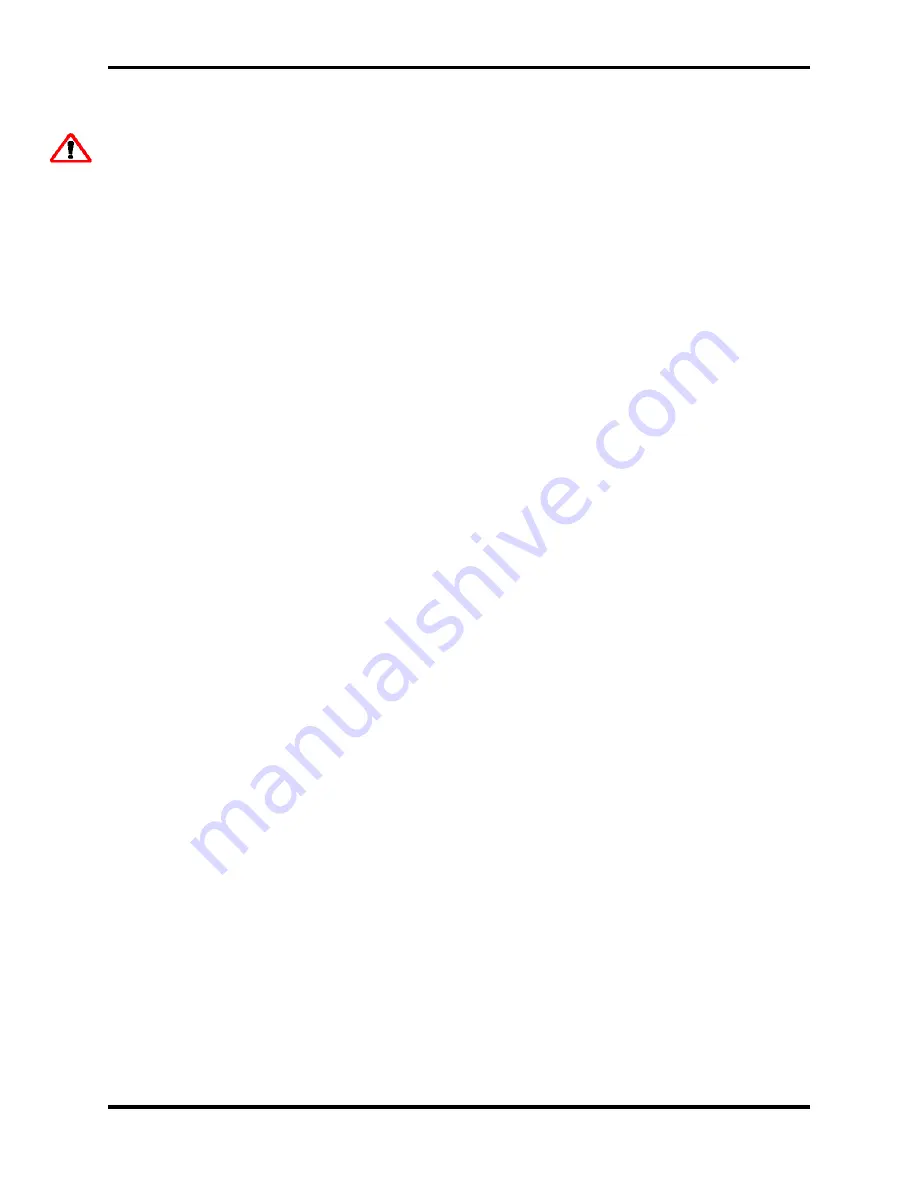
Page 2
Installation and General Maintenance Recommendations
WARNING: INSTALLATION
and MOUNTING
The user of these devices must conform to all applicable
electrical, mechanical, piping and other codes in the installation,
operation or repair of these devices.
INSTALLATION! Do not attempt to install, operate or repair this
device without proper training in the technique of working on
pneumatic or hydraulic systems and devices, unless under
trained supervision.
Compressed air and hydraulic systems contain high levels of
stored energy. Do not attempt to connect, disconnect or repair
these products when a system is under pressure. Always
exhaust or drain the pressure from a system before performing
any service work. Failure to do so can result in serious personal
injury.
MOUNTING! Device should be mounted and positioned in such
a manner that it cannot be accidentally operated.
INSTALLATION and GENERAL
MAINTENANCE RECOMMENDATIONS
Operation
When the cylinder installation is completed correctly, air pressure
delivered from the directional control valve to the port on the cap
end of cylinder will extend the piston rod. A shift of the valve to
exhaust that air and apply air pressure to the port on the head end
will retract the piston rod.
Adjustments
No adjustments are required after the cylinder is installed and
properly aligned.
Maintenance
It is recommended that this cylinder be completely disassembled
approximately every five years for cleaning, inspection, and
replacement of all rubber parts. The first examination on this
particular application will determine if the period between service
should be extended or shortened.
Disassembly –
Use care not to destroy or scratch any parts
during this procedure.
1. Remove the rod eye (14) from the piston rod (12).
2. With the cylinder lying horizontal on the floor, loosen and
remove the four stop nuts (19).
3. Using a mallet, tap the cap (1) away from the tube (2) and
remove the tube seal “O” ring (10).
4. Hold the end of the piston rod (12) and using the mallet, tap
the head (3) carefully away from the tube (2) just far enough to
allow your hand to reach between the head and tube to grab
and support the piston rod. Now continue to tap the head off of
the rod.
5. Pull the piston rod upright to a vertical position and then pull
the tube (2) off of the piston rod assembly.
6. Clamp the piston rod in a vise, protecting the rod’s surface,
and remove the piston (13) from the piston rod (12) by
loosening the threaded joint (via spanner wrench) and slide
the piston off of the rod.
7. Remove the piston “O” ring (11), two piston seals (7), back-up
rings (8) and wear strip (9) .
8. Remove from the head (3) the tube seal “O” ring (10), the rod
wiper (4) and the rod seal (5) and back-up ring (6).
Cleaning & Inspection
1. Clean all metal parts with a non-flammable solvent and wash
all elastomer or rubber parts with soap and water. Rinse
everything thoroughly and blow them dry with a low pressure
air jet.
2. Inspect all parts and throw away all those that are to be
replaced due to damage, wear or age. Give particular attention
to the recommended replacement parts as indicated on the
parts list.
REASSEMBLY
– Use the exploded view as a guide and lubricate
all seals and grooves with Shell Oil Company’s Aeroshell Grease
14.
1. Assemble the rod seal (5) into the head (3), making sure the
concave side of the seal faces the inside of the cylinder. Place
back-up ring (6) against the flat face of the seal.
2. Install the rod wiper (4) in the head (3) with the sharp edge
facing the outside.
3. Clamp the piston rod (12) in a vise, install the piston “O” ring
(11) and slide the piston (13) onto the rod. Fasten the piston
into place using a torque wrench and tighten to 250 ft-lbs using
Loctite 277.
4. Install piston seals (7) onto the piston (13) with the flat side of
the seals facing the middle of the piston. Place back-up rings
(8) against the flat side of the piston seals (7). Install wear strip
(9) onto the piston (13).
5. Set the piston rod assembly on end, protecting the rod’s
surface. Slide the head (3) down over the piston rod (12),
being careful not to cut or damage the wiper (4) or rod seal (5).
6. Lay the piston rod over towards its side and push it through
the head until the piston is about four inches from the head.
7. Set the tube (2) on end and wipe some grease on the inside at
the very top.
8. Insert the tube seal “O” rings (10) into the head (3) and the cap
(1).
9. Fit the greased end of the tube on to the piston. Carefully run a
screwdriver around the first seal to assist the entry into the
tube. Push the tube forward until it enters the groove in the
head (3).
10. Install the cap (1) onto the tube, sliding the tie rods through the
holes of the cap.
11. Replace the stop nuts (19) onto the tie rods (17 & 18) and
using a torque wrench, alternately torque on opposite sides to
40 ft-lbs. DO NOT tighten one side first.
12. Torque rod eye onto the piston rod (12) to 200 ft-lbs using
Loctite 277 until it shoulders.
13. The reassembly is complete, therefore test the cylinder for
correct operation and any evidence of leakage. DO NOT
exceed 150 PSIG air pressure.