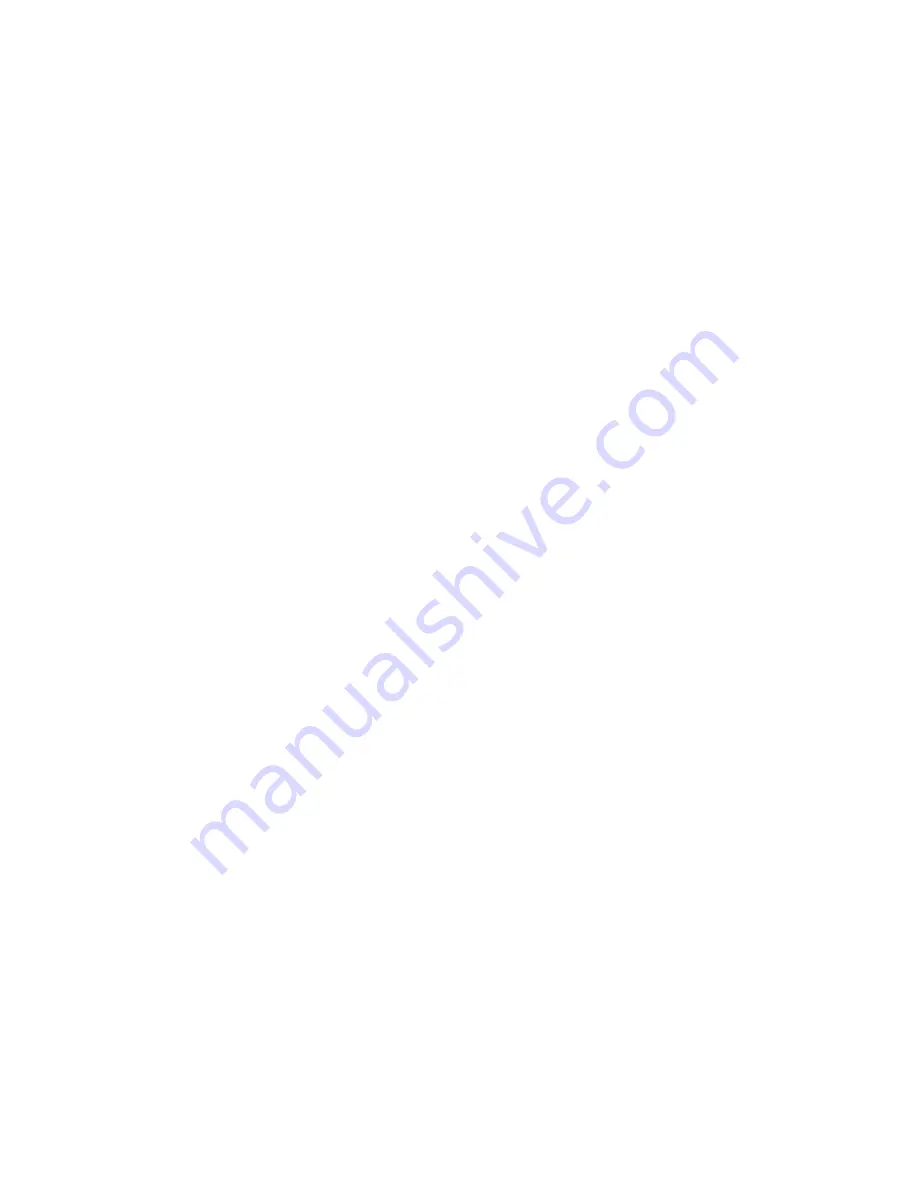
POWERING UP THE TEST SYSTEM
Before applying power the voltage adjustment knob on the front panel of the printer should
be turned fully counter-clockwise. This ensures that the applied voltage is below the maximum
value recommended for the printhead.
NOTE: If the voltage adjustment knob is positioned near maximum, the over-voltage
protector may shut the printhead power supply off. To reset the supply turn the voltage down,
turn the system off, and after several seconds restart the system.
Apply power by turning on the switch on the left side of the back of the test controller and also
turning on the switch on the right side of the computer. It is a good idea at this point to press the
reset button on the right side of the test controller front panel to ensure synchronism between the
two CPU's.
LOADING THE MEDIA
The test system mechanism is designed to accept a variety print of media, both thermally
sensitive and thermal transfer receptor stock. The media path is determined somewhat by the
nature of the media under test and the configuration of the supply. When testing media
narrower than 8 inches the media should be attached to 8.5 inch paper backing, this prevents the
printhead from firing directly against the platen roller.
The media should be oriented such that the side to be printed on faces up as it passes between
the printhead and platen roller. Printhead pressure should be released by rotating the cam lever on
the right side of the head mounting mechanism. The media should be fed in from the back side
of the printer. If the media is wound on a core, mount the two appropriately sized core plugs
into the ends of the core, slide the mounting shaft through the center and insert the shaft into
the slots in the supply mounts at the rear of the mechanism. Core plugs are provided for 1, 1.5
and 2 inch cores. Be sure that the brush side of the back tension plate is in contact with the roll of
media.
Media may be fed to the platen in either of two paths depending on the amount of back tension
necessary to prevent the target media from wrinkling. For lighter tension, thread media under bar
"C", between printhead and platen, and finally under the tear bar. If the media tends to
wrinkle during printing, additional back tension may be necessary. This may be achieved by
threading the media over bar "A" prior going under bar "C".
For sheet feeding and for very thick media, the supply mount may be in the way. The supply
mounting brackets may be eliminated by removing the two screws holding them to the base plate.
If difficulty is encountered in threading the media the feed button on the front of the printer
may be pressed. This will cause the print roller to spin, assisting in the paper threading process.
Slide the paper to both center and align it with the printer. Apply printhead pressure by
turning the cam shaft lever to the down position.
Refer to APPENDIX A for a loading diagram.