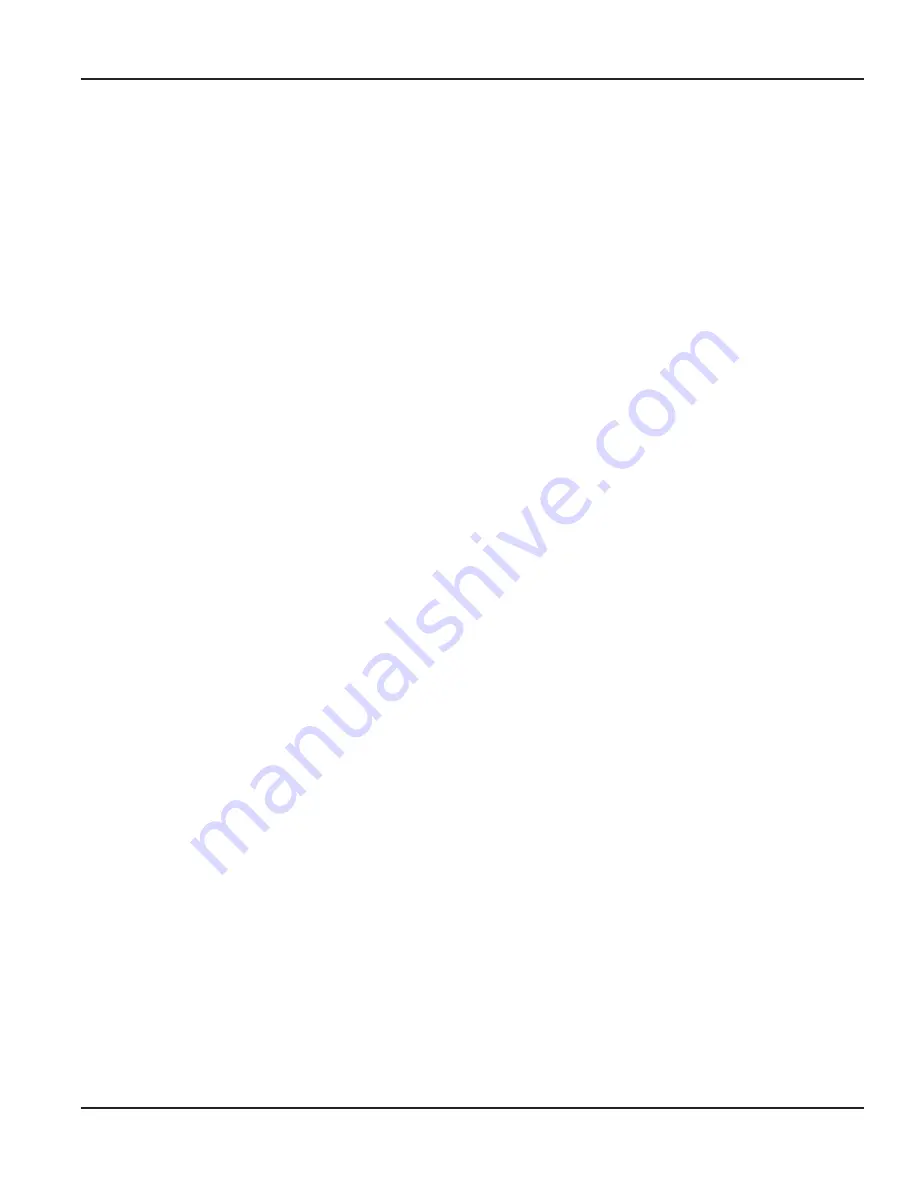
METEO INSTALLATION FOO STEAM SEOVICE
Steam measurement is one of the most difficult applications for differential pressure transmitter tubing and requires careful
consideration during installation Steam is usually at a high temperature, which will damage the transmitter In addition,
steam can vary between liquid or gaseous phase depending on temperature and pressure Due to this, the differential
pressure impulse tubing must be oriented in such a manner that it can operate with gas liquid, or a combination of the
two present
Installation Options
• Meter Orientation
—Gemini Cone meters can be installed in a horizontal or vertical position Horizontal is the standard
orientation, however where space is very limited, a vertical position may prove to be the best option
• Connection Tubing Orientation
—The orientation of the impulse tubing is dictated by the orientation of the meter, the
type quality of the steam being measured, and for vertical meter installations, the direction of flow When a vertical meter
run is used, the operator must give special consideration to the impulse tubing configuration to prevent liquid from being
trapped in gas differential pressure lines
• Condensate Chamber
—The condensate chamber is a liquid reservoir that helps prevent steam from entering the
differential pressure transmitter In most cases, a large-diameter tee is all that is required to collect the liquid However, if
the DP measuring instrument is designed with hydraulic/pneumatic bellows (such a Barton 202E chart recorder), a larger
volume condensate chamber will be required Modern DP transmitters have very little diaphragm movement and do not
require the large-volume condensate chamber
Horizontal Meter Installation
Install the pressure taps above the horizontal centerline (9…3 o'clock) of the primary device In condensing hot vapor service
such as steam, the fluid in the impulse lines is liquid that has been condensed from the vapor The use of a condensate
chamber is mandatory to prevent hot process fluid from damaging the transmitter Slope the impulse tubing upwards from
the cone meter to the condensate pots A condensate pot can be a tubing tee (for low volume DP instruments) or a full-size
condensate chamber (for high volume DP instruments) In either case, install the condensate pots at exactly the same level to
ensure accurate differential pressure readings Fill the line from the bottom of the tee to the transmitter mounted below the
tee to the point where excess fluid can drain back into the meter
In many cases, water (steam condensate) is used for the fluid fill However, in cold weather, the fluid must be protected
from freezing The fluid fill requires careful design with heat tracing and insulation to keep it in the liquid phase and to keep
both the high-pressure and low-pressure legs of the tubing at the same temperature (maintaining the liquid fill at the same
density) If practical, use a liquid leg fill fluid other than water Methanol is a possible substitute, but dibutyl phthalate is the
recommended fill fluid because it does not mix with water and remains liquid throughout a broad temperature range of,
–31…644° F (–35…340° C)
MPOOTANT
I
Be careful when using dibutyl phthalate. Follow all hazardous material guidelines (CAS No: 87-74-2).
Meter Installation for Steam Service
Page 17
June 2018
DPM-UM-00206-EN-03