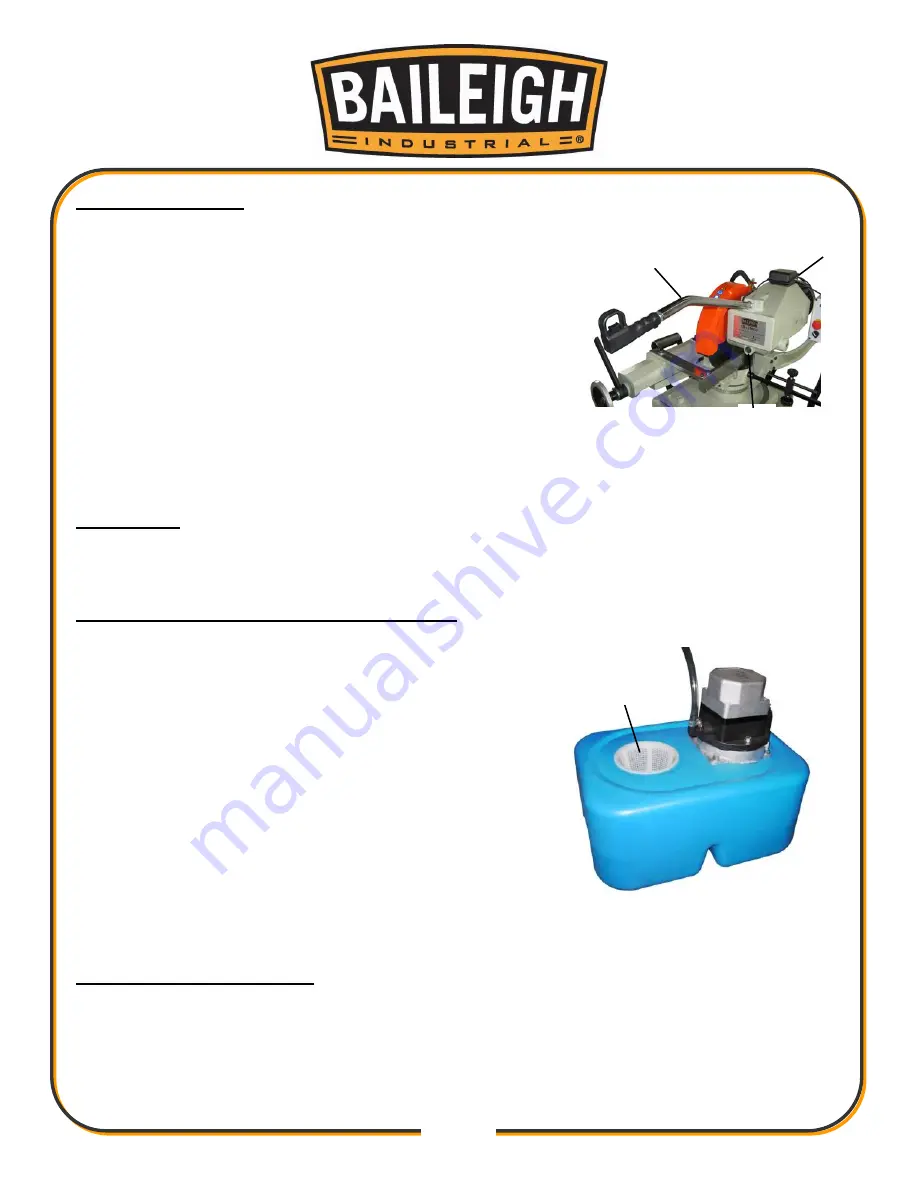
36
36
Yearly Maintenance
Change the oil in the gear case as follows:
•
Position the saw head in the horizontal position.
•
Remove the connecting plug (A) from the electrical box
socket and unscrew the feed handle (B).
•
Place a container under the drain hole (C) and remove the
drain plug.
•
Drain off the old oil.
•
Install the drain plug.
•
Raise the head to the up position, add 1.58 qt. (1.5L) oil
through the feed handle mounting hole.
•
Install and connect the feed handle.
Oil Disposal
•
Used oil products must be disposed of in a proper manner following local regulations.
Accessing and Cleaning the Coolant System
1. Remove the drain hose from the return screen.
2. Lift the tank and pump assembly off of the retaining
tray and slide the assembly out of the stand.
3. Remove and clean the filter (A). Replace if needed.
4. Pour out the coolant from the tray.
5. Wash out the dirt and debris.
6. Replace the filter and install the pump and tank
assembly so that the V-notch is over the retaining
flange.
7. Fill the tank with coolant solution by pouring
coolant through the chip strainer (A).
Oils for Lubricating Coolant
Any 10:1 (water to coolant) solution will work, however we recommend Baileigh B-Cool 20:1
(water to coolant) biodegradable metal cutting fluid. It has excellent cooling and heat transfer
characteristics, is non-flammable, and extends blade and machine life. Each gallon of
concentrate makes 21 gallons of coolant.
C
A
B
A
Summary of Contents for CS-350EU
Page 17: ...14 14 OVERALL DIMENSIONS Machine Dimensions when assembled...
Page 35: ...32 32 BLADE SELECTION CHART...
Page 42: ...39 39 PARTS DRAWING A...
Page 47: ...44 44 PARTS DRAWING B...
Page 51: ...48 48 ELECTRICAL PARTS FU1 FU2 FU3 KR1 KR2 TC SA1 A1 M2 internal...
Page 52: ...49 49 SB4 SB1 SA2 SB2 SB3 VR A1 Display...
Page 58: ...55 55 NOTES...
Page 59: ...56 56 NOTES...