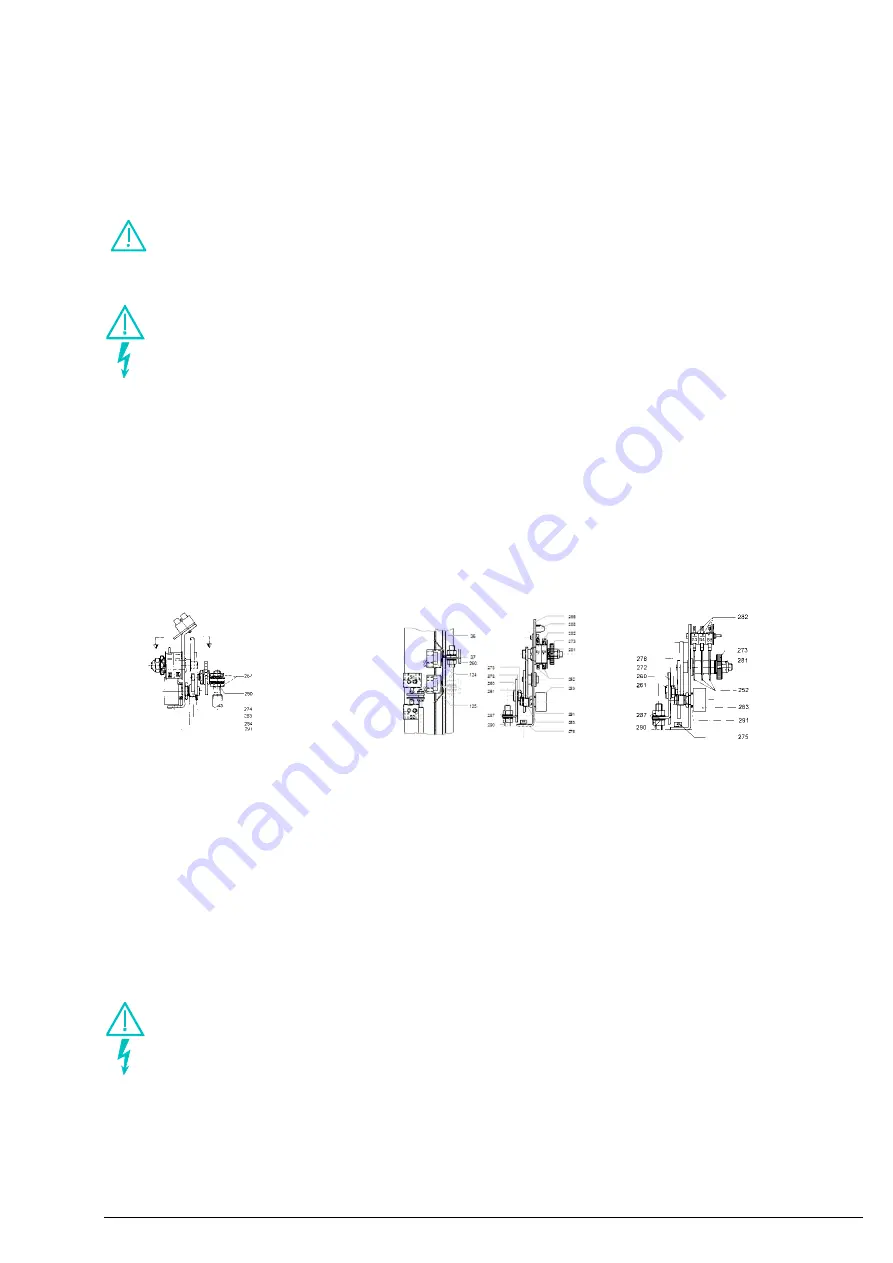
AUMA Industry & Marine GmbH, 08.2018
MON_SBA06-200_DE_EN_rev01.docx
Seite/page 7/8
After connection but prior to applying the voltage, observe the <Commissioning> chapter.
Carry out mains connection only with power supply switched off! Safeguard against unintentional switching on.
For installing electric lines and the mains connection the regulations for the installation of power systems and
equipment, as well as the provisions of the local Electricity Board must be observed!
Check the mains connection voltage and frequency for conformity on the name plate of the linear actuator and also
the name plate of the driving motor.
The conductor cross section must always be laid out according to the respective power consumption of the linear
actuator and the required length of the line. Minimum cross section of the conductor for this type of linear actuator:
1 mm²
In case of a fault: Hazardous voltage while protective earth conductor is NOT connected! Electric shock possible.
Start running the device only after having connected the protective earth conductor.
Short-circuit due to pinching of cables! Electric shock and functional failures possible.
5.1 Cable
connection
Hazardous voltage! Electric shock possible.
Disconnect device from the mains before lifting hood.
On principle the wiring diagram enclosed or glued into the hood is applicable.
Replace blanking plug by suitable cable glands.
1. Remove cable sheathing.
2. Strip wires.
3. For flexible cables: Use end sleeves according to DIN 46228.
4. Connect cables according to order-related wiring diagram.
The enclosure protection IP... stated on the name plate is only ensured if suitable cable glands are used.
6. Commissioning
The thrust of the actuator and set of travel has to be compared with the valve data. Overstressing can cause serious
damage to the valve.
Pay attention to moving parts during the mounting and adjustment. There exists the danger of being injured and the
risk of essential material damages.
6.1
Setup of the limit switching
By default the actuator is switches off in the end positions by force using DE switches. Are also limit switches used for
stopping in end position, the preset stroke can be read on the nameplate.
SBA06
SBA12-20-45
SBA80-200
Figure 6.1-1: Position of the limit switches
6.2 Test
run
6.2.1 Check direction of rotation
Move actuator manually to intermediate position or to sufficient distance from end position.
Switch on actuator in running direction CLOSE and observe the direction of rotation.
If the direction of rotation is wrong, switch off immediately.
Check wiring (bridges). Correct phase sequence in case of 3~phase power supply.
Repeat test run.
Valve damage due to incorrect direction of rotation due to non-functioning of end switches when rotation is wrong.
6.2.2 Check limit switching
In case of wiring of switches is not done factory-made, the switching off in end position has to be checked:
The linear actuator without hood may be short-term-operated only during test run respectively for
indispensible adjusting works on electrical options such as potentiometer, travel switch or electronic
positioner.
During this activity there exists access to dangerous live, blank, moving and rotating parts. In case of
inappropriate or incautious execution of the adjusting works can cause death, severe physical injuries or
essential material damages.
The operation of the linear actuator without hood is interdicted for a purpose different to what has been
described as mentioned before.
Actuate the switching rollers of the DE-switches and WE-switches with an insulated screw driver and check whether
the corresponding switches actually switch off the motor.
If necessary, interchange the inset motor feed bridges.