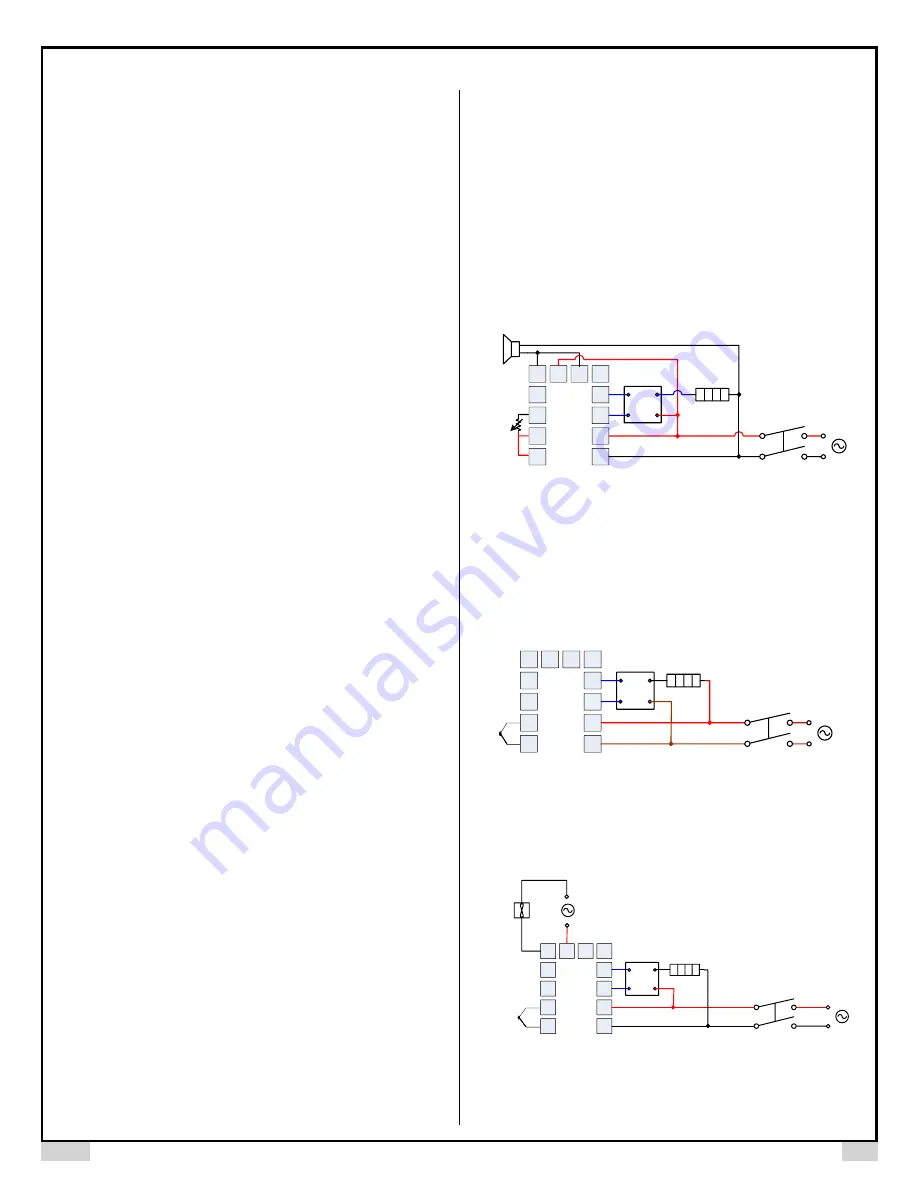
AUBER INSTRUMENTS
WWW.AUBERINS.COM
2020.06
P8/10
For example, a user wants to preheat a small oven from room temperature to
400˚F and maintain it for 10min before preceding to the next step; the acceptable
deviation is +/-
3˚F. So the program can be set as C01 = 400˚F, r01 = 2000, t01
= 10, SSB = 3. So the temperature to start t
he timer is 400˚F –
3˚F = 397˚F. After
the program is started, the controller will start bringing up the temperature with
paused
timer. Once the reading temperature reaches 397˚F, the controller will
start the soak timer t01 and counting down for 10 minutes.
6.2.6.
Program Run
When the program is running, the A-M indicator should be on. To start running a
program or resume a program that is on “hold”, press the
UP arrow (
▲
) key
once. The A-M indicator will be solid ON.
6.2.7.
Program Hold
“Hold” means the
program is being temporarily stopped. When the program is
on hold, the A-
M indicator will blink, the lower display window will flash “
hold
”
and set temperature. The controller will maintain at your current set temperature.
Two ways to hold the program manually:
1) Press and hold the UP arrow (
▲
) key for 2 seconds until the lower window
shows "
hold
".
2) Change parameter RUN = 2 (see note 5.3.20)
Please note, you cannot program the step to hold it for indefinite time. An
alternative solution is, you can set the soak timer to a large number like 9999.
Then you can manually jump to the next step. See section 6.2.9 for how to
manually jump steps.
6.2.8.
Program Stop
When a program is stopped, the output is turned off. The lower display window
will show “
stop
”, a
nd the A-M indicator is off. To stop the program manually,
change parameter RUN to 1. But the step will not go back to step segment 1
automatically. You can use Pro parameter for manually jump, or use display
mode 5 to manually jump. When all the program steps have been completed and
if program loop is disabled (LOOP = 0), RUN parameter will be automatically
changed to 1.
6.2.9.
Program Jump
To jump the program from the current step to step x, press and hold A/M key for
3s. Bottom display will show letter
“
P
”
. Press up and down arrow keys to change
the step number you want to jump to, then press and hold A/M key for about 3s
to save and jump.
6.2.10.
First Step & Last Step
For the first step, please set r01(step 1 ramp timer) as 2000, t01 as 0 and C01
as your ambient temp (like 80F).
For the last step, assuming step n is your last step, please set r[n+1] as 0 so the
controller will know step n is your last step. If LOOP = 0 (no looping), the
controller will stop the output. The lower display window will
show “
stop
”, and
the A-M indicator is off. If LOOP = 1 (looping is enabled), the controller will run
from step 1 automatically.
6.2.11.
Check the Step Number and Jump the Program
To check at which step the program is running, press the SET key once. The
upper wi
ndow will show “
StEP
” and the lower window will show the step
number. Press SET key again, the controller will show the set time for the current
step in the upper window, and show the running time in the current step in the
lower window. Press the SET key twice to return to the normal operating mode.
If no key is pressed in 10 seconds, it will automatically return to the normal
operating mode. While checking the step number or time, the step number or
time will be updated as the program executes.
To manually jump to another step in the program, press the SET key once to
show the step number in the lower window, then press the UP arrow (
▲
) or
DOWN arrow (
▲
) key to change the step number, and press the SET key to
confirm the change. The program will be jumped to the specified step
immediately. The controller will show the step set time for the new step in the
upper window. And the running time in the lower window will be cleared to 0. If
the step number is not changed, press SET key won’t affect the execution
of the
current step, but the display window will show step set time and running time.
This is a convenient feature when you want to skip the current step and manually
jump to another step. For example, if you want to jump to step 5 while the
program is running, press SET key to check the step number, then change the
step number to 5, and then press SET key to confirm.
7.
Wiring Examples
7.1.
Controlling heater by SSR
SSR
N
1 13 14 6
2
3
4
5
7
8
9
10
L
120V AC
Heater
SYL-5352P
120VAC buzzer
3
4
2
1
+
-
R
R
W
R
TD
Figure 6. SYL-5352P with RTD input. This is a typical wiring for controlling the
temperature of a tank of liquid with high precision.
The RTD sensor can offer accuracy within a fraction of a degree. The SSR allows
the heater to be switched at higher frequency for better stability. It also has longer
life time than the electromechanical relay. A proper heat sink is needed when
the SSR switches > 8A of current. For wiring a 240V heater, please see 5.2. AL1
and AL2 alarm relay outputs are connected to one same 110V buzzer.
7.2.
Controlling the load via SSR, 240VAC power.
TC
+
-
SSR
L2
1 13 14 6
2
3
4
5
7
8
9
10
L1
240VAC
Heater
SYL-5352P
3
4
2
1
+
-
Figure 7. This is essentially the same wiring example as 7.1, except the heater
and controller are powered by 240V AC and the temperature sensor is a
thermocouple. Alarms are not installed in this example.
7.3.
Heating and cooling with the same controller
SSR
N
1 13 14 6
2
3
4
5
7
8
9
10
L
120VAC
Heater
SYL-5352P
3
4
2
1
+
-
TC
+
-
120VAC
L
N
Cooling
Fan
Figure 8. Control a heating element and a cooling fan using SYL-5352P.