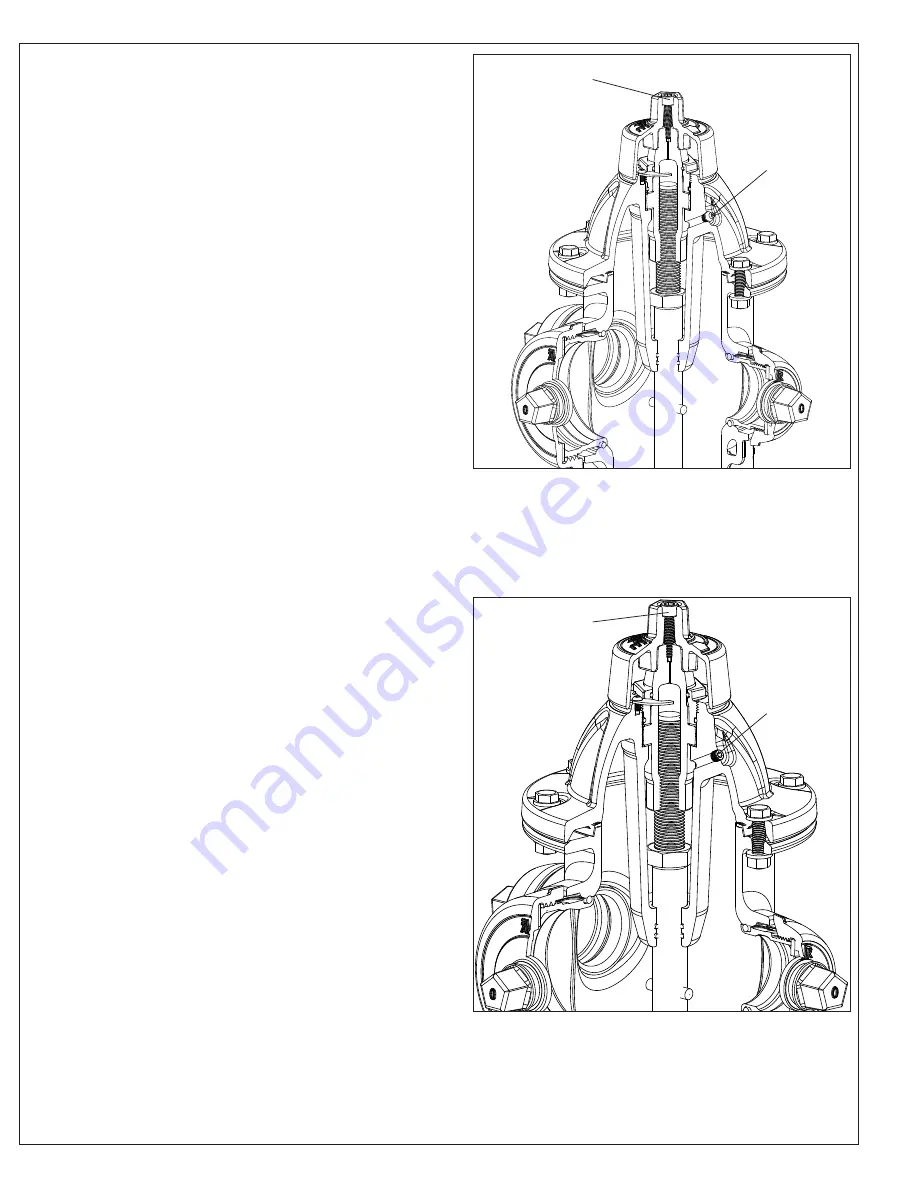
F1
F55
page 9
MAINTENANCE PROCEDURES
The American AVK Series 2780 Dry Barrel Hydrant is designed
to be a trouble free, easy to maintain hydrant. The following steps
are recommended to provide trouble free operation.
GREASE LUBRICATION
(Fig. 4A)
WARNING:
On a partially disassembled hydrant under line
pressure, pressing down on the stem could force open the Main
Valve (F61) and allow it to slam shut, creating a water hammer.
To prevent this during routine maintenance, first locate and be
sure the supply valve is closed. Relieve the pressure on the
Main Valve (F61) by momentarily opening and then closing the
hydrant. Reopen the supply valve after the hydrant has been
reassembled.
GREASE SERVICING FOR BONNETS WITH ZERK FITTINGS,
(Fig. 4A
)
CAUTION
: For grease servicing, ensure that the Weathershield
bolt has been loosened to prevent damage to the internal
O-rings.
1. Refilling is performed by loosening the Weathershield bolt
(F1) with a 5/16” or (8mm) hexagon key.
2. Refill lubricant reservoir with a food grade grease using a
Grease gun on the Zerk Fitting (F75).
3. Tighten the Weathershield Bolt.
OIL LUBRICATION
(Fig. 5A)
WARNING:
On a partially disassembled hydrant under line
pressure, pressing down on the stem could force open the Main
Valve (F61) and allow it to slam shut, creating a water hammer.
To prevent this during routine maintenance, first locate and be
sure the supply valve is closed. Relieve the pressure on the
Main Valve (F61) by momentarily opening and then closing the
hydrant. Reopen the supply valve after the hydrant has been
reassembled.
OIL SERVICING FOR BONNETS WITH BRASS PLUG,
FIGURE 5A
1. Loosen the Weathershield bolt (F1) with a or 5/16”,(8mm)
hexagon key. This will allow the oil reservoir to breath and be
filled faster.
2. Remove the Brass Plug (F55) with a 3/16” hexagon key.
Refill the oil reservoir with FDA approved food grade oil.
3. Install the Brass Plug and tighten the Weathershield Bolt.
This should be done after any repairs or as required by local
specifications.
Fig. 4A
Grease lubrication for bonnets
with zerk fittings
F1
F75
Fig. 5A
Oil lubrication for bonnets
with brass plug
Summary of Contents for 2700 SERIES
Page 7: ...page 6 Fig 2 Internal Drain Plugging F55 F51 ...
Page 27: ...page 26 ...