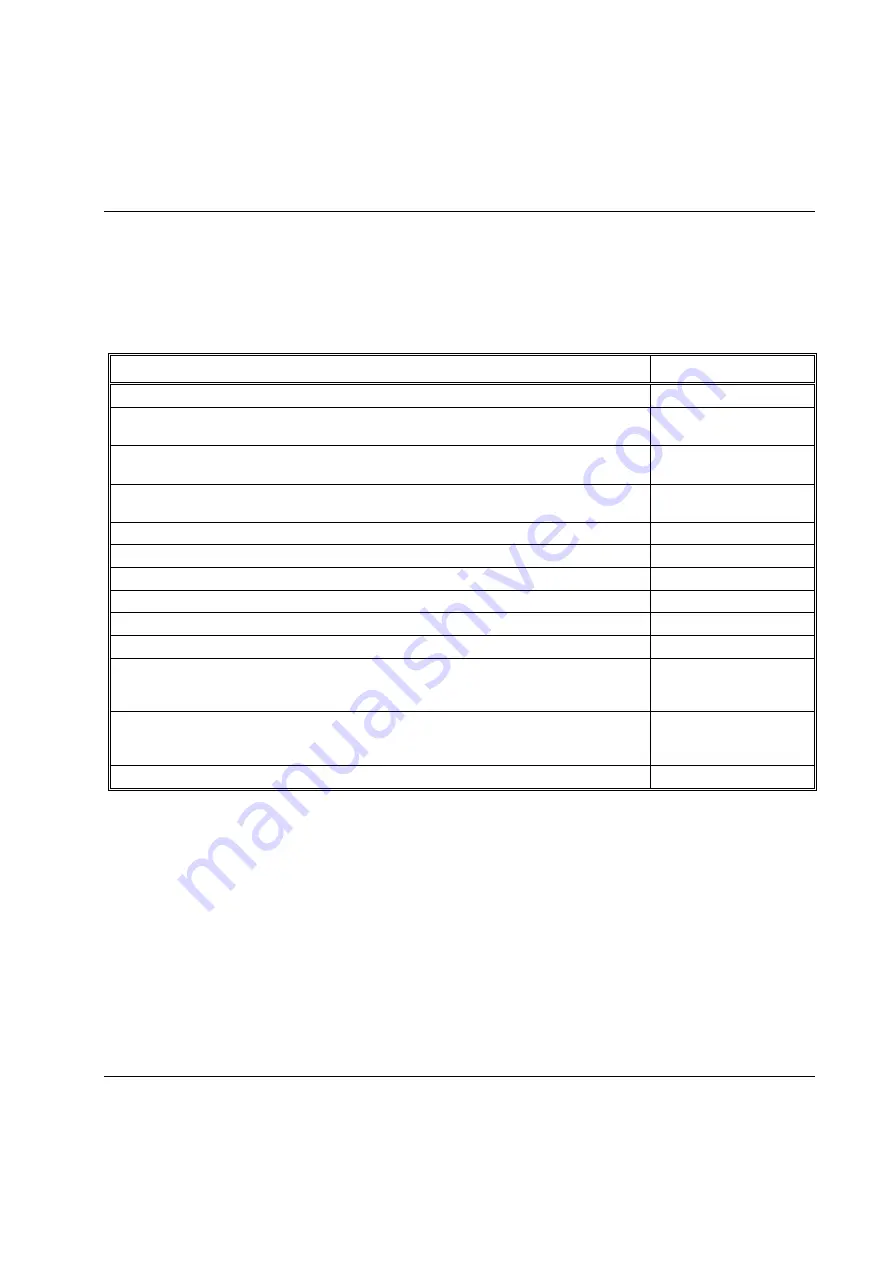
Specification
9836 3521 01
623
9
Specification
9.1
Specification
This part is the specification of the system. It describes general performances of a complete system:
Topic
Performance
Max. time from start signal until all spindles are running
50 msec..
Max. time from last spindle stops a step until all are running in the next step:
50 msec. + monitoring
time.
Max. time from last spindle stops last step until OK/NOK status on digital output, per
spindle and total:
0.1 sec. + monitoring
time.
Max. time between cycles
0.5 sec at limited data
reporting.
Position accuracy
0.5 degrees.
Sampling frequency
1000 Hz
Stations per system.
1
– 15
Spindles per system
1
– 50
Delays in set values to servo
2 x sampling time
Maximum time for a loop in the PLC program
5
Maximum number of cycle data stored in the system
Depends on number of
bolts and variables
included.
Traces per spindle. Each trace with 2000 values for angle, torque and current.
Up to 300 (depends on
length of trace and curve
form)
Max time to change a device
3 min
The Performance values can be seen as a realistic estimate of performance for the finalized system, but
the design of the system is focused on reaching the Target values.
Traces will be stored in two circular buffers with equal size, one for OK cycles, the other for NOK cycles. A
new trace will overwrite the oldest stored trace, independent of tightening program.
Summary of Contents for PowerMACS 4000
Page 2: ......
Page 46: ...System Architecture 46 9836 3521 01...
Page 267: ...Tightening 9836 3521 01 267...
Page 400: ...Tightening 400 9836 3521 01...
Page 486: ...Peripheral Devices 486 9836 3521 01...
Page 622: ...Peripheral Devices 622 9836 3521 01...
Page 664: ...References 664 9836 3521 01...
Page 668: ...9836 3521 01 2010 11 Edition 10 3 0 www atlascopco com...