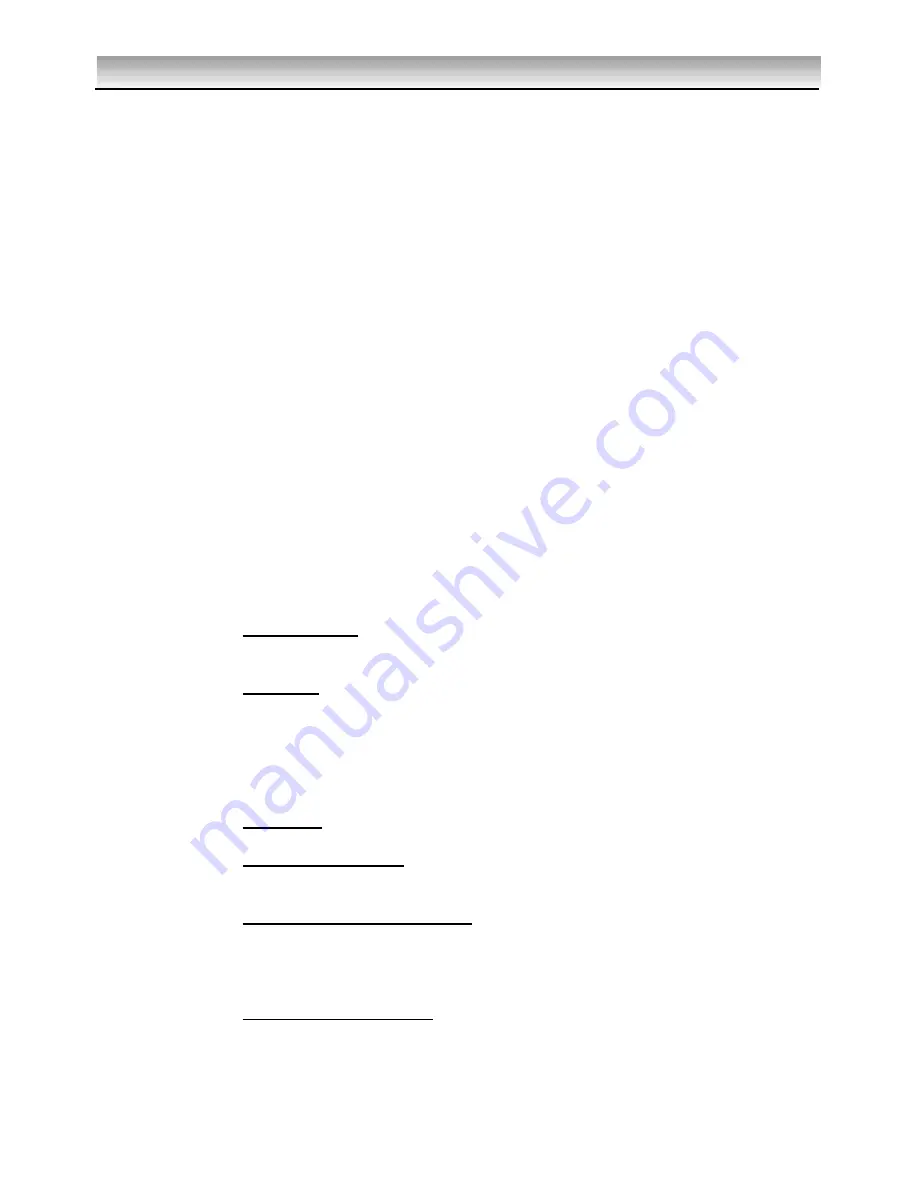
08
Parts Identification and Description
Please take some time to identify the various parts of your machine so that you are
familiar with the terminology we will use to enable you to set up and operate your Lathe
safely and correctly.
Headstock
The ‘engine block’ of the lathe, supports the motor, the spindle, the cover
for the change gears, the drive belt and the driven end of the leadscrew. It
also mounts the control panel for the motor and the selector for the
leadscrew.
Change gear
Protective cover, enclosing the motor pulley, the drive pulley and drive belt
cover
and the change gear.
Motor
220V d.c. motor
Mounting flange
The mounting flange is integral with the spindle and mounts all the material
carriers, (chucks, faceplate etc.), it is bored with a No.2 morse taper to accept
the headstock centre, The boring is then carried through the complete length
of the spindle (10.5mm clear) to allow long lengths of round bar to be
machined. Your Micro-Lathe is supplied with a chuck adaptor plate and chuck
already fitted to the mounting flange.
Chuck safety
A clear acetate cover mounted on a pivot bar on the rear top front face of the
cover
headstock. It can be tipped out of the way to access the chuck when it is
stationary, and repositioned over the chuck during operation. It is safety
interlocked, if it is not in position the motor will not run, or the motor will stop
if it is moved whilst the spindle is turning.
Motor control
Power On LED
panel
Green LED that indicates that power is available to the motor. i.e. mains is
applied, fuse is intact and the Emergency Stop switch is not activated.
Fault LED (marked UNNORMAL)
Amber LED that indicates that there is a fault or an incorrect control
sequence. e.g. the chuck guard interlock has been activated or the speed
control is activated without forward or reverse direction being selected.
The Motor will not run if the fault LED is illuminated. If the safety interlock is
activated, the safety interlock will remain in force until the interlock is reset
and the start sequence re-initiated.
Fuse Cap
Access cap for the 20mm fuse cartridge (1 Amp 250V).
Speed Control Knob
Round raised ridge knob connected to the circuit that controls the motor
speed (100-2000 rpm).
Forward /Off/Reverse Switch
Three position switch that controls the direction of rotation of the spindle.
Forward indicates that the spindle is turning toward the operator; reverse,
the spindle is turning away from the operator. The centre OFF position
inhibits the spindle from turning in either direction, under motor drive.
Emergency Stop Switch
Red Domed Mushroom switch; if pressed it removes all power to the
machine. It is a ‘knock off, stay off,’ switch. To reset the switch the domed
head must be turned clockwise, which will allow the switch to unlatch and
‘spring out’ and reset itself.