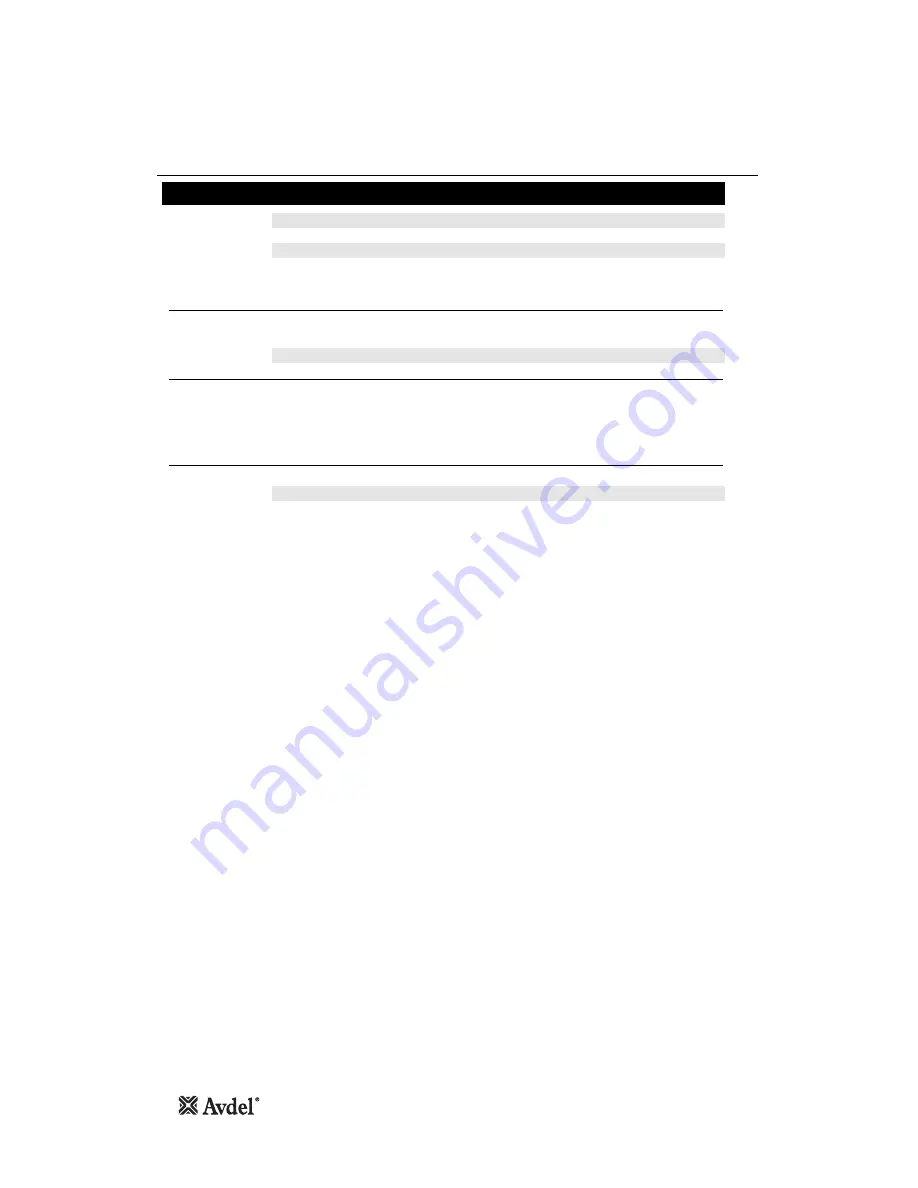
S y m p t o m , P o s s i b l e C a u s e a n d R e m e d y
24
F a u l t D i a g n o s i s
S Y M P T O M
P O S S I B L E C A U S E
R E M E D Y
PA G E R E F
Tool does not spin
Insufficient gap between Lock Nut 30
Adjust gap to between 1.5mm and 2mm
-
on
and Spindle 43
Pushrod 5 too short
Replace
-
Air motor jammed
Lubricate tool at air inlet. If insufficient
-
dismantle & clean air motor thoroughly
Trigger
Static friction
Depress trigger a few times
-
inoperative
Low air pressure
Increase air pressure
-
Drive screw does not
Lip Seal 25 is defective
Replace
-
return and/or keeps
spinning off
Tool does not spin
Adaptor Nut 44 loose
Tighten
-
off
No air supply
Connect
-
Air motor jammed
Lubricate tool at air inlet. If insufficient
-
dismantle & clean air motor thoroughly
Summary of Contents for 74405
Page 1: ...Hydro Pneumatic Power Tool 74405 Instruction Manual Original Instruction ...
Page 2: ......
Page 25: ...25 Notes ...
Page 26: ...26 Notes ...