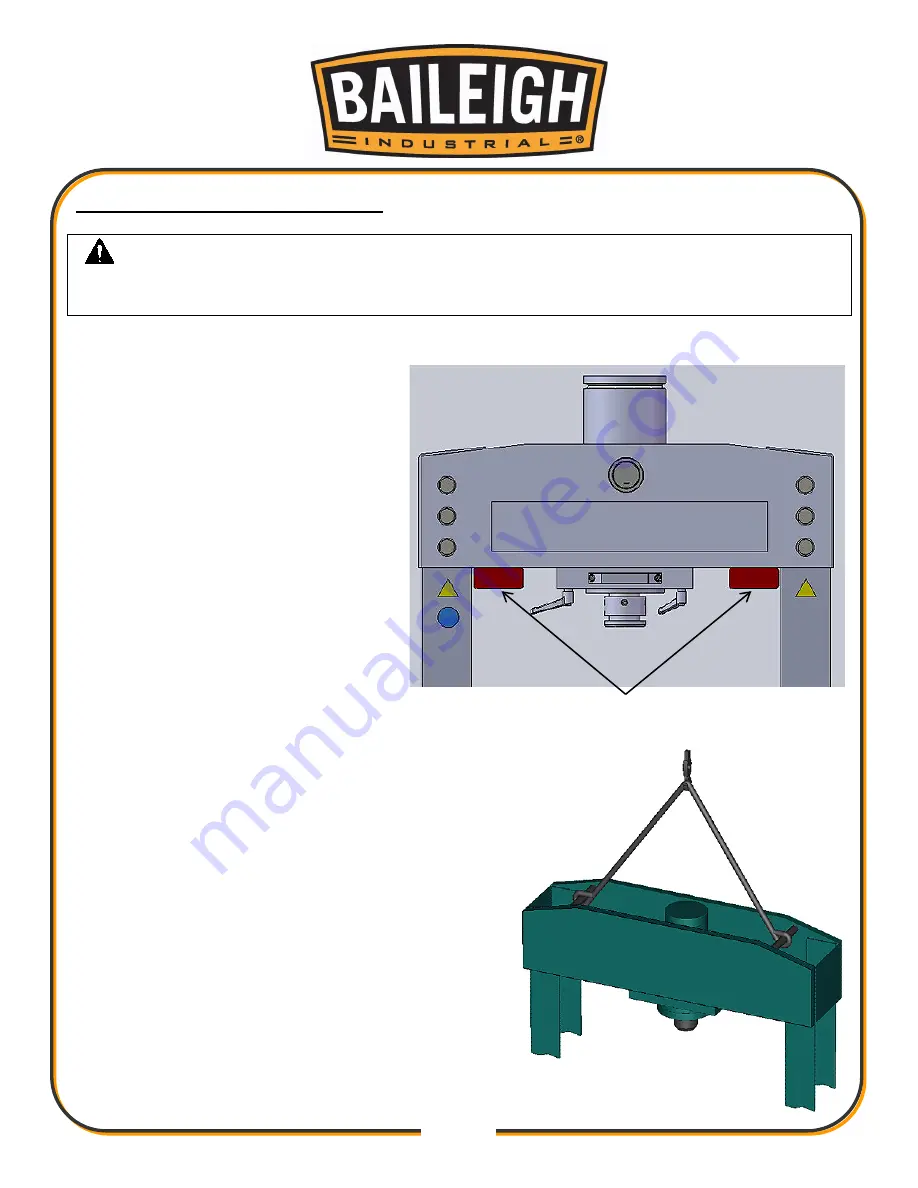
11
11
TRANSPORTING AND LIFTING
IMPORTANT:
Lifting and carrying operations should be carried out by skilled workers,
such as a truck operator, crane operator, etc. If a crane is used to lift the machine, attach the
lifting chain carefully, making sure the machine is well balanced.
Follow these guidelines when lifting with truck or trolley:
•
The lift truck must be able to lift at
least 1.5 – 2 times the machines
gross weight.
•
Make sure the machine is balanced.
While transporting, avoid rough or
jerky motion, and maintain a safe
clearance zone around the transport
area.
•
Use a fork lift with sufficient lifting
capacity and forks that are long
enough to reach the complete width
of the machine.
•
Remove the securing bolts that
attach the machine to the pallet.
•
Approaching the machine from the
side, lift the machine on the frame
taking care that there are no cables or pipes in the
area of the forks.
•
Move the machine to the required position and
lower gently to the floor.
•
Level the machine so that all the supporting feet
are taking the weight of the machine and no
rocking is taking place.
Follow these guidelines when lifting crane or
hoist:
•
Always lift and carry the machine with the lifting
holes provided at the top of the machine.
•
Use lift equipment such as straps, chains, capable
of lifting 1.5 to 2 times the weight of the machine.
•
Take proper precautions for handling and lifting.
Lift with Forks Here
Summary of Contents for HSP-176M-1500-HD
Page 3: ...ELECTRICAL SCHEMATIC 38 Electrical Parts List 38 TROUBLESHOOTING 39 ...
Page 19: ...16 16 GETTING TO KNOW YOUR MACHINE A I G H L J B F K C E D ...
Page 30: ...27 27 Using the Machine Incorrect Correct ...
Page 31: ...28 28 Incorrect Correct ...
Page 37: ...34 34 RAM PARTS DIAGRAM ...
Page 39: ...36 36 HYDRAULIC PUMP PARTS DIAGRAM ...
Page 43: ...40 40 NOTES ...