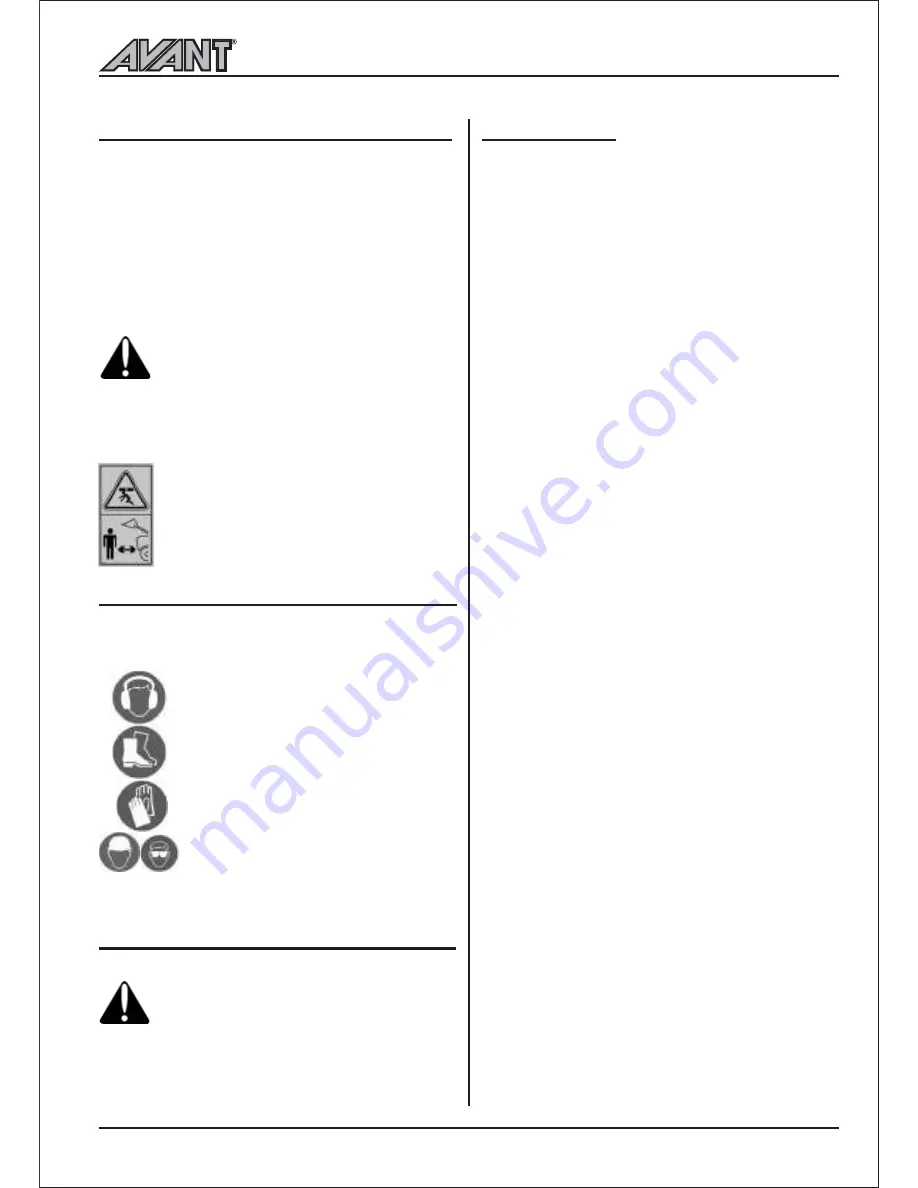
Safety instructions
5
Handling of heavy loads and load sensor
The loader is equipped with a load sensor system. It
gives an audible warning signal and at the same time
an indicator lights in the dashboard when there is a risk
that the machine tips over its front axle. When the
system gives a warning signal the load that is being lifted
is too heavy in relation with the lift capacity of the
loader. In this case one has to either put more counterweights
on the loader or relieve the load that is being lifted.
When the load sensor starts to warn, there is
a risk that the machine tips over its front axle.
In this case stop lifting of the boom, retract
the telescopic boom and lower down the boom
slowly. When the load sensor is warning do
not steer the machine before the boom is
lowered down close to ground level. Lift the
boom only when the loader chassis is straight.
Keep the load as close to ground as possible.
Never take a heavy load on the loader from
high level e.g. from truck, shelf etc. risk
of tipping over!
Always put the load down on the ground before
leaving the machine. When loading, always
keep the loader chassis as straight as possible.
Personal safety and protective equipment
Wear safe clothing and personal protective equipment
(PPE). Protect yourself against work hazards like noise,
ejecting debris or dust for example.
Noise level at drivers seat can exceed
85 dB(A). Wear hearing protection
when working with the loader.
It is recommended to wear safety
footwear when working with the loader.
Wear protective gloves when handling
hydraulic hoses.
Follow regulations regarding
protective equipment. Wear eye
protection and hard hat or other
protective equipment as needed.
Read Operators Manual of the attachment for more information
about protective equipment needed in the work.
Safety frame (ROPS) and safety canopy (FOPS)
Safety frame (ROPS) protects the operator
in case the machine tips over. Always fasten
the seat belt in order to stay inside the safety
frame protective area. Never take off the
safety frame.
When working in conditions where falling objects may
be a risk (on building sites etc.), the loader must be
equipped with a falling objects protective canopy
(FOPS), part no. A48905.
Electric system
Lead acid batteries can produce flammable and
explosive gases. Make sure that the ventilation is
sufficient and keep arcs, sparks, flames and lighted
tobacco away from battery.
Battery acid causes severe burns. In case of acid
contact, wash immediately with water for several
minutes and get medical attention in case of eye
contact.
Read the instructions for jump start on page 30.
Never charge a frozen battery.
700 Series
https://tractormanualz.com