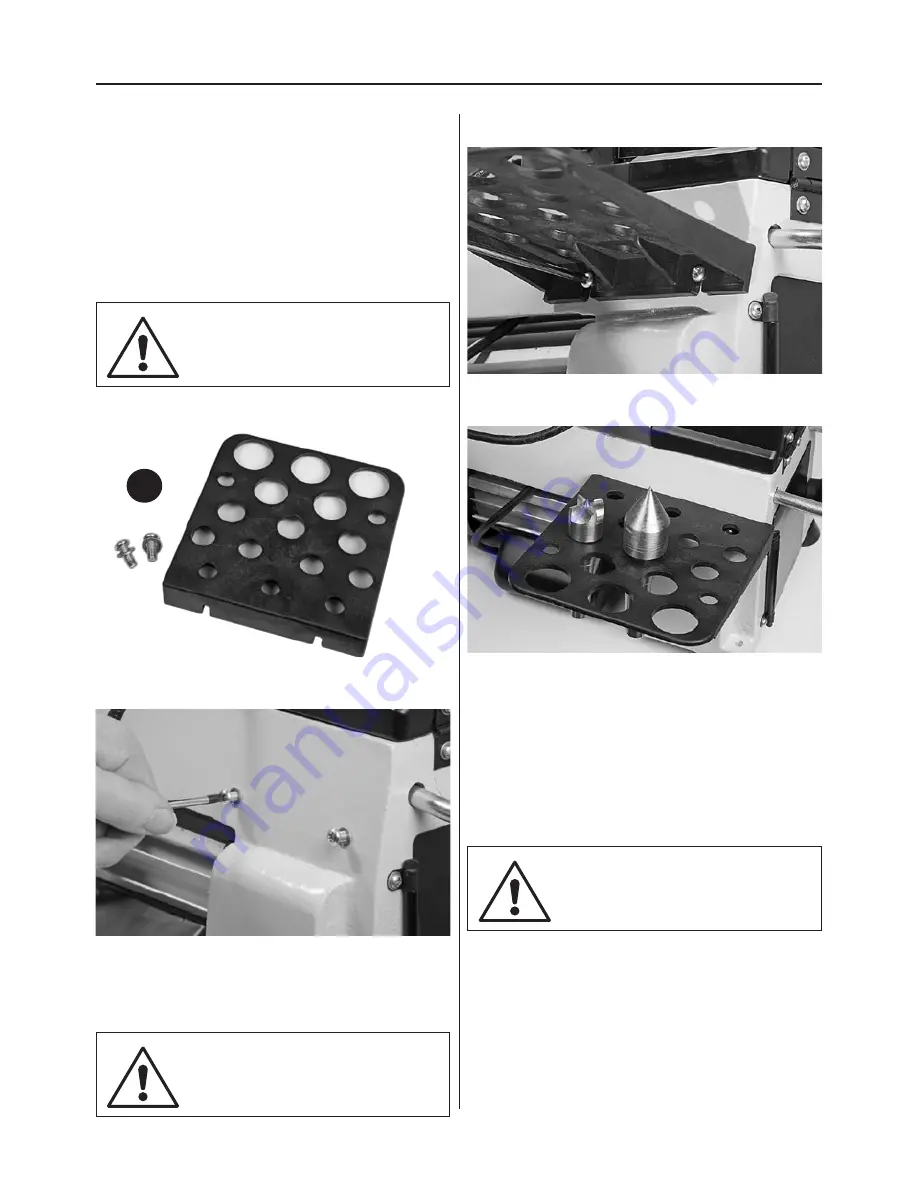
Assembly
6
Locate the bed extension (J) and the two Hex screws
and spring/washers, (see fig 7) position the bed
extension against the end of the lathe and line up
the pre-drilled holes, (see figs 8-9). Place a washer and
spring washer over the Hex screws and lightly screw
them into the threaded holes, (see fig 10).
Optional Bed Extension
Release the tailstock clamping lever and position the
tailstock across the join to align both beds, re clamp
the tailstock in position and tighten both Hex screws.
(see figs 11-12). Both beds are now aligned.
Fig 03
Fig 05
Fig 04
Fig 06
Locate the tool holder (I) the two Phillips screws and
washers. (see fig 3) Place a washer over the screws
and screw them into the two pre-drilled holes below
the headstock, (see fig 4).
NOTE GIVE ADEQUATE GAP
BETWEEN THE SCREW HEAD
AND LATHE CASTING!
I
Line up the machined slots in the tool holder (I)
and slide the holder down over Phillips screws then
lightly tighten the screws to clamp the holder in
place, (see figs 5-6).
Tool Holder
DON’T OVERTIGHTEN THE
PHILLIPS SCREWS AS THE
HOLDER IS ONLY PLASTIC!
NOTE: DON’T TIGHTEN THE
SCREWS AT THIS POINT!
NOTE: There are also two pre-drilled holes under
the tailstock if you wish to mount the tool holder
there.