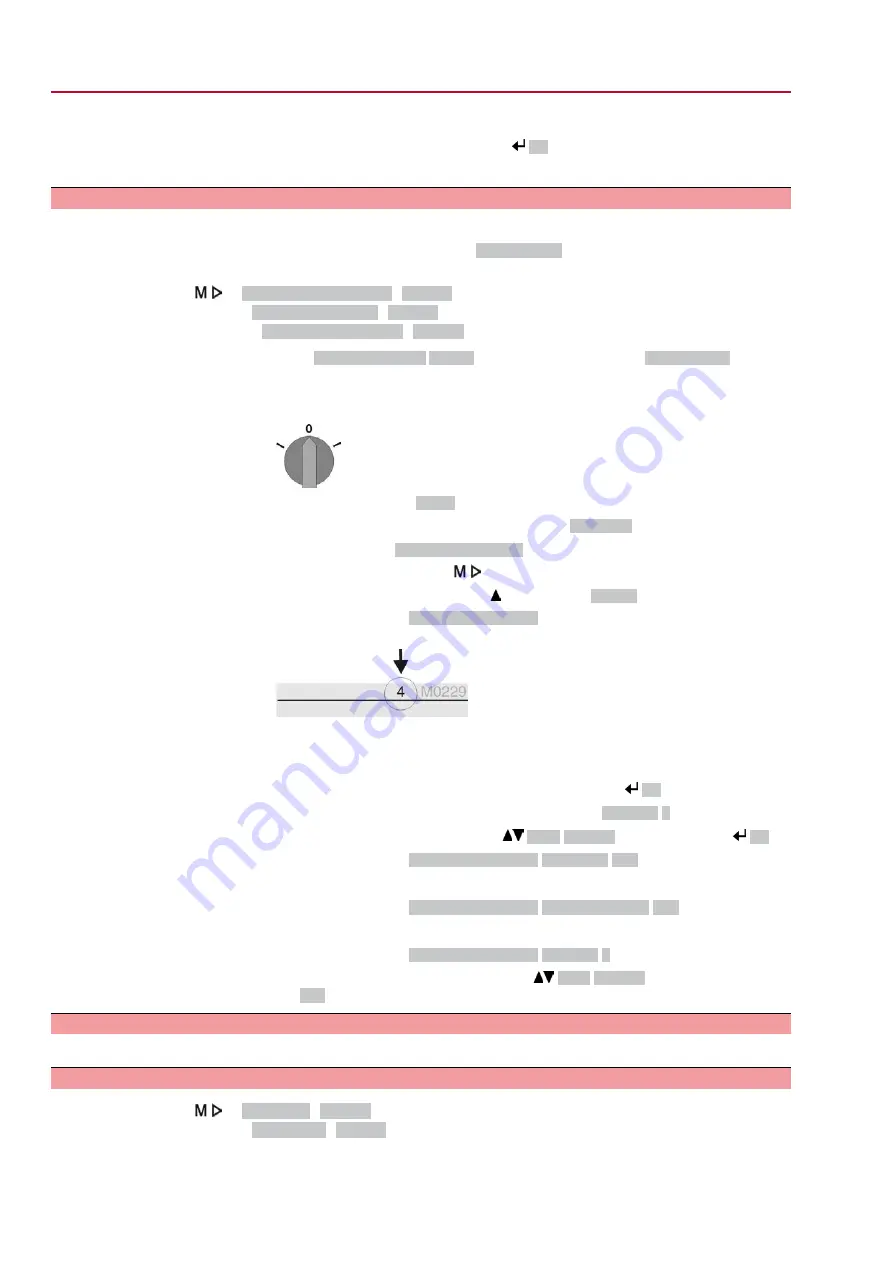
5.
Repeat steps 1 and 2 for all further digits.
➥
Having confirmed the last digit with
Ok
, access to all parameters within one
user level is possible if the password entry is correct.
6.4.2.
Password change
Only the passwords of same or lower access level may be changed.
Example: If the user is signed in as
Specialist (4)
, he/she can change passwords as
for password levels (1) through (4).
Device configuration M0053
Service functions M0222
Change passwords M0229
Menu item
Service functions M0222
is only visible, if user level
Specialist (4)
or higher
is selected.
Select main menu
1.
Set selector switch to position 0 (OFF).
2.
Press push button C
Setup
and hold it down for approx. 3 seconds.
➥
Display goes to main menu and indicates:
▶ Display...
Change passwords
3.
Select parameter
Change passwords
either:
→
click via the menu
to parameter, or
→
via direct display: press and enter ID
M0229
-
Display indicates:
▶ Change passwords
-
The user level is indicated in the top row (1 – 6), e.g.:
-
For user level 1 (view only), passwords cannot be changed. To change pass-
words, you must change to a higher user level. For this, enter a password via
a parameter.
4.
For a user level between 2 and 6: Press push button
Ok
.
➥
The display indicates the highest user level, e.g.:
For user 4
5.
Select user level via push buttons
Up ▲ Down ▼
and confirm with
Ok
.
➥
Display indicates:
▶ Change passwords Password 0***
6.
Enter current password (
→
enter password).
➥
Display indicates:
▶ Change passwords Password (new) 0***
7.
Enter new password (
→
enter password).
➥
Display indicates:
▶ Change passwords For user 4
(example)
8.
Select next user level via push buttons
Up ▲ Down ▼
or cancel the process
via
Esc
.
6.5.
Language in the display
The AUMATIC actuator controls display is multilingual.
6.5.1.
Language change
Display... M0009
Language M0049
38
SQ 05.2 – SQ 14.2 / SQR 05.2 – SQR 14.2 Control unit - electromechanical
Operation
AC 01.2 Intrusive Modbus RTU