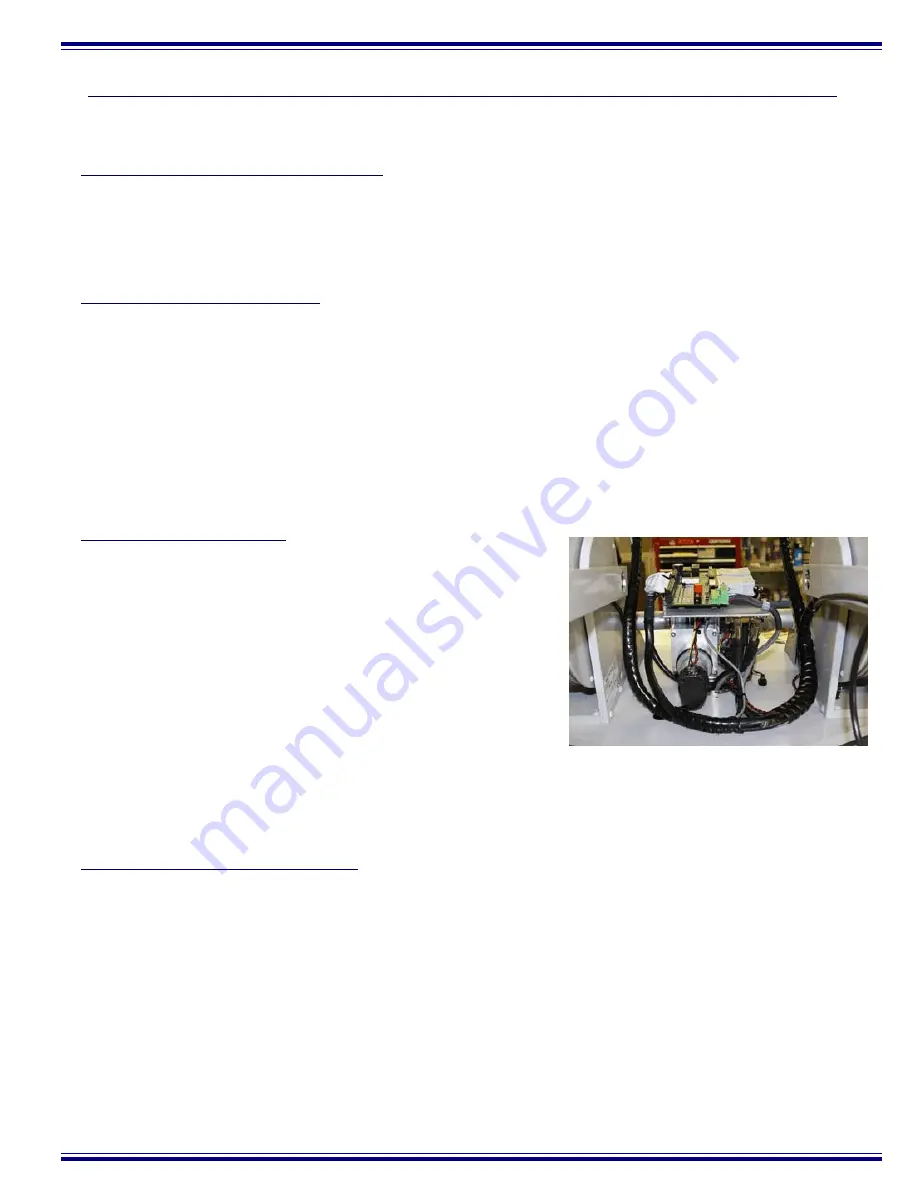
Model 1278K Mobile VSAT Antenna System
13
Operation and Maintenance Manual
SECTION 4 — ELEVATION POSITIONING SYSTEM
4.1 ELEVATION PIVOT ASSEMBLY
The elevation pivot assembly consists of two elevation drum assemblies pivoting between two clevis blades
assemblies. The drum shafts pivot in hi-tech plastic bushings. No maintenance is required. If squeaking
noise is heard, simply spray silicone lubricant with “straw” nozzle down between the drum side and clevis
plate on to the pivot shaft.
4.2 ELEVATION GEAR BOX
The elevation gearbox is a low backlash (30’) worm gear box. The worm gear drive isolates any backlash
in the motor drive from the system. In addition, since it is a 40:1 ratio it will not back drive, eliminating any
need for a brake on the drive train.
The motor drives the input worm via a quill/female hole and square key. The worm shaft is extended with a
hex shape adapter for the hand crank. The dual elevation capstans are driven with a square key and
clamped to the gearbox shaft to eliminate backlash.
The gearbox contains synthetic oil filled half way to the level plugs. Because of the design capacity of the
gearbox, low rpm and limited cycles, no maintenance is required.
4.3 ELEVATION MOTOR
The elevation drive motor is a 24V DC motor with integral 32:1
spur gear train. The motor armature rotates at up to 3300 rpm
causing a high frequency noise that will vary depending of the
loading condition of the motor. (Fig. 4.1) An optical encoder is
mounted to other end of motor output shaft to provide real time
positional information to TracStar Systems controller.
The maximum output speed is 104 rpm. The output shaft is a
standard keyed shaft. The output torque capacity of the motor is
rated for the operational wind load.
Since the low backlash worm gear drive, isolates the backlash
from the motor, any backlash between the square key and motor
gear train will not be seen by the reflector bore sight. No
maintenance of elevation motor is required.
4.4 ELEVATION AvL CABLE DRIVE
The patented elevation AvL cable drive produces a zero backlash, high stiffness, no wear, no lubrication,
and drive system with maximum reliability. The system consists of 12 1/16, 7x19 stainless steel aircraft
control cables reverse wrapped three times around the capstan with solid connections on one end and
high force, Belleville springs on the other end. Eight cables have the capacity to withstand a 75 mph wind
load. The additional cables are used to provided increased stiffness and drive redundancy
. If a cable
becomes damaged during usage, cut off cable and continue to use positioner. Replace cable
when time permits at your maintenance facility.
The cables are sized to last the life of the positioner. The springs will automatically compensate for any
elongation of the cable.
Figure 4.1