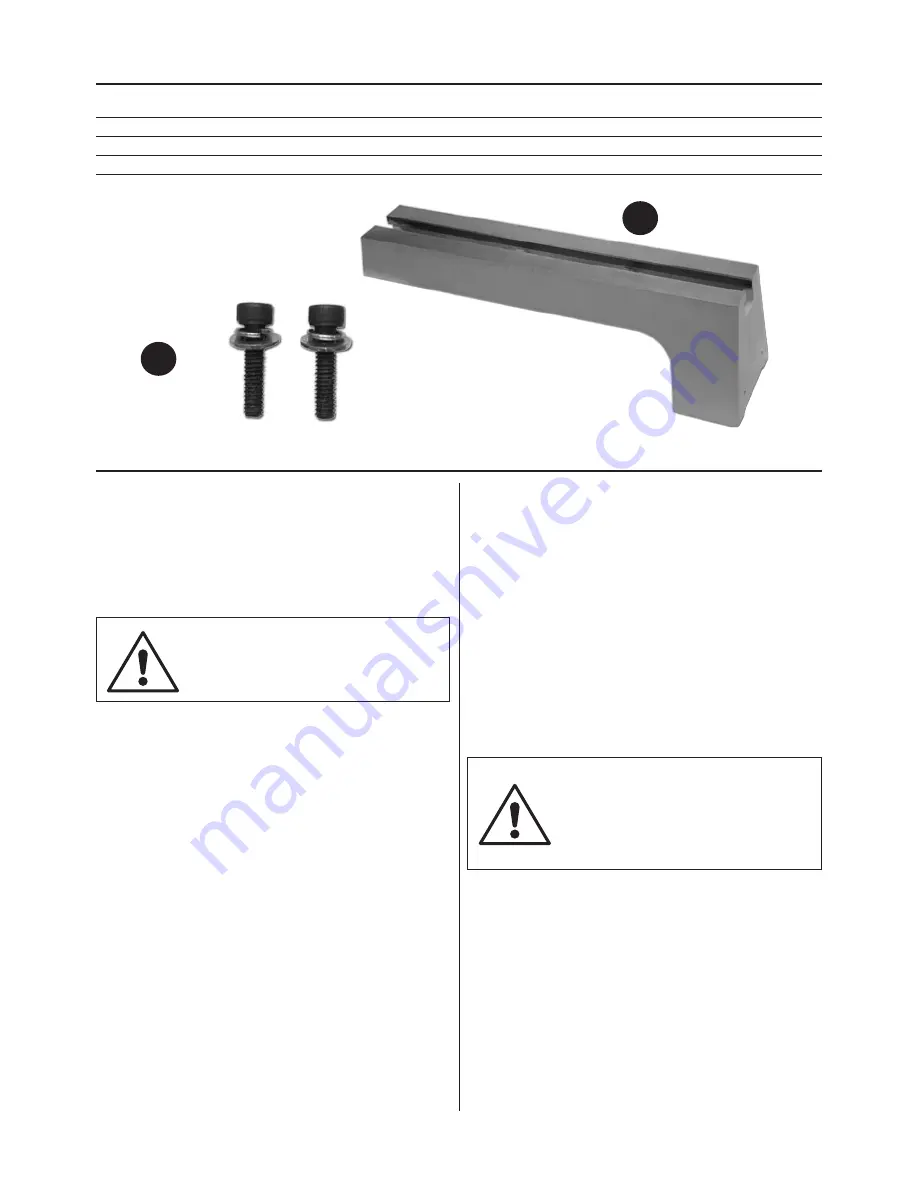
4
Quantity
Item
1 No
Extension Bed (Product code: 951249)
2 No
5
/
16
” x 1” Caphead Bolts & Spring/washer
Optional Accessories
H
I
I
H
General Instructions for 230V Machines
Good Working Practices/Safety
Primary Precautions
Work Place/Environment
The following suggestions will enable you to observe
good working practices, keep yourself and fellow
workers safe and maintain your tools and equipment
in good working order.
WARNING! KEEP TOOLS AND
EQUIPMENT OUT OF THE
REACH OF YOUNG CHILDREN
These machines are supplied with a moulded 13
Amp. Plug and 3 core power cable. Before using the
machine inspect the cable and the plug to make sure
that neither are damaged. If any damage is visible,
have the tool inspected/repaired by a suitably
qualified person. If it is necessary to replace the plug,
it is preferable to use an ‘unbreakable’ type that will
resist damage. Only use a 13 Amp plug, and make
sure the cable clamp is tightened securely. Fuse as
required. If extension leads are to be used, carry out
the same safety checks on them, and ensure that they
are correctly rated to safely supply the current that is
required for your machine.
Make sure when the machine is placed that it sits
firmly on the bench or stand, that it does not rock,
that it is sufficiently clear of adjacent obstacles so
that you have unimpeded access to all parts of the
machine. The machine is designed for indoor use, do
not use when or where it is liable to get wet. Keep the
machine clean; it will enable you to more easily see
any damage that may have occurred.
Clean the overall machine with a damp soapy cloth
if needs be, do not use any solvents or cleaners, as
these may cause damage to any plastic parts or to
the electrical components. Clean the machine
components with a lightly oiled cloth. If the machine
is liable to be standing idle for any length of time
a light coat of machine or spray oil will minimise
rusting.
Keep the work area as uncluttered
as is practical, this includes personnel
as well as material. Under no circum-
stances should CHILDREN be allowed
in work areas.
It is good practice to leave the machine unplugged
until work is about to commence, also make sure
to unplug the machine when it is not in use, or
unattended. Always disconnect by pulling on the
plug body and not the cable. Once you are ready to
commence work, remove all tools used in the setting
operations (if any) and place safely out of the way.
Re-connect the machine.
Carry out a final “tightness” check e.g. chuck or face
plate, work piece, tool rest, etc., check that the
correct speed has been selected.
Summary of Contents for AT1416VS
Page 14: ...Parts Breakdown 14...
Page 15: ...Parts Breakdown 15...
Page 16: ...Parts List 1 16...
Page 17: ...Parts List 2 17...
Page 18: ...Parts List 3 18...
Page 20: ...Wiring Diagram 20...