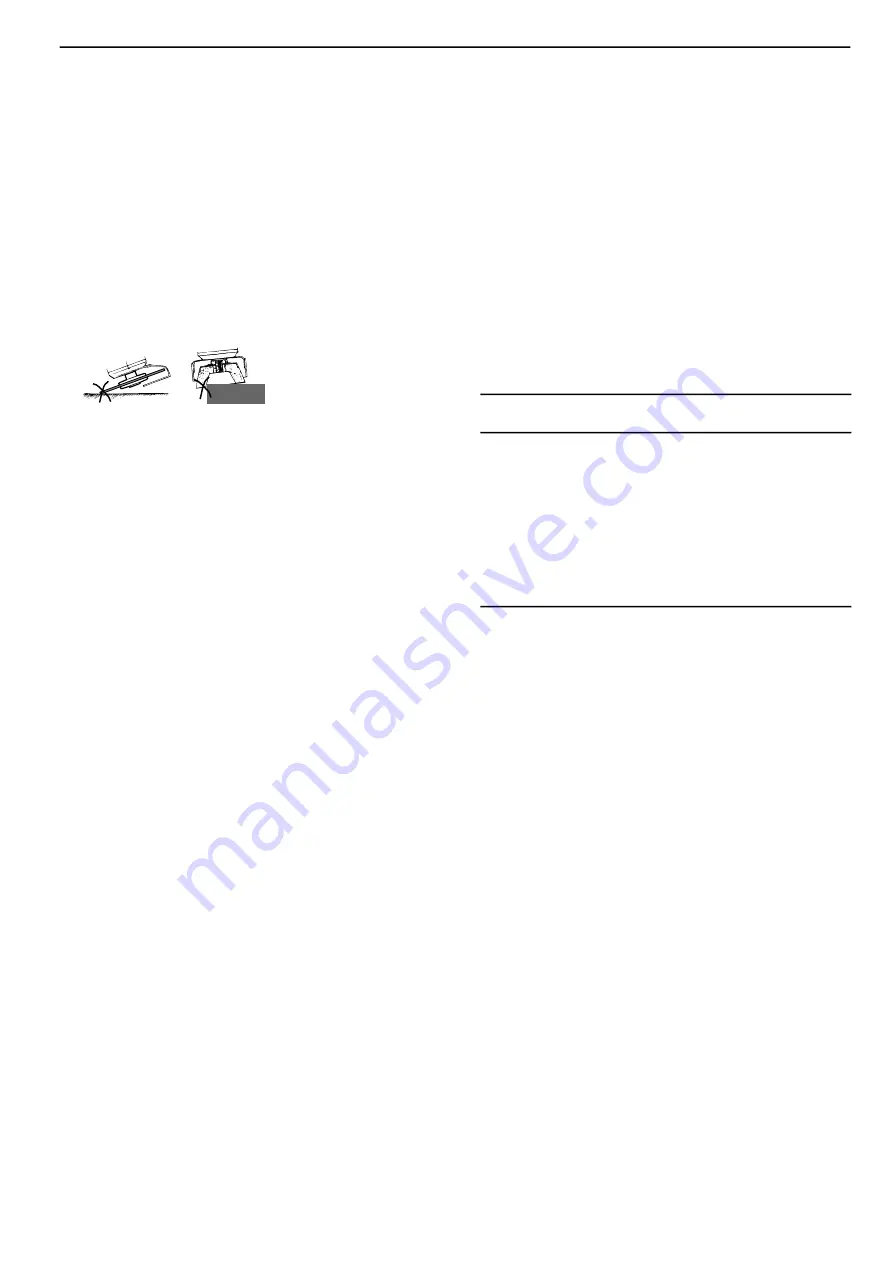
►
Personal protective equipment must be used as
described in Section
Personal protective equip-
ment
►
Slip/Trip/Fall is a major cause of serious injury
or death. Watch out for excess hose left on the
walking or work surface
►
Proceed with care in unfamiliar surroundings.
Hidden hazards may exist, such as electric or
other utility lines
►
Maintain a balanced body position and firm foot-
ing
►
Do not side grind with cutting off wheels and
straight wheels or with inside of cup wheels
►
React quickly to excessive vibration due to dam-
aged, or improperly mounted insert tool
►
Keep away from rotating drive spindle and abras-
ives. Rotation may continue for several seconds
after the throttle has been released. Do not lay the
tool down until rotation has stopped
►
Observe that stored compressed air in the hose
may cause an accidental start
►
Release control device if the energy supply should
fail
►
If a grinder fitted with an abrasive wheel is
dropped, the wheel must be thoroughly examined
before reuse
►
Disconnect from power supply before changing
wheel or servicing
►
Always keep the tool in a dry and clean place
when not in use
Broken grinding wheel
If grinding wheel is broken, a careful investigation
shall be made by the user to determine and correct
the cause.
If the failure occurs while the tools is in operation,
the wheel manufacturer and the tool manufacturer
should be notified promptly.
Maintenance
Rust protection and internal cleaning
Water in the compressed air, dust and wear particles
cause rust and sticking of vanes, valves etc.
This can be solved by lubricating with oil (a few
drops), running the machine for 5-10 seconds and
wiping off excess oil with a cloth.
Do this before
longer standstills.
Lubrication
The machine is fitted with an angle gear which is
lubricated with a semi-fluid grease to ensure good
wear resistance. To avoid overfilling, which could
result in a rise in temperature and damage to seals,
there is no lubrication nipple. Instead, the grease
should be changed after about 200 running hours by
removing the angle-gear spindle.
A
Do not use ball bearing grease or chassis
grease.
Lubricating guide
Use lubricants of good quality. The oils and greases
listed in the lubrication table are examples of lubric-
ants that can be recommended.
Air lubrication
General purpose
Bearings
Brand
Energol E46
Energrease LS-EP2
BP
Spheerol EP L2
Castrol
Arox EP46
Beacon EP2
Esso
Chopin 46
Rembrandt EP2
Q8
Almo oil 525
Mobilegrease XHP 222
Mobil
Tonna R32
Alvania EP2
Shell
Aries 32
Multifak EP2
Texaco
BR2 Plus
Molycote
Overhaul
T
WARNING Overspeed could result in serious
injury or death
►
If speed governor is used, check that correct speed
governor is assembled. Careless handling may put
it out of order
►
Do not disassemble security parts, e.g. speed
governor or overspeed shut-off. These parts must
be completely replaced when damaged
►
Always check the free speed of the machine after
service. See Section
Preparation before using the
grinder
For preventive maintenance, the grease in the angle
gear should be changed after roughly 200 hours of
operation. See the directions under
Lubrication
.
The entire machine should be checked regularly
at six-months intervals. If it is in heavy duty service
or not running properly it should be taken out of
service more often for inspection.
Check the sealing lip and adjacent column for
wear. The seal is essential to keep lubricant in the
gear box.
The strainer at the air inlet should be cleaned fre-
quently to prevent clogging and decreased capacity.
7
© Atlas Copco Industrial Technique AB - 9836 3995 00
Safety and operating instructions
EN
G2515
Summary of Contents for 8423 0316 05
Page 81: ...T T T T T 81 Atlas Copco Industrial Technique AB 9836 3995 00 EL G2515...
Page 84: ...T 30 T Atlas Copco Industrial Technique AB 9836 3995 00 84 G2515 EL...
Page 97: ...T T T T T T 97 Atlas Copco Industrial Technique AB 9836 3995 00 RU G2515...
Page 100: ...T 30 T Atlas Copco Industrial Technique AB 9836 3995 00 100 G2515 RU...
Page 104: ...Atlas Copco Industrial Technique AB 9836 3995 00 104 G2515 RU...
Page 171: ......