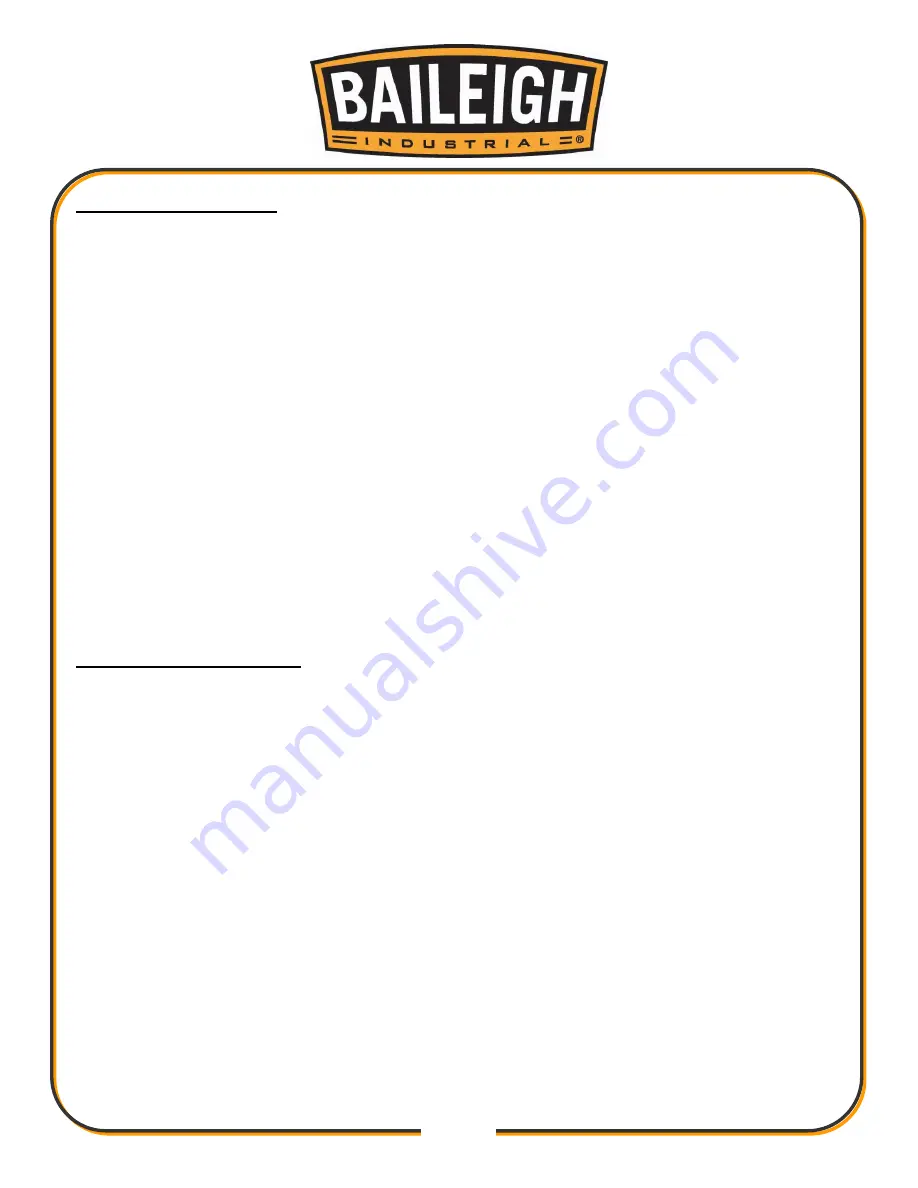
23
23
BEFORE EACH USE
•
For dusty operations, wear a face shield along with safety goggles.
•
It is important to choose the right blade for the material and the type of cutting you plan to
do. This saw is equipped with a bi-metallic blade which can be used to cut stainless steel,
steel, iron, brass, aluminum, wood, plastic.
•
Make sure the direction of rotation arrow on the blade matches the direction arrow on the
saw. The blade teeth should always point downward at the front of the saw.
•
Make sure the blade is sharp, undamaged and properly aligned. With the saw unplugged,
push the power-head all the way down. Rotate the blade by hand checking for clearance. If
the blade hits anything, make the adjustments shown in the Maintaining Maximum Cutting
Capacity section.
•
Never cut freehand.
•
Make sure the cut-off piece can move sideways after it is cut off. Otherwise, it could get
wedged against the blade and thrown violently.
•
Never turn the saw "ON" before clearing everything except the work piece beneath the
blade.
•
Never put lubricants on the blade while it is spinning.
Whenever Saw is Running
•
Never confine the piece being cut out.
•
Never hold it, clamp it, touch it, or use length stops against it. It must be free to move
sideways. If confined, it could get wedged against the blade and thrown violently.
•
Avoid awkward hand positions where a sudden slip could cause a hand to move into the
blade.
•
Let the blade reach full speed before cutting.
•
Feed the saw into the work piece only fast enough to let the blade cut without bogging down
or binding.
•
Before freeing jammed material, turn the switch off and unplug the saw. Wait for all moving
parts to stop.
•
After finishing a cut, keep holding the saw bow down, release the switch, and wait for all
moving parts to stop before moving your hands.
Summary of Contents for BS-712MS
Page 17: ...14 14 OVERALL DIMENSIONS...
Page 18: ...15 15 GETTING TO KNOW YOUR MACHINE A B C D E F G H I K J L...
Page 32: ...29 29...
Page 46: ...43 43 PARTS DIAGRAM A...
Page 47: ...44 44 PARTS DIAGRAM B...
Page 58: ...55 55 NOTES...
Page 59: ...56 56 NOTES...