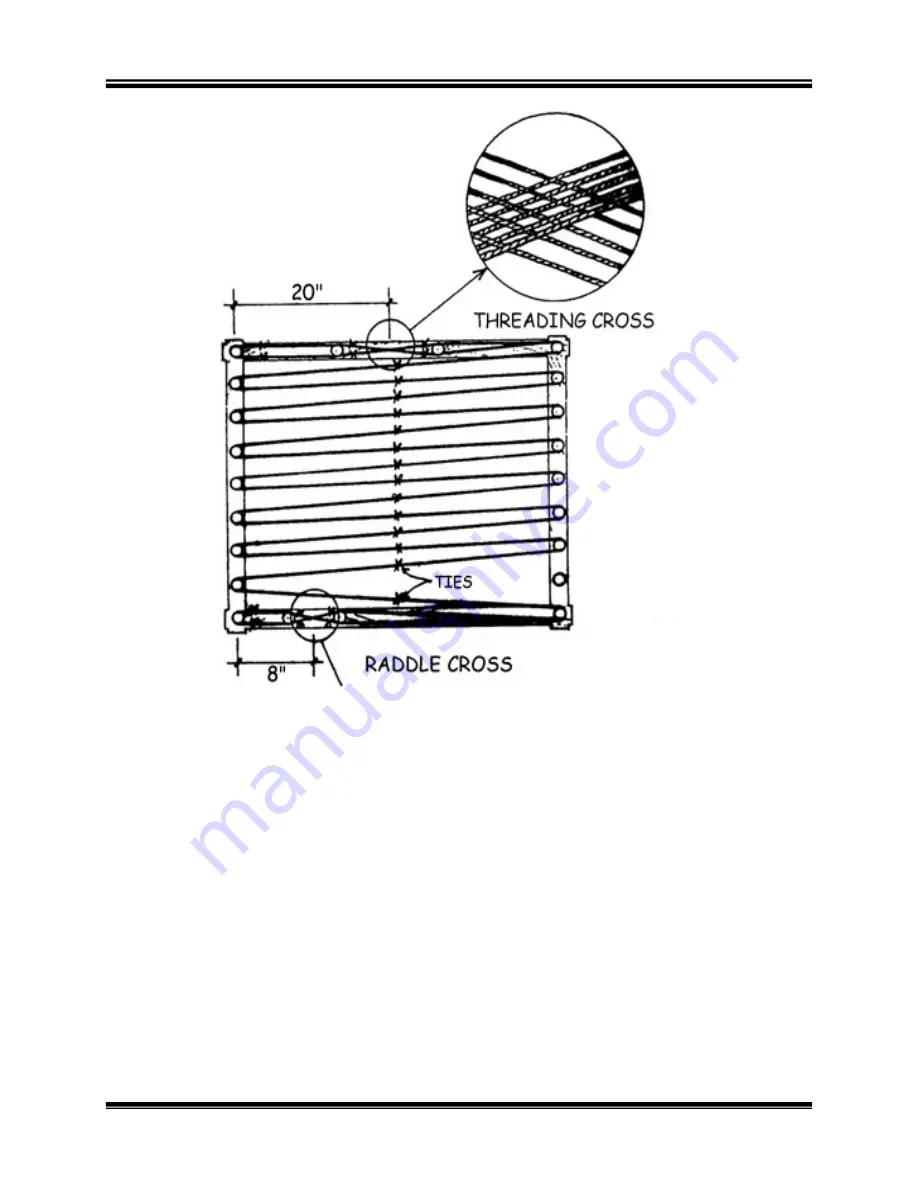
Using the WDL
Workshop Dobby Loom User’s Manual
Page | 40
Warping Section
Figure 40 - Warping Board with Two Crosses
Securing the Crosses
Before removing the warp from the board or the reel, secure the crosses.
Use four ties to secure each cross. These ties go on each side of both pegs
holding the cross.
It is usually a good idea to use different color threads for the ties on the tops
of the pegs and another color to tie the bows underneath the pegs. By color
coding your ties, you are less likely to twist the warp later.
Removing the Warp for the Warping Boards
Remove the warp from the warping board by chaining or by winding on the
kitestick. Start from the threading cross and proceed to the raddle cross.
Since the capacity of the warping board is limited, for wide warps you will
end up making a number of mini-warps and taking them off individually.