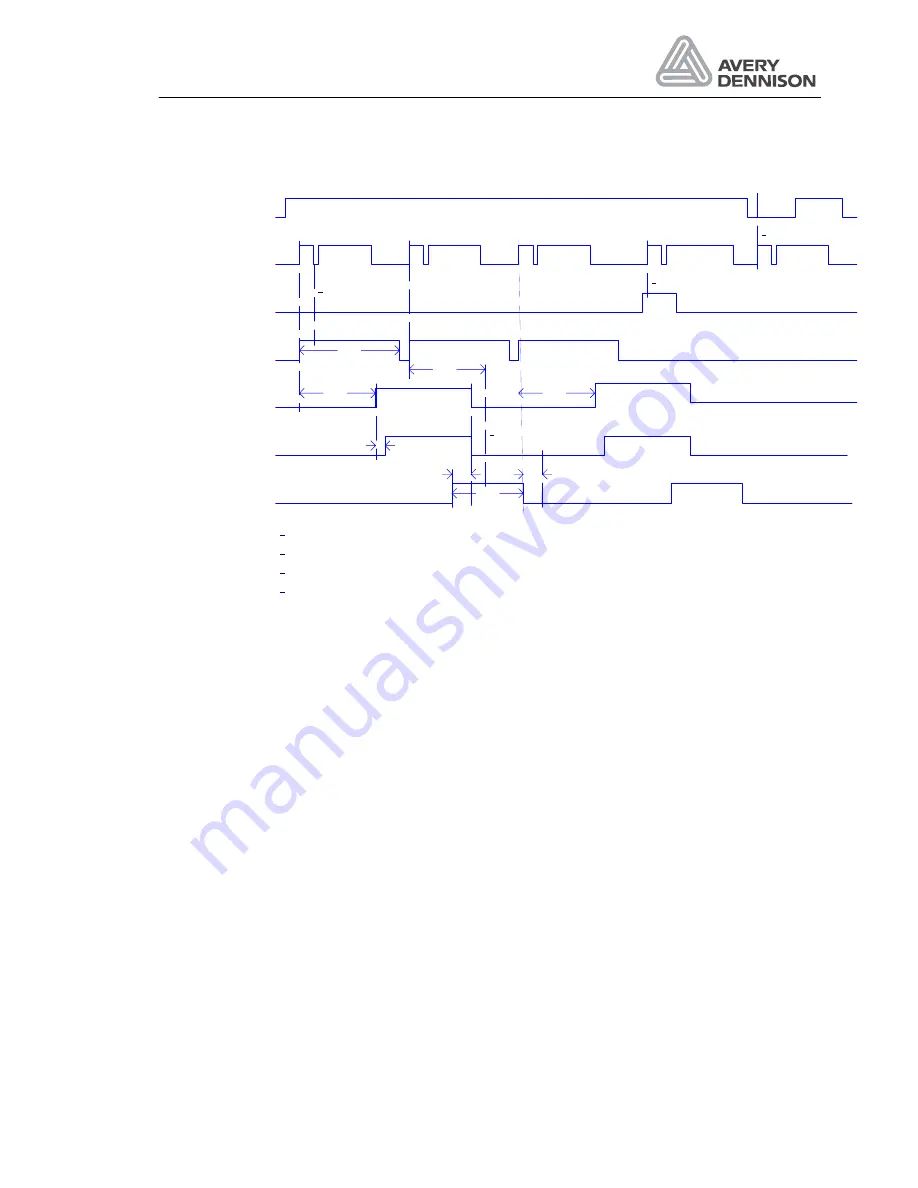
Operators Manual
ALS 341
Release 4/04
Page 39
Electrical connections
Productstart
Dispense
Dispensing edge
Output CN10 / 8
POS
Product Output
PRDL
APOS
CN10 / 6
CN6 / 19
Printer Output
CN10 / 10
PDT
Ready
Inhibit
PDWT
POS
POS
1
2
4
1
2
3
Missing Label: New start of dispense during printer activ
Inhibit activ
Machine not ready. Errorcondition or not online
3
4
Productstart disabled. PRDL activ
PHT
Figure 19 Timing diagram
6.7
EMI
To protect the machines against electrical noise and to protect production of electrical noise
you have to follow these rules:
Rule 1
All metallic parts must have a good and plane contact (no lacquer, aluminium oxide is an
isolator). Use scratch washers.
Rule 2
A signal line (Data-, communication- and control cable) has to separate to power cables. The
minimum distance is 50 cm (20 cm inside a cabinet).
Rule 3
All signal lines should be lead in the machine or cabinet only on one side.
Rule 4
Unshielded cables must be twisted (both poles).
Summary of Contents for ALS 341
Page 1: ...ALS 341 User Manual Covering the World Part number 0089999 10 Release 4 04...
Page 2: ......
Page 11: ...Operators Manual ALS 341 Release 4 04 Page 7...
Page 12: ......
Page 34: ......
Page 46: ...Operators Manual ALS 341 Release 4 04 Page 42 Maintenance Figure 20 Rewind adjustment...
Page 50: ...10 CE Declarations...