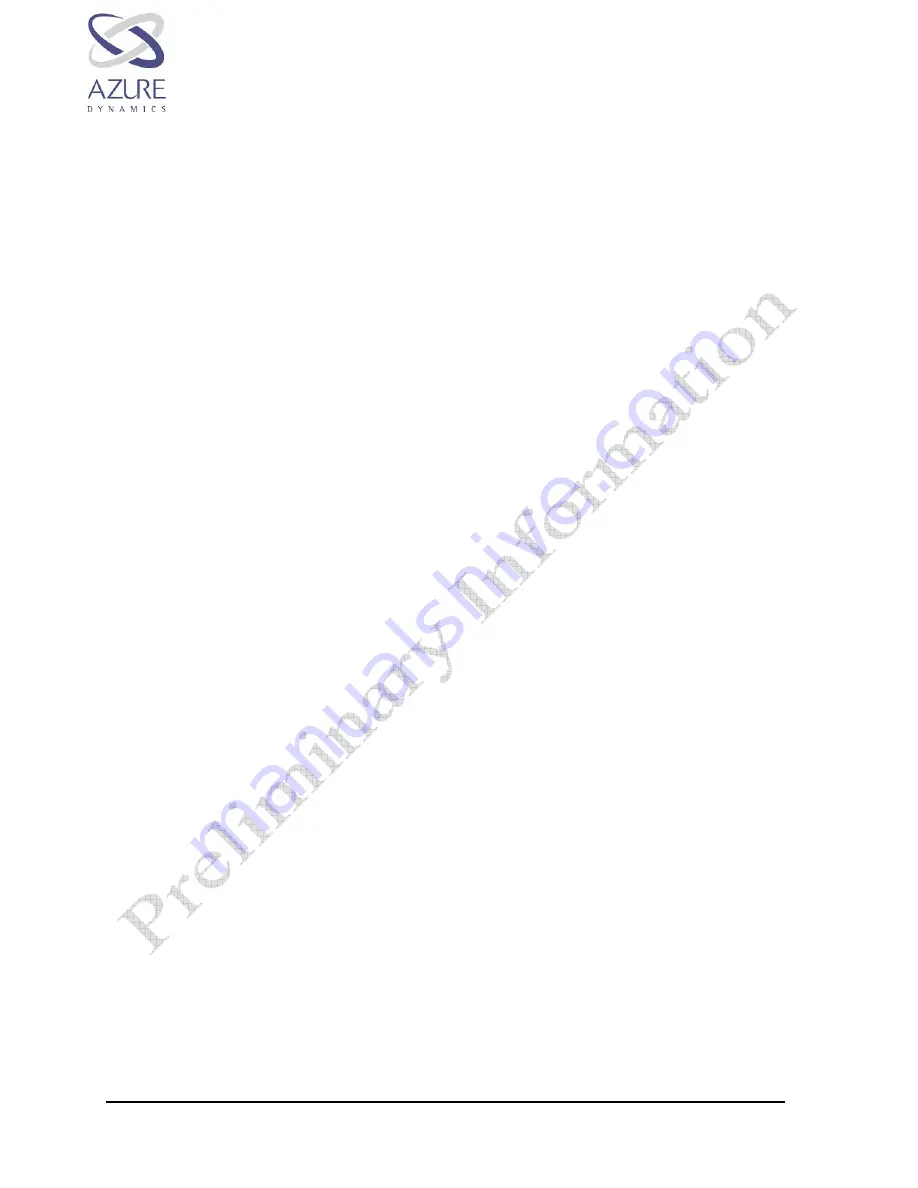
Proprietary
24
DMOC445 Manual and Operating Instructions
8. Installation
Requirements
1. Mounting
The DMOC is recommended for mounting with cooling fans face-up on a flat rigid surface and located in a
compartment that provides easy access for servicing and replacement.
The DMOC should be kept dry at all times, however, it is understood that some water splash to the
underside of a vehicle is unavoidable. The DMOC is factory sealed to withstand small amounts of
moisture.
•
Avoid locations where the DMOC will be routinely exposed to water.
•
Do not wash the DMOC with a pressure sprayer. Large amounts of water will cause a
malfunction.
•
If you have reason to believe water has entered the DMOC, do not open the case. Disconnect the
DMOC and return it for service as soon as possible.
•
When not in use, keep the protective plastic cap over the unit’s serial data port or connector.
•
Vibration damping mount should have ¼ inch nominal diameter threaded stud on each end of the
mount. A minimum of four (4) mounts are required to secure the DMOC on a stationary surface.
•
Position vibration damping mounts, DMOC, washers and fasteners as depicted on figure 7.
•
Torque all ¼ inch fasteners on the vibration damping mounts to 10-11 ft-lb.
•
If non-factory supplied vibration damping mounts are used, please consult with the new vibration
damping mount manufacturer for the proper fastener torque.
•
All power wires, cables and cooling hoses should be strain relieved thru the use of cable or hose
clamps that are attached to solid surface.
•
42.9mm [1.69 inched] diameter thru hole is provided to accept grommet or similar cable retention
device for the AC wires (see figure 4). Grommet should meet IP57.
•
26.7mm [1.05 inched] diameter thru hole is provided to accept grommet or similar cable retention
device for the battery positive and negative wires (see figure 6). Grommet should meet IP57.
DMOCs with extensive water damage may not be repairable. DMOCs returned to Azure Dynamics with
the factory seal broken will be ineligible for warranty service
All electronic systems must be isolated from vehicle vibration. This is done through the use of vibration
mounts.
All DMOCs are shipped from the factory with vibration mounts in the accessory kit. Attaching the DMOC
directly onto the solid surface or rigid vehicle frame without vibration damping mounts is not
recommended. This method of mounting of the DMOC will greatly reduce the life expectance of the unit
and void the unit warranty.
Vibration mounts must be operated in compression, with the weight of the DMOC on them. For improved
vibration protection, or when the DMOC is not mounted face-up, heavy-duty mounts must be used.
Heavy-duty mounts are available through Azure Dynamics.
Summary of Contents for DMOC445
Page 10: ...Proprietary 10 DMOC445 Manual and Operating Instructions 1 FIGURE 2 FIGURE...
Page 11: ...Proprietary 11 DMOC445 Manual and Operating Instructions 3 FIGURE 4 FIGURE...
Page 12: ...Proprietary 12 DMOC445 Manual and Operating Instructions 5 FIGURE 6 FIGURE...
Page 13: ...Proprietary 13 DMOC445 Manual and Operating Instructions 7 FIGURE...