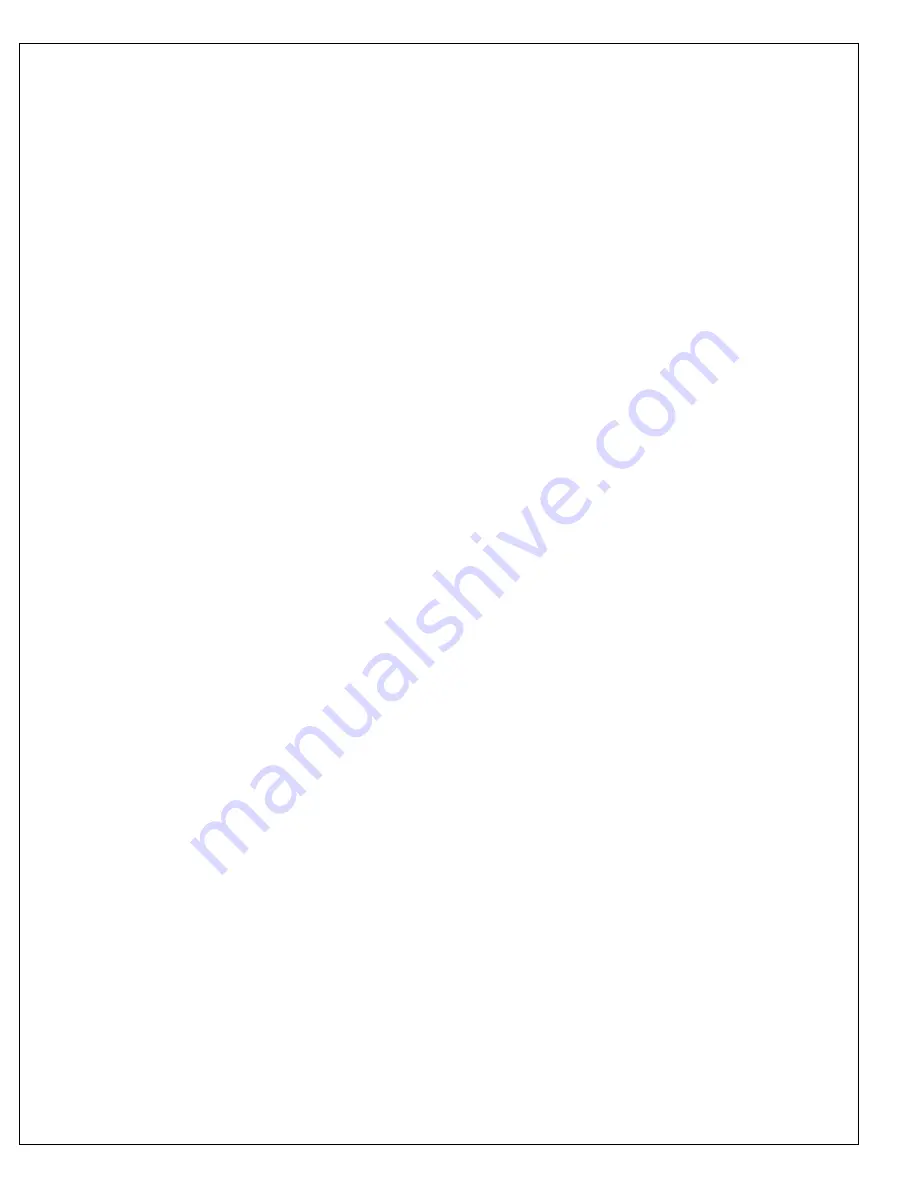
page 15
TROUBLESHOOTING GUIDE
PROBLEM: Hydrant leaking from around nozzle.
Probable Cause:
Damaged valve disc or nozzle sealing surface.
Corrective action:
Inspect valve disc and nozzle sealing surfaces and replace if necessary.
PROBLEM: Hydrant leaking from around stem nut.
Probable Cause:
Damaged stem o-rings.
Corrective action:
Replace stem o-rings.
PROBLEM: Nozzle section facing the wrong direction.
Corrective action:
Loosen the Nozzle Section hardware and carefully rotate the Nozzle Section to the desired
position. Tighten the mounting hardware to 60 Ft. Lbs..
PROBLEM: Hydrant flow is low.
Probable Cause:
Hydrant or supply vale is not fully open.
Corrective action:
Verify that the hydrant is fully open. The AVK Series 24 hydrant valve discs are fully opened
in approximately 9-14 turns.
Also locate and verify that the supply valve is fully open.
Summary of Contents for 2472
Page 19: ...page 18 ...