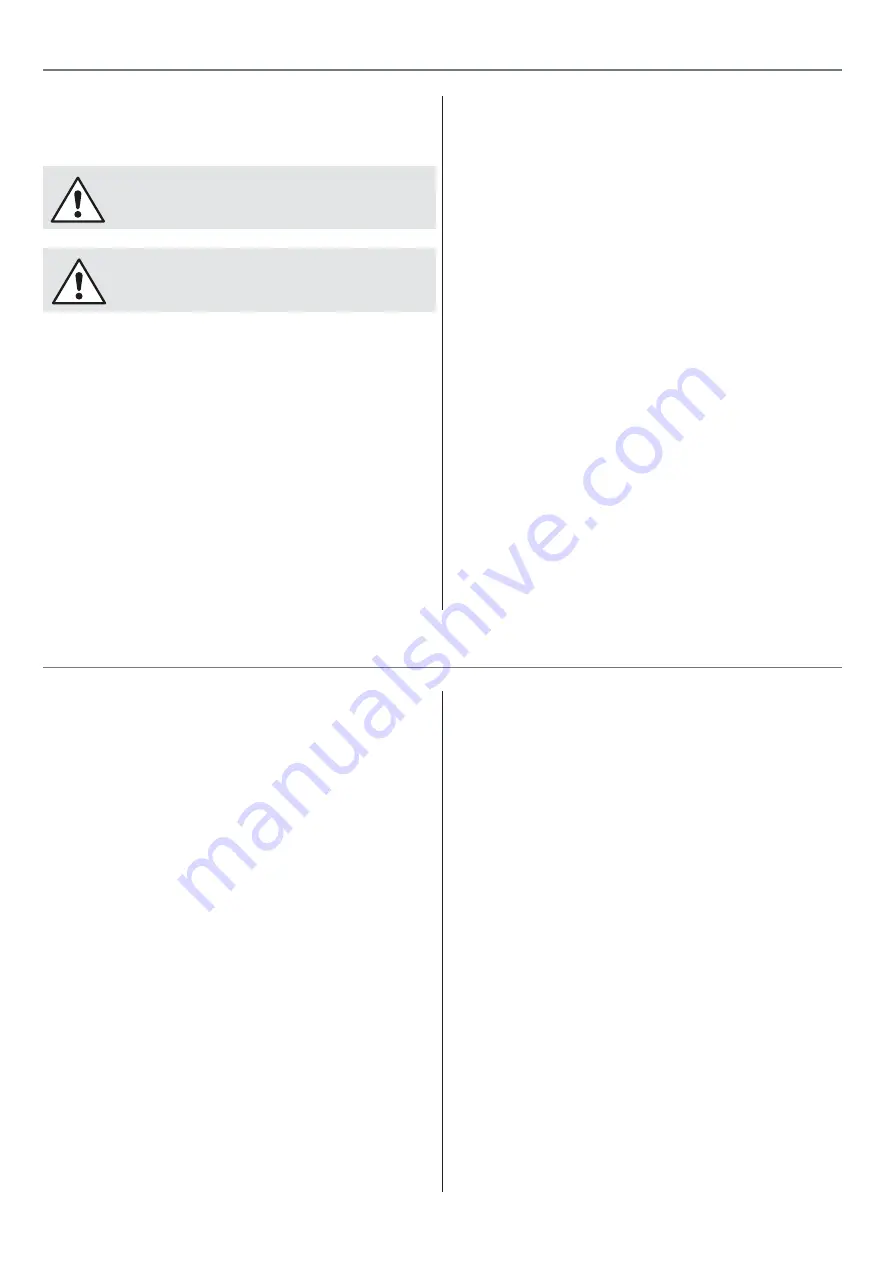
General Instructions for 230V Machines
4
Specific Precautions Using Thicknessers
Most machines currently, are well interlocked to ensure that
the machine must be in the correct configuration to perform
one task or the other. Make yourself familiar with these
configurations and do not try to use the machine in a half
and half state; or rig the interlocks to enable you to do so.
• Lower the thicknessing hood and lock in place.
• Connect the dust extraction. Ensure the hose will not foul
any materials being passed through the machine.
• Check the height of the thicknessing table.
• Engage the autofeed mechanism.
• Check blade inserts for damage, chips etc.
Rotate or replace if required.
• Periodically, clean any excess build up of resin from the
thicknessing table, and apply any proprietary brand of
lubricating agent.
NOTE, Consideration should be given to the type of finish you
will be applying to the surface when you select your cleaning/
lubrication agent.
The following will enable you to observe good working
practices, keep yourself and fellow workers safe and maintain
your tools and equipment in good working order.
WARNING!! KEEP TOOLS AND EQUIPMENT
OUT OF REACH OF YOUNG CHILDREN
Mains Powered Tools
• Tools are supplied with an attached 13 Amp plug.
• Inspect the cable and plug to ensuree that neither are
damaged. Repair if necessary by a suitably qualified person.
• Do not use when or where it is liable to get wet.
Workplace
• Do not use 230V a.c. powered tools anywhere
within a site area that is flooded.
• Keep machine clean.
• Leave machine unplugged until work is about to commence.
• Always disconnect by pulling on the plug body and not the
cable.
• Carry out a final check e.g. check the cutting tool
is securely tightened in the machine and the correct
speed and function set.
• Ensure you are comfortable before you start work,
balanced, not reaching etc.
• Wear appropriate safety clothing, goggles, gloves,
masks etc. Wear ear defenders at all times.
• If you have long hair wear a hair net or helmet to prevent it
being caught up in the rotating parts of the machine.
• Consideration should be given to the removal of rings and
wristwatches.
• Consideration should also be given to non-slip footwear etc.
• If another person is to use the machine, ensure they are
suitably qualified to use it.
• Do not use the machine if you are tired or distracted
• Do not use this machine within the designated safety areas
of flammable liquid stores or in areas where there may be
volatile gases.
• Check cutters are correct type and size, are undamaged
and are kept clean and sharp, this will maintain their
operating performance and lessen the loading on the
machine.
• OBSERVE…. make sure you know what is happening
around you and USE YOUR COMMON SENSE.
KEEP WORK AREA AS UNCLUTTERED AS IS
PRACTICAL. UNDER NO CIRCUMSTANCES SHOULD
CHILDREN BE ALLOWED IN WORK AREAS.
Summary of Contents for 106202
Page 7: ...Machine Dimensions 7 1 050mm 1 500mm 1 020mm 610mm ...
Page 20: ...Exploded Diagram Parts List 20 ...
Page 23: ...Exploded Diagram Parts List 23 ...
Page 24: ...Wiring Diagram 24 ...
Page 25: ...Notes 25 ...
Page 26: ...Notes 26 ...
Page 27: ...Notes 27 ...