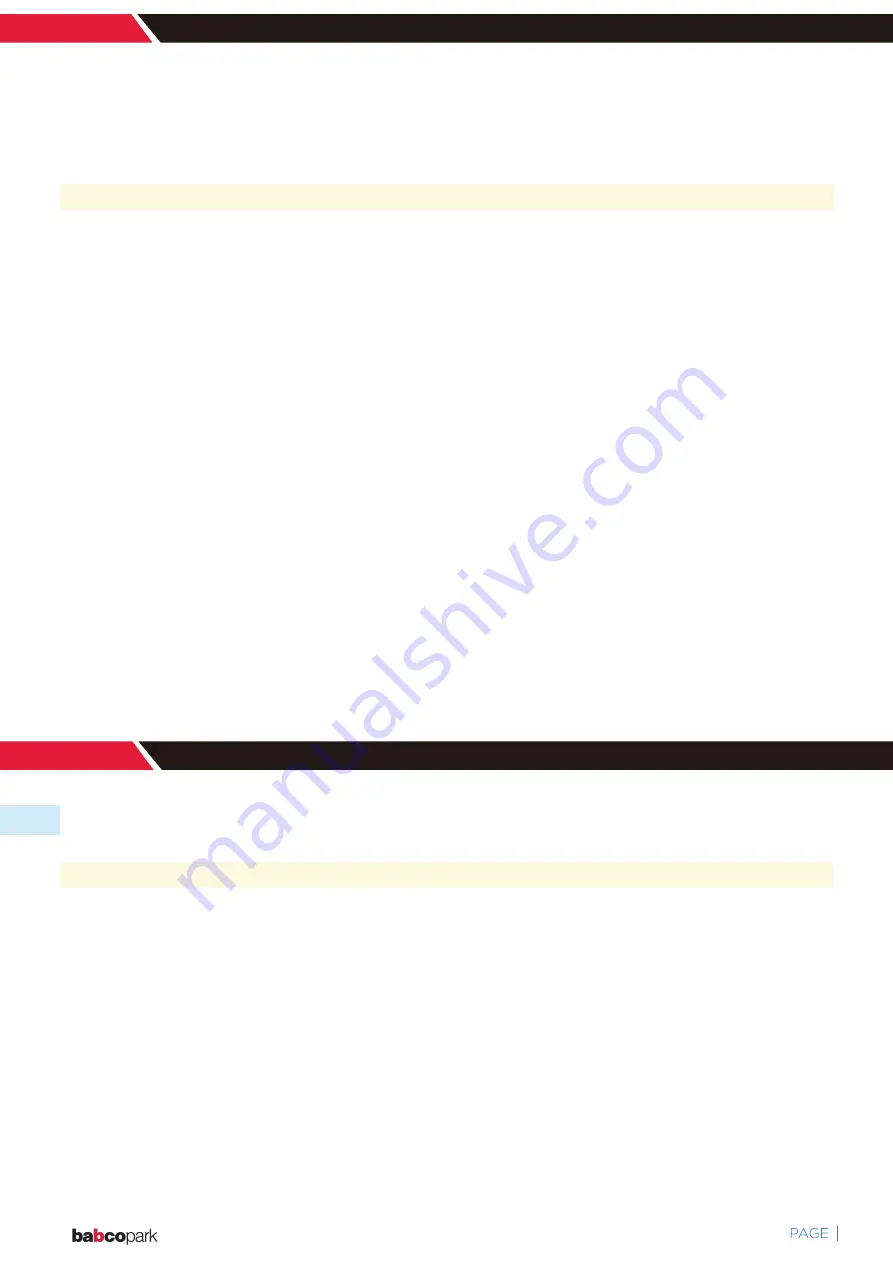
7.1.1
Basic cleaning of the
upper platform.
A regular cleaning of the
upper platform
helps to preserve the system and is absolutely essen�al.
Make
sure they are
swept clean by using a broom or vacuum cleaner.
Recommended frequency: At least 1 x yearly
7.1.2
Cleaning in winter
As the winter months cause more heavy wear due to snow, ice, road salt, chippings etc. when the pla�orm
surfaces are driven over, the following measures are to be observed:
7.1.2.1 In winter any regular condensa�on is to be removed in par�cular below the pla�orms.
Recommended frequency: When droplets form below the pla�orm
7.1.2.2 Snow, ice, road salt and dirt deposits are to be removed from the pla�orms.
Recommended frequency: In winter if required several �mes during the month
7
Surface Cleaning & Protection
7.1
Surface cleaning
6.2.4
Open the car door carefully to avoid any collision. Pay a�en�on to the waving plates and side beams in case
any falling down of person.
6.2.5
Make sure the car sizes and weight is in allowance range of this parking li� before leaving.
6.3
Operation
6.3.1
An
inspec�on o
f
equipment is necessary before opera�on
and to
make sure
lift
is
in good working order
.
6.3.2
Before first opera�
ng
, turn on
the
main switch, secondly turn on the power switch on switching cabinet, and
thirdly make sure the emergency stop bu�on on
the o
pera�on panel is open.
6.3.3
The power indicator light is off un�l both
the
main switch and power switch on switching cabinet is turned
on, that will make the circle of whole control system on.
6.3.4
Pay
a
�en�on
to
the movement of
the
pla�orm during
operation
. Opera�on
should
be stopped at once if
any abnormal movement found.
6.3.5
Turn the key by an�clockwise to make the pla�orm go up, and turn the key by clockwise to make the
pla�orm go down.
6.3.6
Keep holding the key switch to make
the
pla�orm move, which will stop at
when
releasing
the key switch.
6.3.7
Turn UP to make pla�orms ascend un�l stopped by top limit switch.
6.3.8
Top limit switch stops pla�orm li�ing at maximum height.
6.3.9
Turn DOWN to make pla�orm descend un�l upper pla�orm is level with ground floor.
6.3.9
Press the red and round bu�on, the emergency stop bu�on, to stop the movement of parking li� if any
accident happens or anything else
requires
t
he
equipment
to
stop. Rotate the emergency stop bu�on to reset it
a�er being sure the parking li� is in good condi�on again.
6.3.10
The buzzer keeps making a sound when pla�orms move up or down, as well as
when
the chain detec�on
mechanism finds any
loose
or broken
chain
and stops
the
machine
from operating
. Buzzer will not stop and
parking cannot
resume operation
un�l every chain is in good condi�on.
46
Operation
Surface Cleaning & Maintenance
Summary of Contents for Starke 2121
Page 1: ...User Manual for Pit Lift ...