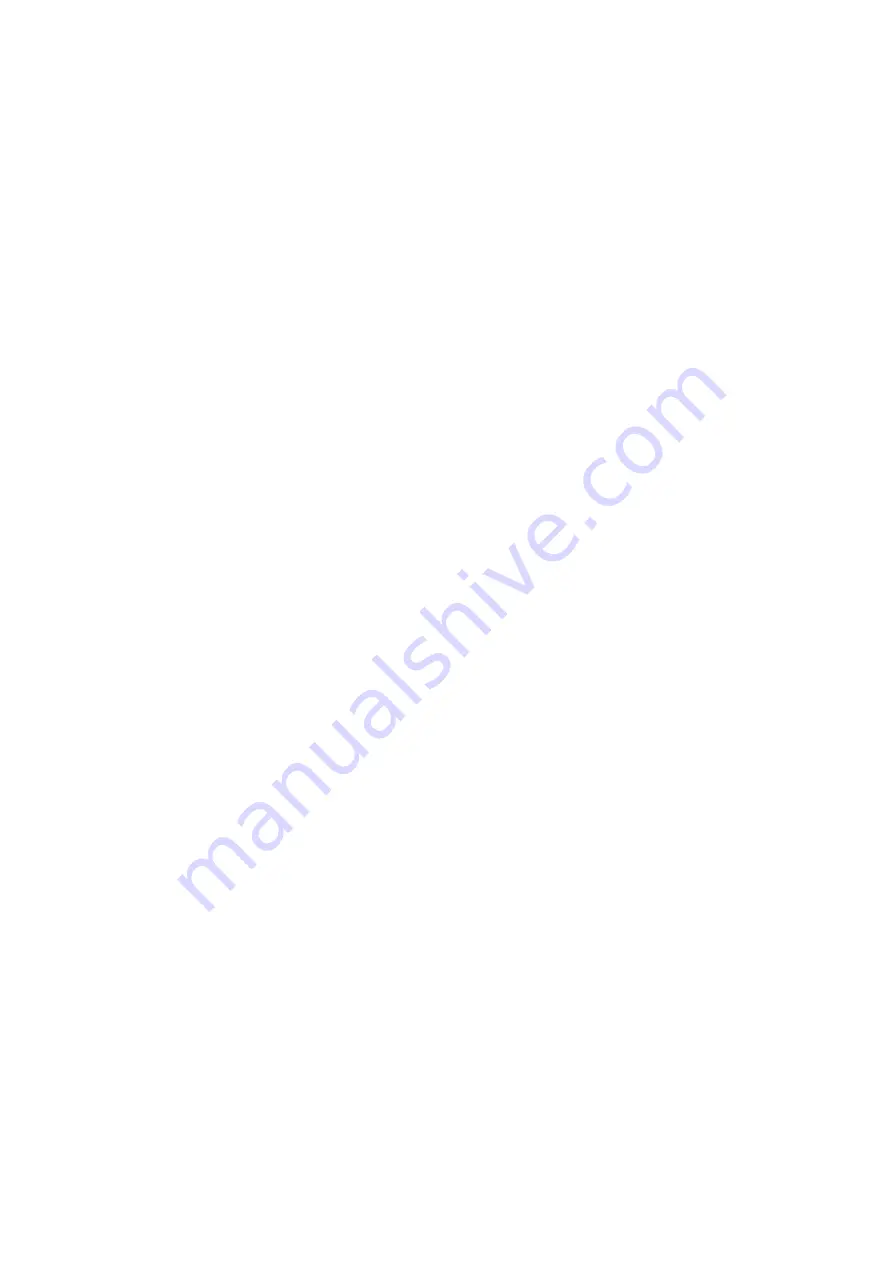
10
Atwell International Limited
Governor Pull-Through
Forces
The governor has a brake actuated by the falling of the “drop weight”. This traps
the governor rope between a pivoted jaw and a spring loaded jaw. Both jaws are
case hardened and have undercut semi-circular groove profiles.
The brake incorporates the same underlying technology used in the VG rope
brake where braking force is dependent on the spring force and groove profile.
The standard governor has a minimum braking force of 500 Newton’s in both
directions based on 4 compression springs and a 50% undercut groove.
The braking force can be increased to over a 1000 Newton’s by fitting 6 springs
and increasing the undercut to 75%. As part of the documentation of the
governor, the actual pull through force will be recorded on the CE plate.
VG OSG Control Box
(VGOSG-CB01A)
The controller will be enclosed in a plastic enclosure suitably rated for the lift
control room. It is approximately 289mm long x 239mm tall x 108mm deep.
With the exception of replacing the battery every 3 years it does not require any
maintenance, other than periodical testing and inspection in accordance with
your site risk assessment and the lift regulations.
It contains safety relays, visual and audible indicators, wiring connectors,
emergency stop button, key switches, battery, power supply and fuses.
The VGOSG-CB01 controller has been designed and constructed to comply
with all current CE requirements, i.e. EMC, Low Voltage, RoHS, WEEE and more
specifically to meet the requirements of EN 81-1:1998+A3:2009.
Indication of the system status will be provided by LED’s i.e.
a) Reset Mode Enabled,
c) Set OK
d) Warning / Fault Detected
e) Overspeed Detected
f) Unintended Movement Detected
g) Doors Closed
h) Motor Running
The VGOSG-CB01 has two switches and one push button, one is an emergency
stop button, when this is pressed the VG OSG will be immediately deployed. The
key switches require a key to operate them; this is because regulations require a
competent person to reset the VG OSG in the event of a deployment or the need
to carry out hand winding operations. So to prevent any unauthorised tampering
or resetting or bypassing of the system a key is used. We supply 2 sets of keys
per system (4 keys in total); these should only be made available to competent
persons. One key switch will allow the remote reset of the VG OSG (any VG
rope brakes or VG safety gears are set in the normal way) and also to bypass
the unintended movement detection during maintenance. Please note that
overspeed detection will always remain in operation.
An audible alarm is included within the VGOSG-CB01 controller; this will beep
when in the bypass mode.
The other key switch is to activate either the Test or Hand-winding functions.