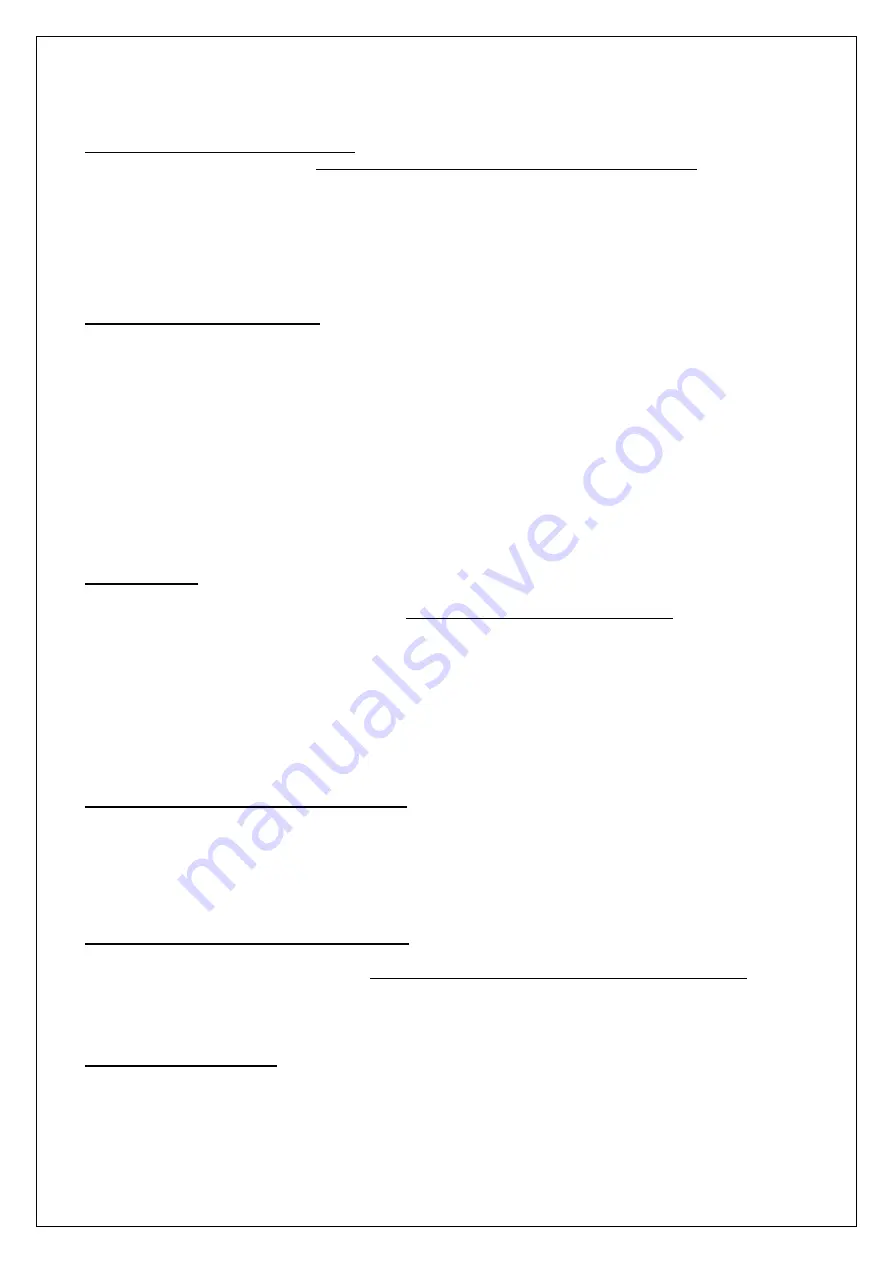
13
7.
Gently pull front panel outwards from the bottom and lift front panel upwards.
8.
REASSEMBLE IN REVERSE ORDER.
Removal of Burner for Service
Follow procedure described under GAINING ACCESS TO GAS AND/OR WATER SYSTEM;
1.
Undo barrel union located at in the centre of the gas manifold.
2.
Remove burner support screw by undoing wing-nut located on the bottom front of the appliance
frame.
3.
Gently lift burner upwards slightly and pull burner outwards.
4.
REASSEMBLE IN REVERSE ORDER.
Pilot and Flame Safeguard
Access to pilot assembly is gained by removing the wing-nut located to the left of the pilot assembly which
secures it to the burner support bar, and gently pull forward to gain greater access (refer picture).
1.
To service/remove the thermocouple;
a. Undo the nut located underneath and above the thermocouple at the pilot assembly and
gently pull thermocouple downwards.
b. Remove thermocouple from flame failure valve by unscrewing.
c. Reassemble in reverse order.
2.
To service/remove pilot burner;
a. Undo nut located underneath the pilot burner on the pilot assembly.
b. Gently pull down pilot flexible gas tube.
c. Remove injector from pilot and clean (if required).
d. Reassemble in reverse order.
3.
REASSEMBLE IN REVERSE ORDER.
Adjustments
Pilot
1.
Remove front panel as described under GAINING ACCESS TO GAS CONTROL.
2.
To increase gas pressure to pilot, turn adjustment screw located at the top right hand side of the
flame failure devise anti-clockwise.
3.
To decrease gas pressure to pilot, turn adjustment screw located at the top right hand side of the
flame failure devise clockwise.
4.
REASSEMBLE IN REVERSE ORDER ENSURING POSITION OF PILOT IS AS FOLLOWS;
Ensure pilot light head is light head is located no further than 45mm from the injector located
opposite the burner inlet.
Servicing Wok Spout
– Where Fitted
The Wok Spout has a few wearing parts and these comprise a single flow control O-ring in the tap body and
two sealing O-rings on the swivel spout. Whilst it is expected that servicing would only be required at
approximately 200,000 cycles, it recommended that a preventative service be carried out every two years.
Please contact manufacturer for service kit.
Servicing Knee Valve
– Where Fitted
The knee valve incorporates a cartridge design for ease of service.
1.
Follow procedure described under GAINING ACCESS TO GAS AND/OR WATER SYSTEM
2.
To gain access to knee valve cartridge undo knee valve where the deflector meets the cartridge
area.
3.
REASSAMBLE IN REVERSE ORDER.
Gas Type Conversion
The following parts componentry require changing the appliance from NG to LPG (vice-versa);
1.
Regulator.
2.
Burner.
3.
Pilot.
In case of any failure in the functioning of the knee valve, unscrew the head assembly and clean the