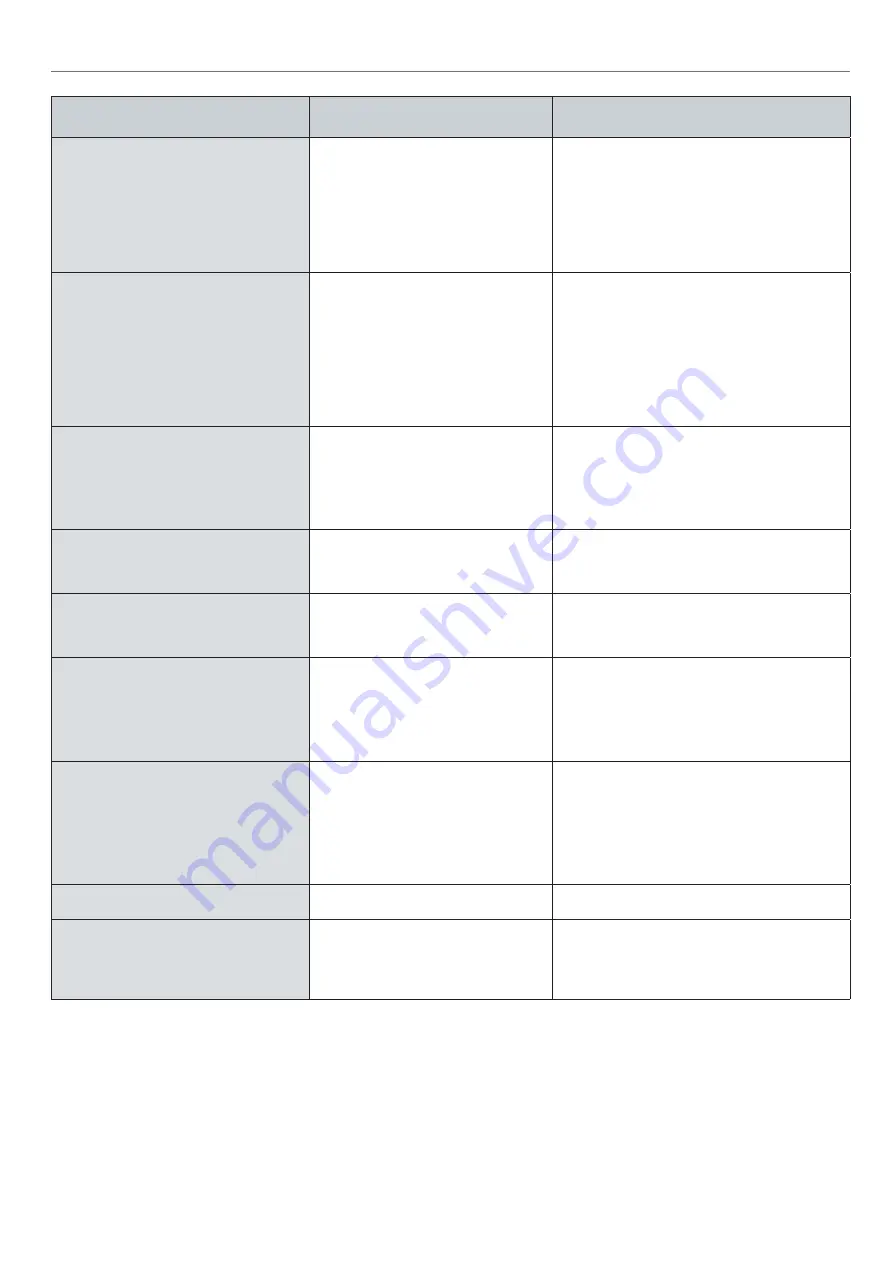
TROUBLESHOOTING
23
TROUBLE
PROBABLE CAUSE
REMEDY
Noisy Operation
1. Incorrect belt tension
2. Dry spindle
3. Loose spindle pulley
4. Loose motor pulley
1. Adjust the tension
2. Lubricate spindle
3. Checking tightness of
retaining nut on pulley,
and tighten if necessary
4. Tighten set screws in pulleys
Drill bit burns
1. Incorrect speed
2. Chips not coming out of hole
3. Dull drill bit
4. Feeding too slow
5. Not lubricated
1. Change speed
2. Retract drill bit frequently
to clear chips
3. Resharpen drill bit
4. Feed fast enough-allow drill
bit to cut.
5. Lubricate drill bit
Drill bit leads off hole not round
1. Hard grain in wood or lengths of
cutting lips and/or angles not equal
2. Bent drill bit
1. Resharpen drill bit correctly
2. Replace drill bit
Wood splinters on underside
1. No “back-up material” under
workpiece
1. Use “back-up material”
Work piece torn loose from hand
1. Not supported or clamped
properly
1. Support work piece or clamp it
Drill bit binds in work piece
1. Work piece pinching drill bit
or excessive feed pressure
2. Improper belt tension
1. Support work piece or clamp it
2. Adjust tension
Excessive drill bit run out or wobble
1. Bent drill bit
2. Worn spindle bearings
3. Drill bit not properly
installed in chuck
4. Chuck not properly installed
1. Use a straight drill bit
2. Replace bearings
3. Install drill bit properly
4. Install chuck properly
Quill returns too slow or too fast
1. Spring has improper tension
1. Adjust spring tension
Chuck will not stay attached to
spindle it falls off when trying to
install it
1. Dirty, grease or oil on the tapered
inside surface of chuck or on the
spindle’s tapered surface
1. Make sure all surfaces are free of dust
and grease
Summary of Contents for 107704
Page 4: ...WHAT S INCLUDED 4 1 2 5 3 4a 4 4b 6 7 8 9 11 13 12 10 16 17 18 14 15 ...
Page 24: ...EXPLODED DIAGRAM PARTS LIST 24 MODEL ZQJ4132K AP540PD ...
Page 27: ...EXPLODED DIAGRAM PARTS LIST 27 ...
Page 28: ...WIRING DIAGRAM 28 ...
Page 29: ...NOTES 29 ...
Page 30: ...NOTES 30 ...
Page 31: ...NOTES 31 ...