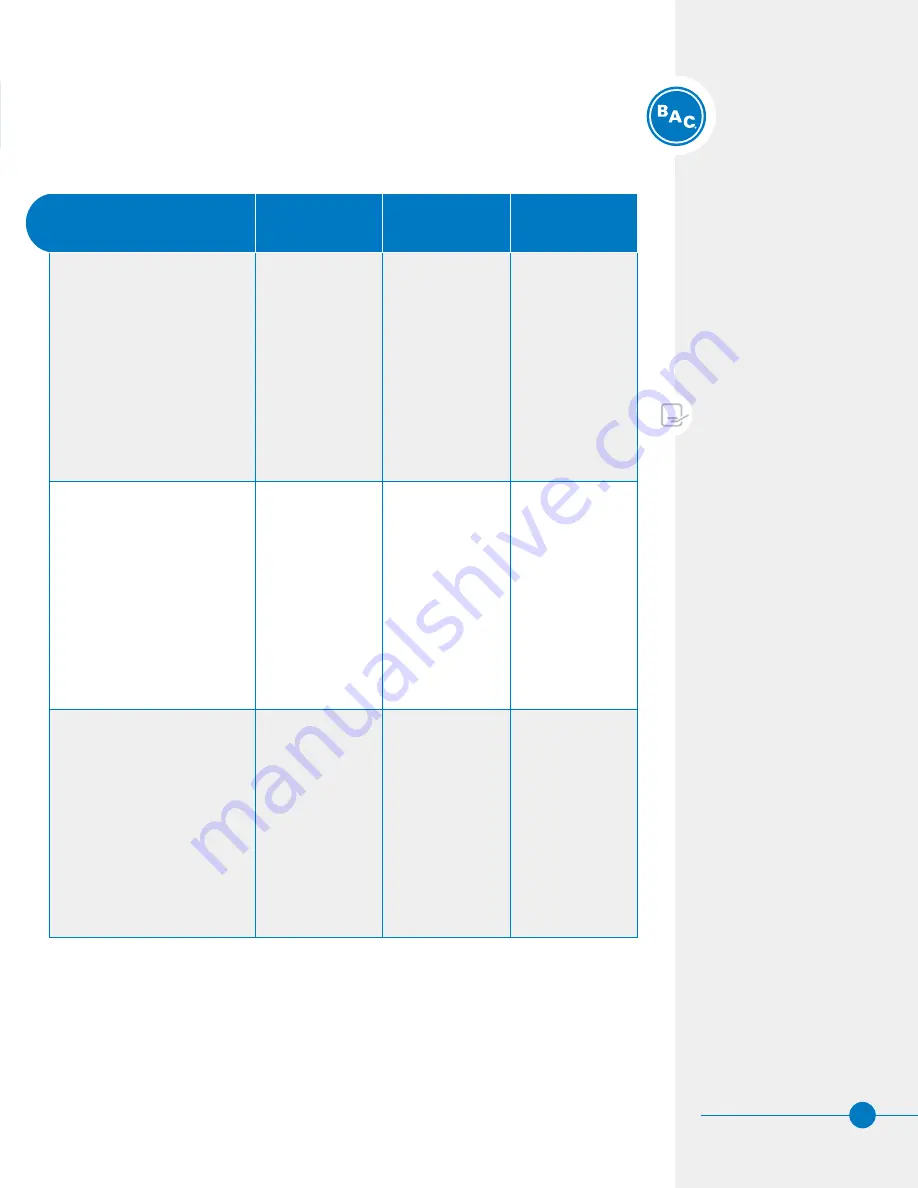
35
35
Positive Closure Damper hood and Insulation
The amount of auxiliary heat required can be substantially reduced by the use of a positive
closure damper hood and insulation on the hood and casing. The heat loss data can be
found in Tables 3, 4, 6, and 7.
Model Number
Standard Unit
Unit with PCD
hood
Unit with PCD hood
& Insulation
[1]
FXV-0806x-12D
FXV-0806x-16D
FXV-0806x-20D
FXV-0806x-24D
FXV-0806x-28D
FXV-0806x-32D
FXV-0806x-36D
FXV-0806x-24T
FXV-0806x-30T
FXV-0806x-36T
FXV-0806x-16Q
FXV-0806x-24Q
FXV-0806x-32Q
82,000
97,100
111,400
140,200
153,000
165,100
176,700
141,200
160,500
178,400
98,100
142,200
168,000
46,200
45,900
45,600
61,300
60,900
60,600
60,200
61,900
61,500
61,100
46,600
62,600
62,200
34,700
34,500
34,200
44,600
44,400
44,100
43,900
45,100
44,800
44,500
35,000
45,600
45,300
FXV-0809x-12D
FXV-0809x-16D
FXV-0809x-20D
FXV-0809x-24D
FXV-0809x-28D
FXV-0809x-32D
FXV-0809x-36D
FXV-0809x-24T
FXV-0809x-30T
FXV-0809x-36T
FXV-0809x-16Q
FXV-0809x-24Q
FXV-0809x-32Q
118,700
141,500
163,000
203,100
222,000
239,900
256,800
205,300
233,900
260,400
143,600
207,500
246,200
60,400
59,800
59,200
79,300
78,600
77,900
77,300
80,700
79,800
79,100
61,200
82,000
81,300
47,400
46,900
46,400
60,200
59,600
59,100
58,600
61,200
60,500
60,000
48,000
62,200
61,600
FXV-0812x-12D
FXV-0812x-16D
FXV-0812x-20D
FXV-0812x-24D
FXV-0812x-28D
FXV-0812x-32D
FXV-0812x-36D
FXV-0812x-24T
FXV-0812x-30T
FXV-0812x-36T
FXV-0812x-16Q
FXV-0812x-24Q
FXV-0812x-32Q
154,900
185,000
213,400
264,100
288,800
312,200
334,000
267,900
305,600
340,300
188,700
271,700
323,100
74,300
73,200
72,200
96,500
95,300
94,200
93,200
98,700
97,400
96,100
75,500
101,000
99,700
59,800
58,900
58,100
75,000
74,100
73,200
72,400
76,700
75,600
74,600
60,800
78,400
77,500
Table xa.
FXV-0806X thru FXV-0812X Heat Loss Data (BTW/hour)
[2]
NOTES:
1.
One inch thick PVC nitrite rubber
blend thermal insulation on both
the PCD hood and the casing
panels surround the coil.
2.
Heat loss is based on 50°F
(10°C) coil water and -10°F
(-23.3°C) ambient air with a
45 MPH wind. The fan(s) and
pump(s) are turned off.