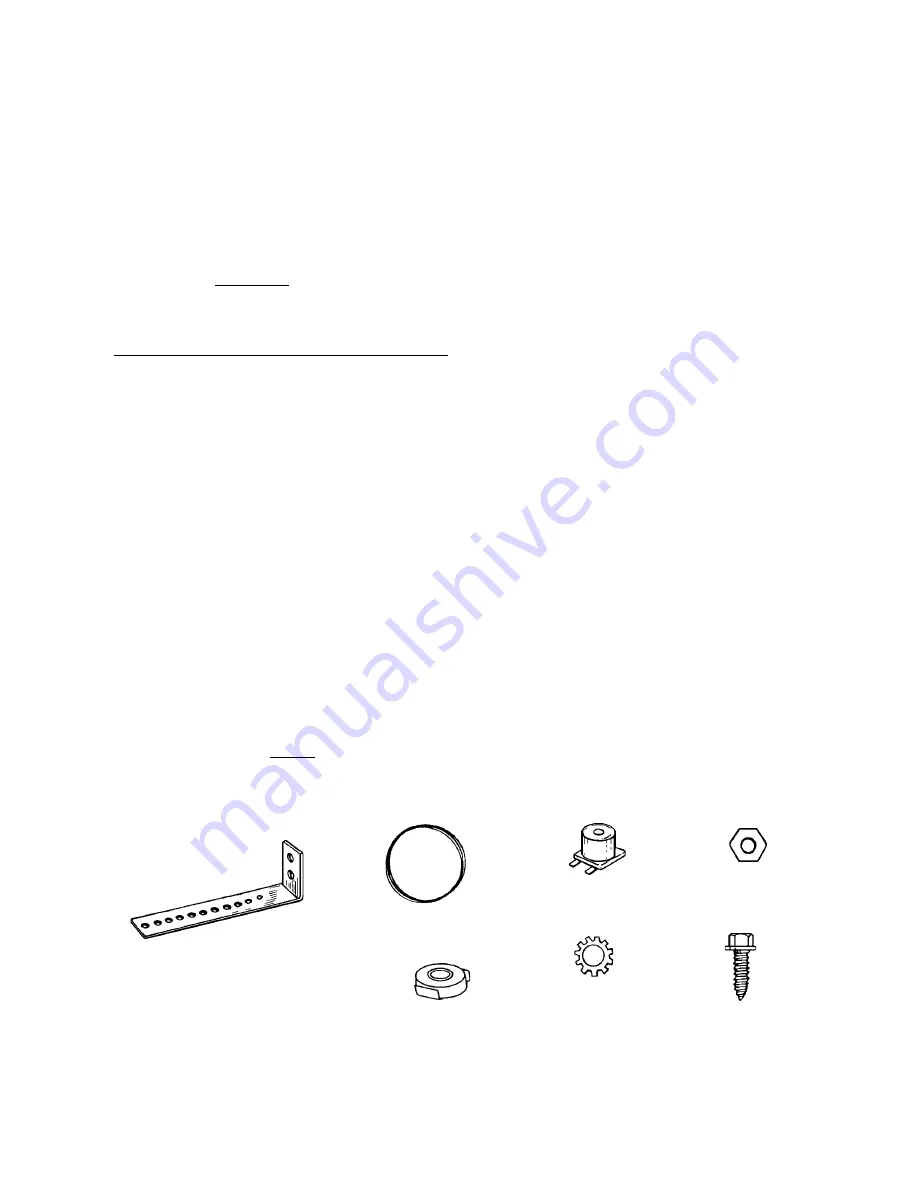
Step 6: While rotating the shaft, carefully snap one wire into one set of magnet slots. Loosely wrap the wire
to hold it in place. Snap the second wire into the remaining slots making sure the ends are nearly opposite
the first wire, as shown in Figure 4 or 11.
Step 7: Carefully pull wires tight, and twist with a pair of pliers, pulling down as you twist to avoid breaking
the wire. Now take the loose ends and wrap through the opposite wire, and twisting as above to remove any
excess slack, see Figure 4. This procedure will secure the magnets onto the drive shaft. The double-faced
tape is used to temporarily hold the magnets until the wire is attached.
Step 8: Spin the drive shaft by hand and check to ensure proper clearance. Remember that the drive shaft
position will change with the suspension. See Figures 3 or 8.
SPEED SENSOR COIL INSTALLATION
Step 9: Assemble the speed sensor coil and bracket with nut and lock washer. Use of mounting bracket will
be determined by the specific installation. Refer to Figures 5 or 10. In some cases installation may be easier
if the bracket is bent or cut to a specific shape.
Step 10: Determining the location for the speed sensor/bracket assembly: The speed sensor coil must be
pointing directly at the centerline of the shaft leaving a 3/8" (10 mm) clearance between the speed sensor coil
and the magnets. See Figures 8.
CAUTION: Before drilling any holes, make sure there are no parts which may be damaged on the other side
of the metal. Double check for any wiring harness which might be easily damaged by the drill bit.
Step 11: Use the bracket as a template to mark and center punch two hole locations. Drill two 3/16" diameter
holes. Mount the speed sensor/bracket assembly using two 1/4" x 3/4" sheet metal screws. Be sure bracket
is mounted securely so it will not vibrate during vehicle movement.
NOTICE: If the speed sensor coil is closer than 1/4", there is a possibility that the magnets will strike the coil.
If the coil is more than 1/2" from the magnets, the cruise control may not function properly.
NOTE: Make sure the black and gray wires are routed clear of any hot or moving parts as well, away from
electrical items such as spark plug wires or ignition systems. Interference from these sources could cause
the cruise control to surge.
WIRING:
Step 12: Route the black and gray paired wires to the speed sensor coil and attach to the terminals. (It does
not matter which way the wires are attached, i.e.polarity).
NOTE: This magnet kit cannot be used on Honda vehicles.
MAGNET KIT HARDWARE:
Stainless Steel Wire
6mm Hex Nut
Speed Sensor Coil
6mm Lockwasher
1/4" x 3/4"
Sheet Metal Screw
Speed Sensor Bracket
Magnet with Holder
-13-