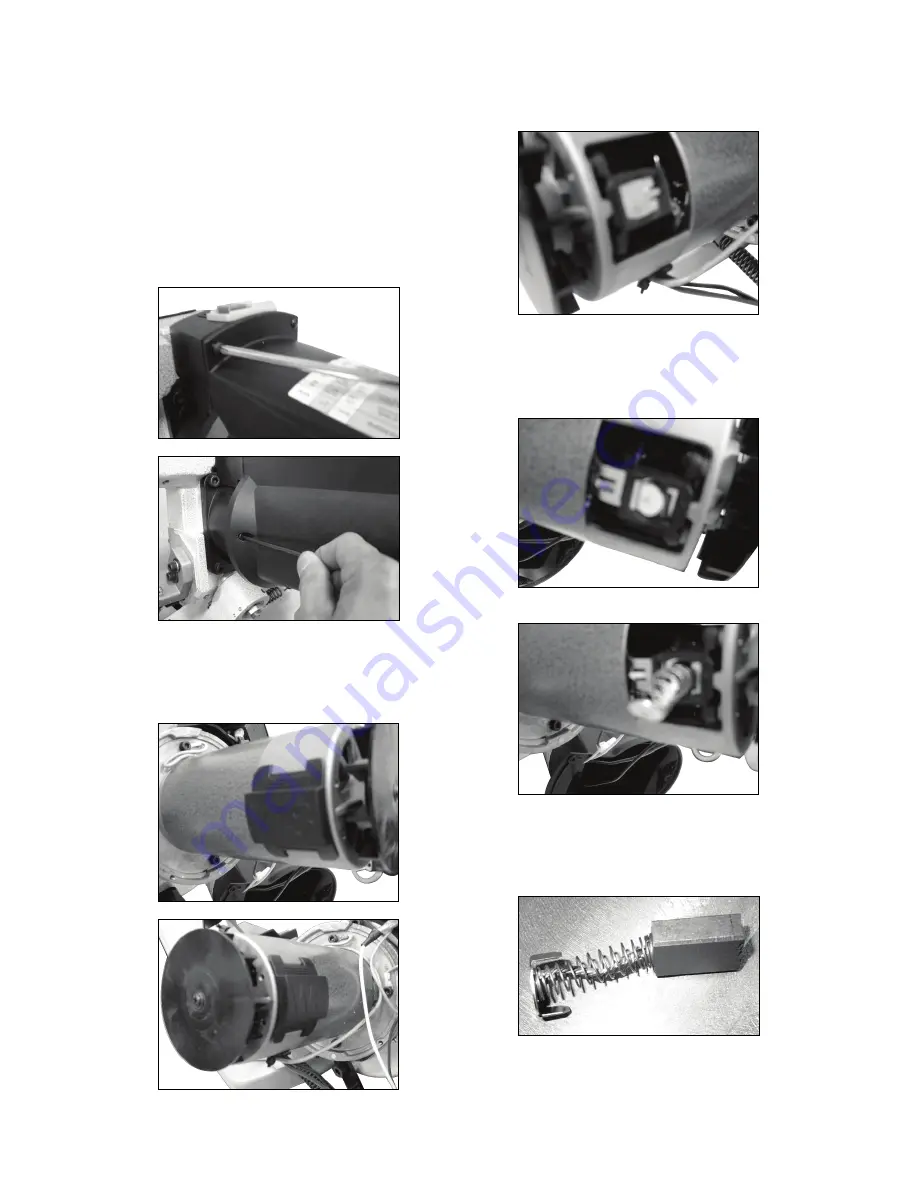
- 11 -
Changing the Motor Carbons
Brushes
If the motor is making an unusual noise then the
carbon brushes may need to be replaced.
1. Disconnect machine from power supply.
2. Remove two tap screws connected with
on/off switch’s box, and three Phillips head
screws around cover base. (Fig. 20)
Fig. 20
3. Opened the motor’s cover; there are two
plastic covers on the motor (Fig.21).
Remove plastic covers.
Fig. 21
4. There are coppers sheet with wiring
covered on the carbon brushes (Fig.22).
Fig. 22
5. Slide copper sheet to the one way (Fig.23),
the carbon brush will jumps out of the lock
(Fig.24).
Fig. 23
Fig. 24
6. Replace the carbon brushes
(Fig. 25).
Both
brushes must be replaced at the same
time.
Fig. 25
7. Replace the carbon brushes cover and
motor cover.
Carbon brush
Summary of Contents for UE-153DV1
Page 1: ......
Page 4: ... 2 Electrical Schematic ...
Page 16: ...Base Assembly 1040420 V6 14 ...