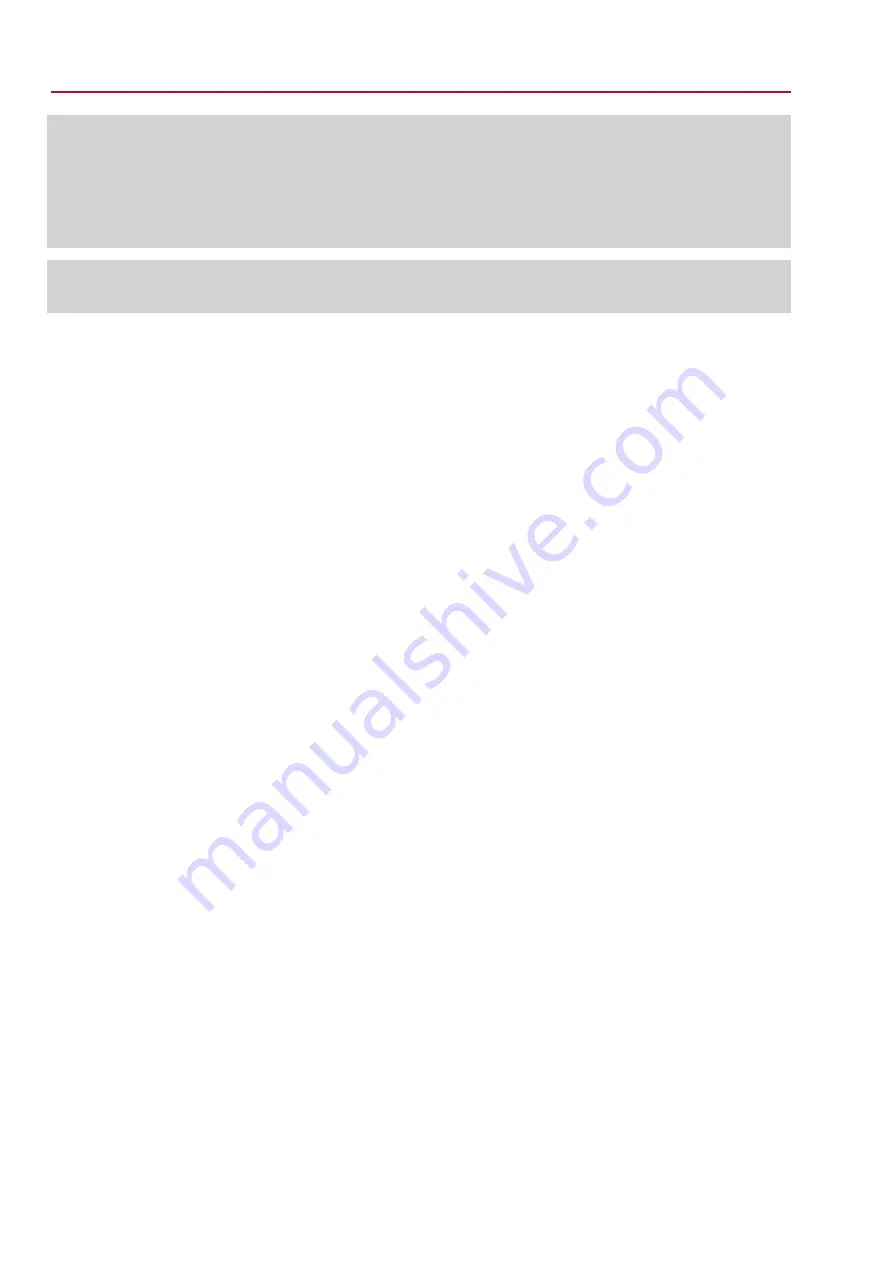
Read operation instructions first.
●
Observe safety instructions.
●
These operation instructions are part of the product.
●
Store operation instructions during product life.
●
Pass on instructions to any subsequent user or owner of the product.
Target group:
This document contains information for assembly, commissioning and maintenance staff.
Table of contents
Page
1.
Safety instructions.................................................................................................................
1.1.
Basic information on safety
1.2.
Range of application
1.3.
Warnings and notes
1.4.
References and symbols
2.
Identification...........................................................................................................................
2.1.
Name plate
2.2.
Short description
3.
Transport and storage...........................................................................................................
3.1.
Transport
3.2.
Storage
4.
Assembly................................................................................................................................
4.1.
Mounting position
4.2.
Handwheel fitting
4.3.
Multi-turn actuators for motor operation
4.3.1.
Mounting positions Multi-turn actuators with part-turn gearboxes
4.3.2.
Mount input mounting flange
4.4.
Mount gearbox to valve
4.4.1.
Overview on coupling variants
4.4.2.
Mount gearbox with coupling to valve
5.
Indications..............................................................................................................................
5.1.
Mechanical position indicator/running indication
6.
Commissioning......................................................................................................................
6.1.
End stops in gearbox
6.1.1.
Set end stop CLOSED (butterfly valves)
6.1.2.
Set end position OPEN (butterfly valves) or modify swing angle at gearbox
6.2.
Seating in end positions via multi-turn actuator
6.3.
Set mechanical position indicator
7.
Servicing and maintenance...................................................................................................
7.1.
Preventive measures for servicing and safe operation
7.2.
Maintenance intervals
7.3.
Disposal and recycling
8.
Technical data.........................................................................................................................
8.1.
Technical data Part-turn gearboxes
2
GS 315 – GS 500
Table of contents
GZ 30.1 – GZ 40.1