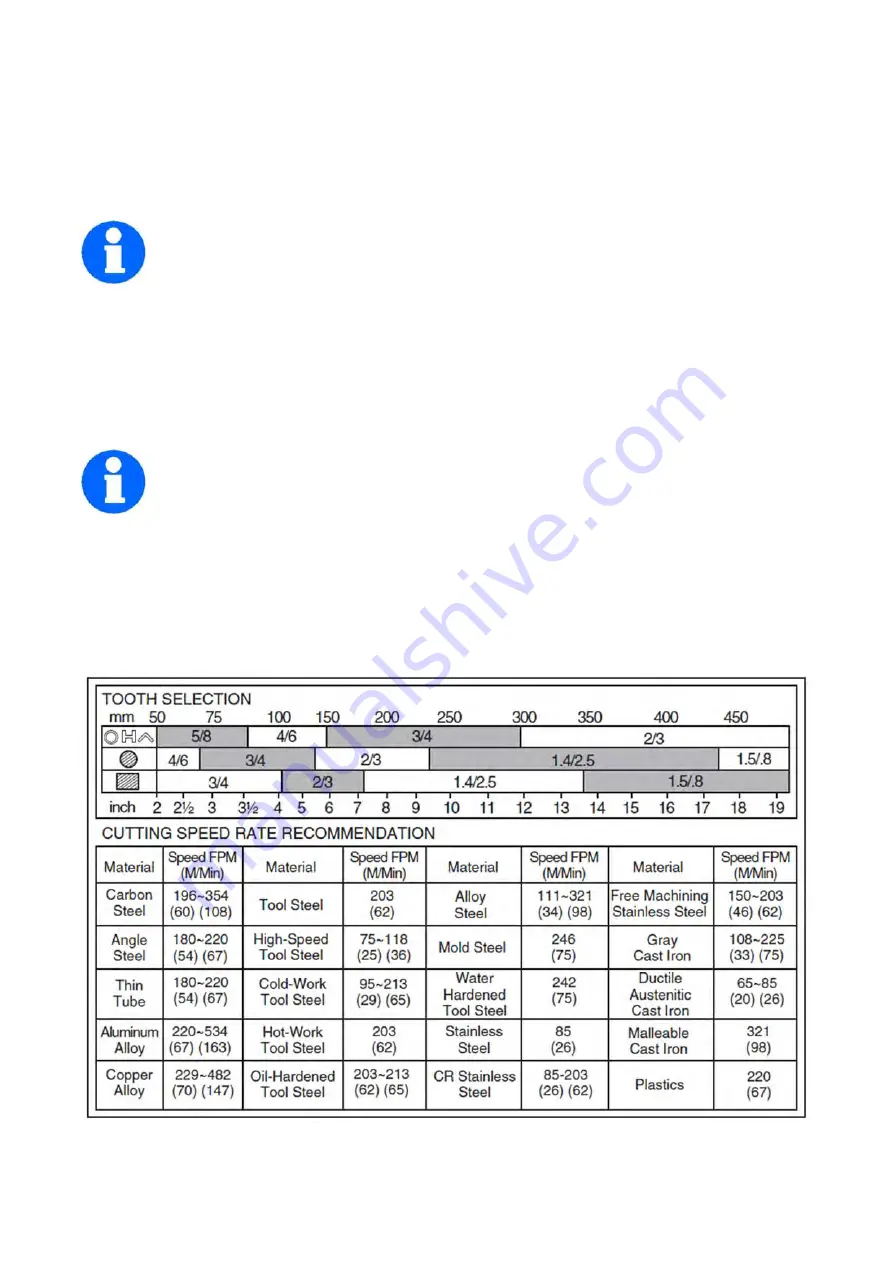
24
4.9 Blade Selection
The chart below is a basic starting point for choosing blade type based on teeth per inch (TPI) for
variable tooth pitch blades and for standard raker type bimetal blades/HSS blades. However, for
exact specifications of bandsaw blades, contact the blade manufacturer.
Here are some general rules of thumb with respect to bandsaw blade use.
▲
At least three teeth must contact the metal at any phase of the cut. Otherwise, the teeth can
load up with metal, fracture, and break off. If the TPI is too high, the teeth can load up with material
and overheat, damaging the blade.
▲
For a faster but rougher cut, use a blade with a lower TPI and a higher feed rate.
▲
For a slower but smoother cut, use a blade with more TPI and a lower feed rate.
To select the correct blade TPI:
1. Measure the material thickness. This measurement is the length of cut taken from
where the tooth enters the workpiece, sweeps through, and exits the workpiece.
2. Refer to the "Material Thickness" row of the blade selection chart in Figure 21, and
read across to find the workpiece thickness you need to cut.
3. Refer to the "Shape" of metal and "Material Type" columns, and find the shape and material to be
cut.
4. In the applicable row, read across to the right and find the box where the row and column
intersect. Listed in the box is the minimum TPI recommended for the variable tooth pitch blades,
and the TPI for bimetal raker blades in parentheses.
Summary of Contents for 700103
Page 3: ......
Page 4: ......
Page 12: ......
Page 14: ...10 2 6 Dimensions...
Page 15: ......
Page 16: ......
Page 17: ......
Page 18: ......
Page 19: ......
Page 21: ......
Page 22: ......
Page 23: ......
Page 24: ......
Page 25: ......
Page 30: ......
Page 33: ......
Page 36: ...7 Diagram Part list 33 7 1 Diagram and part list for MCB128SHD Part 1...
Page 40: ......