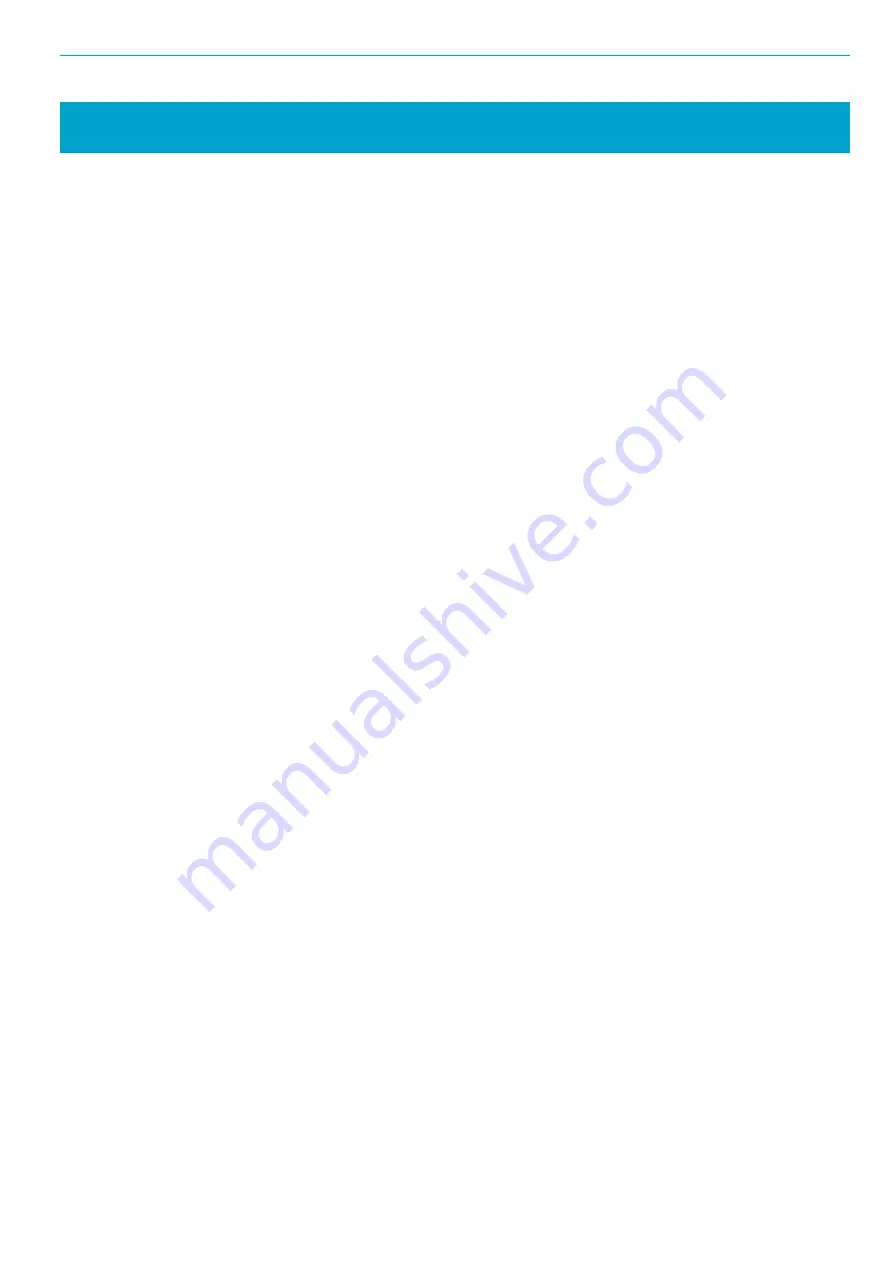
ETD MT41-100-I06
EN
Operation
© Atlas Copco Industrial Technique AB - 9839 1064 01
9
Operation
Ergonomic Guidelines
Consider your workstation as you read through this list of general ergonomic guidelines to identify areas
for improvement in posture, component placement, or work environment.
■
Take frequent breaks and change work positions frequently.
■
Adapt the workstation area to your needs and the work task.
■
Adjust for a convenient reach range by determining where parts and tools need to be located to
avoid static load.
■
Use workstation equipment such as tables and chairs appropriate for the work task.
■
Avoid work positions above shoulder level or with static holding during assembly operations.
■
When working above shoulder level, reduce the load on the static muscles by lowering the weight
of the tool, using for example torque arms, hose reels or weight balancers. You can also reduce
the load on the static muscles by holding the tool close to the body.
■
Take frequent breaks.
■
Avoid extreme arm or wrist postures, particularly during operations requiring a degree of force.
■
Adjust for a convenient field of vision that requires minimal eye and head movements.
■
Use appropriate lighting for the work task.
■
Select the appropriate tool for the work task.
■
In noisy environments, use ear protection equipment.
■
Use high-quality inserted tools and consumables to minimize exposure to excessive levels of vibra-
tion.
■
Minimize exposure to reaction forces.
■
When cutting:
A cut-off wheel can get stuck if the cut-off wheel is bent or not guided properly. Use the correct
flange for the cut-off wheel and avoid bending the cut-off wheel during operation.
■
When drilling:
The drill might stall when the drill bit breaks through. Use support handles if the stall torque is high.
The safety standard ISO11148 part 3 recommends using a device to absorb a reaction torque
above 10 Nm for pistol grip tools and 4 Nm for straight tools.
■
When using direct-driven screwdrivers or nutrunners:
Reaction forces depend on the tool settings and joint characteristics. Strength and posture deter-
mine the amount of reaction force that an operator can tolerate. Adapt the torque setting to the op-
erator's strength and posture and use a torque arm or reaction bar if the torque is too high.
■
In dusty environments, use a dust extraction system or wear a mouth protection mask.