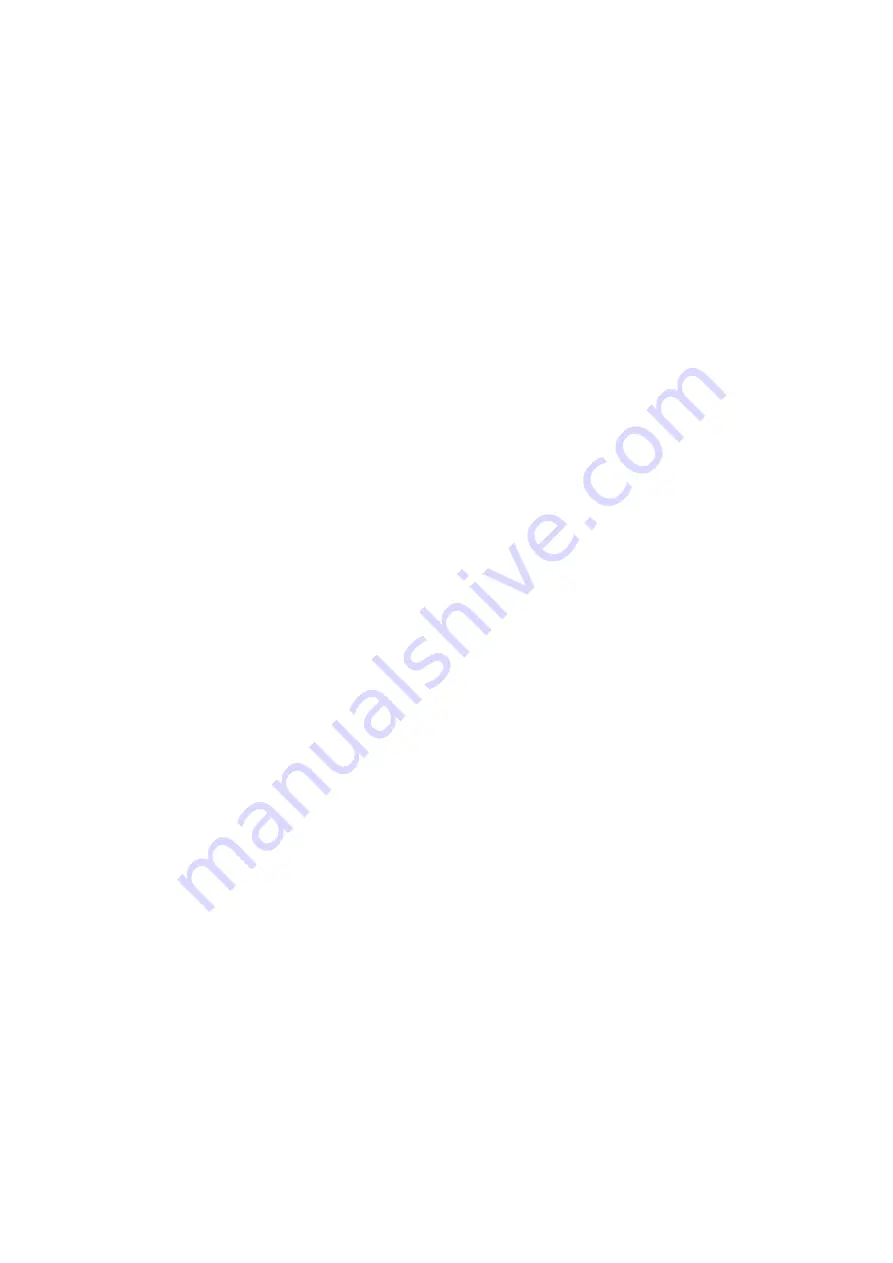
11
Malfunctions
Machine vibrates:
--
Clamping levers for height and diagonal adjustment are not tightly screwed.
---Sawing tool is not tightly screw.
Cuts are not clean/wood is burned:
---
Sawing tool is dull
---Sawing tool is incorrectly mounted.
Rapid sawing tool wear:
---Sawing tool is incorrectly sharpened.
---Contaminated wood(cement, sand , nails).
Motor becomes too warm:
(It is too hot to touch
with bare hands, it continuously shuts itself off.)
---By all means have a qualified electrician inspect the motor.
Machine comes to a stop:
---Overloading (feeding too rapid, Sawing tool is dull).
Wood is raised by the rear side of the saw blade:
---
Longitudinal limit stops are not parallel
---Splitting wedge is not aligned or crossing is too weak
The spindle height is difficult to adjust:
---Thoroughly clean and lubricate the threaded rod, gears and slide tracks.
---Check the operation of the clamping lever.
Miscellaneous:
--- Bearings make unusual noises: Inspect the bearings and replace if necessary.
----Check the tension of the V-belt (V-belts are accessible when the exhaust cover
is removed).
Summary of Contents for TS-200
Page 12: ...12 PARTS DIAGRAM A ...
Page 17: ...17 WIRING DIAGRAM ...