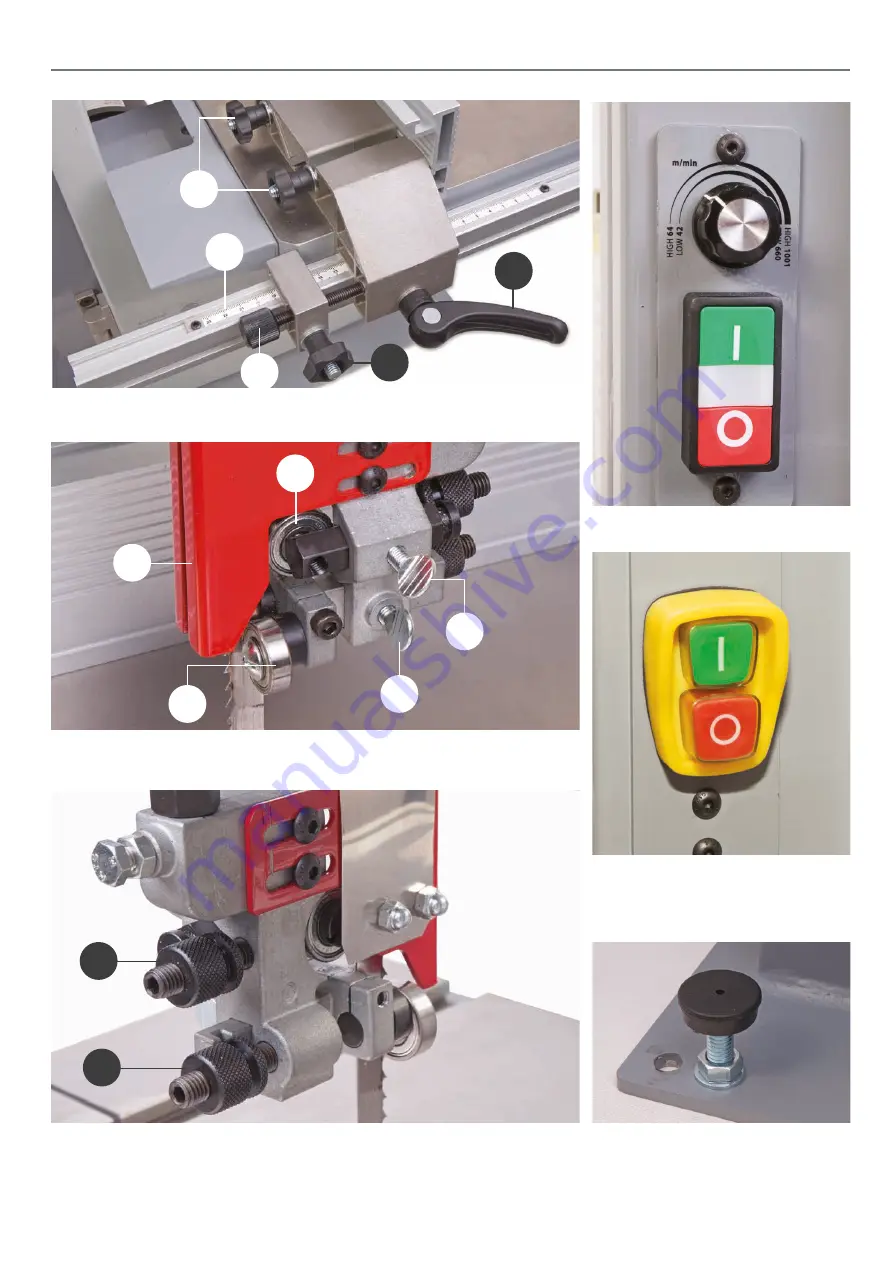
Illustration & Parts Description
11
The Variable speed control for model AT1854BV
ON/OFF control buttons for model AT1854B
Micro adjuster knob (A), Micro adjuster clamp (B), Fence assembly clamping handle (C),
Fence scale (D) and Fence clamping knobs (E)
Lower wheel door stop
Upper guide bearings (A), Upper guide bearing butterfly clamping screw (B),
Rear thrust bearing butterfly clamping screw (C), Rear thrust bearing (D), Upper blade guide guard (E)
Rear thrust bearing adjusting knob (A) and adjusting knob for the upper guide bearing assembly (B)
Model AT1854B
Model AT1854BV
A
B
C
D
E
B
A
E
D
C
A
B
Summary of Contents for AT1854B
Page 9: ...Machine Footprint 9 540mm 590mm 850mm 1530mm 280mm ...
Page 34: ...Exploded Diagram List 34 Model AT1854B BS11 ...
Page 37: ...Exploded Diagram List 37 Model AT1854BV BS11 INV Continues Over ...
Page 40: ...Wiring Diagram for AT1854B 40 ...
Page 41: ...Wiring Diagram for AT1854BV 41 ...
Page 42: ...Notes 42 ...
Page 43: ...Notes 43 ...